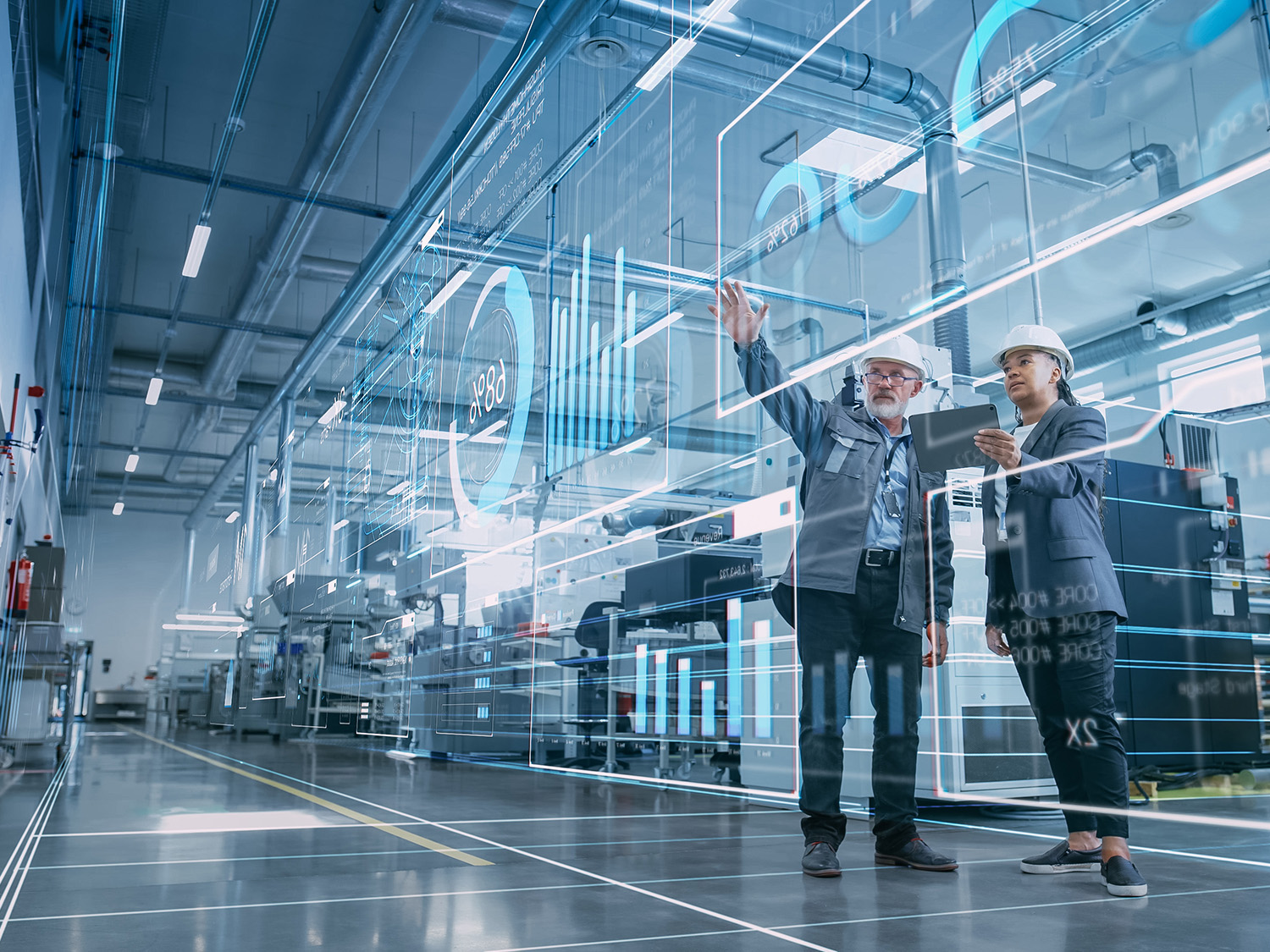
Otis Robinson speaks with postgraduate researcher Rachel Cox about the industry shift towards socio-technical priorities; the bolstering of human centricity within digitalisation; and how Industry 5.0 can benefit business.
A shift towards the Fifth Industrial Revolution is on the horizon in the textile & apparel (T&A) industry. Reflected in new ethical considerations and a shirking of economic focus in favour of societal value, Industry 5.0 could revolutionise manufacturing across the globe.
Industry 5.0 is an emergent phase of industrialisation that prioritises human centricity in the workplace, the relationship between humans and machinery, and the enhancement of the industry for all involved. Ultimately, it ditches the productivity-focused model of digitalisation and strengthening ideas of the dark factory in Industry 4.0 conversation in favour of a worker-centric industry with socio-ecological priorities.
It’s a remarkably rapid but necessary development to the still relatively new-born Industry 4.0. Rachel Cox, a postgraduate researcher at the University of Manchester, UK, notes that perspectives on industrialisation and technological progress are influenced by a framework based on the European and North American Industrial Revolutions. This is an important distinction to make, since many locations around the globe still lack the digital infrastructure to implement Industry 4.0 to begin with. Nevertheless, Industry 5.0 is becoming a buzzword in the European industry – and, specifically to Cox, the UK’s industry – and the drive has genuine and hopeful intentions to better the T&A sector.
Academic perspectives
Cox is a second-year postgraduate researcher at the University of Manchester. Cox’s PhD thesis, titled ‘The future of sustainable manufacturing within the UK fashion and textiles industry’, was inspired by the contemporary UK T&A industry, where stories of worker exploitation and poor working environments run amok.
For example, in 2020, campaign groups in Leicester argued that poor working conditions in garment factories bolstered the spread of Covid-19. Meanwhile, previous reports revealed that many factories in the area had underpaid labourers and time pressures placed on suppliers by leading brands were a major contributor to exploitative working conditions.
Cox accredits these negative characteristics of the UK’s textile industry to complex contemporary business models such as fast fashion, which prioritises productivity and economic success over social and environmental sustainability. Doubly, the pervasive nature of the mistreatment of T&A industry workers is emboldened by digitalisation, or Industry 4.0, which developed out of a desire to meet those economic needs – without consideration for its effects on garment industry workers.
As such, Cox’s PhD aims to explore the impact of digital technologies on garment workers, subsequently providing a voice to industry labourers, and touches upon Industry 5.0 as an emergent industrialisation concept and alternative to Industry 4.0’s arguably detrimental approach to production.
Although much Industry 4.0 critique exists primarily within academia, the European Commission (EC) has addressed this directly, bringing the term Industry 5.0 directly to the attention of industry. The EC explains that, for Europe to remain “the engine of prosperity”, its industry must lead digital and green transitions.
The EC says this means industry must embrace Industry 5.0 to aim “beyond efficiency and productivity as the sole goals”, reinforce “the role and the contribution of industry to society”, and place “the wellbeing of the worker at the centre of production processes, [using] new technologies to provide prosperity beyond jobs and growth while respecting the production limits of the planet”.
Human centricity
Cox explains that Industry 4.0 is undeniably beneficial in many regards, highlighting its ability to protect workers, remove dangerous jobs and support workers with accessibility issues: “[Industry] 4.0 technology has its place – it’s really important and does have a lot of benefits. But as we’ve seen, there’s also a lot of rubbish.”
Today, the industry at large believes digitalisation minimises detrimental environmental and social impact – and there is evidence to suggest it does. But Cox draws attention to metawashing, an emerging trend in industries whereby brands spend more time and money on discussing and marketing virtual products or processes – for the accolade of implementing sustainable processes – than properly addressing its impact on people and environment. Much like greenwashing, metawashing has become a reliable mask for brands and manufacturers to don while avoiding responsibility.
Cox elaborates that phenomena such as metawashing take away valuable focus from systemic issues caused by the cultural use of technology. For example, digitalisation successfully bolstered production efficiency, consequently supporting fast and faster fashion, leaving competitivity and high output numbers as prerequisites for brands and manufacturers. The resulting influence on garment industry workers and the working culture is that high production speeds are now expected from manual labourers.
Cox elaborates: “When we order things [online], someone can press a button and have something delivered the next day. When we look at it on a macro level, this [must] have an impact on somebody somewhere. Instead of having a few days [to produce a product], someone has ordered something for the next day. That is a complete change in time and speed [for a labourer].”
This, according to Cox, suggests a misuse of technology and a lack of consideration for the impact of its implementation on workers and the environment. Industry 4.0, then, may have jumped the gun before industry considered its impact en masse.
As a result, it is important to start questioning the motives behind and end-goals of contemporary digitalisation. According to Cox, “Industry 5.0 is an opportunity to actually question what technology is, and the purpose of it,” and its relationship to labourers and the environment.
Apprehensive for Industry 5.0 to be misconstrued as technophobic, Cox adds that Industry 5.0 is “exactly what Industry 4.0 is, [but] it just puts the brakes on and prioritises human/computer interactions and worker centricity”.
“[For example,] even with automated processes, you still need someone to be there,” says Cox. Therefore, an important question to ask might be: In implementing automation and other Industry 4.0 technologies, are businesses consulting the garment workers who will be working closely with these technologies?
From an academic perspective, Cox hopes to work closely with industry to investigate these manual labourer perspectives on technology implementation. Their project will prioritise this worker voice, exploring evidence of poor working conditions too.
Widening the stakes
The project aims to highlight manual labourer priorities and preferences in the industry. If their voices are considered during the technology adoption conversation, opportunities can arise for both businesses and individual workers. For example, the upskilling of labourers – who are required to increase their technological literacy to work closely with machinery – could be incredibly beneficial to workers. Meanwhile, by making it clear that staff are a priority in said conversations – and an indispensable part of production – manufacturers can build better longstanding relationships with their colleagues and stronger advanced production processes.
And today, there exists a lack of inclusion for garment workers when it comes to decision-making, states Cox. But in considering labourer voices in digitalisation plans, they can become key to decision-making processes, thus democratising the process altogether – and perhaps even chipping away at the unjust hierarchy of the industry at large.
“Normalising that as a process, normalising empathy within engineering and technology and physical science spaces [is important]. You can’t dissociate and detach the social from the technological. People are involved in the process [of digitalisation], and to get those voices really involved is important.”
Cox concludes: “[Industry 5.0] can benefit businesses to prioritise socio-ecological considerations. Unfortunately, [as it stands] with fast fashion, which is focused on short-term profits and not long-term, many businesses are not focused on the long-term.”
Have your say. Tweet and follow us @WTiNcomment