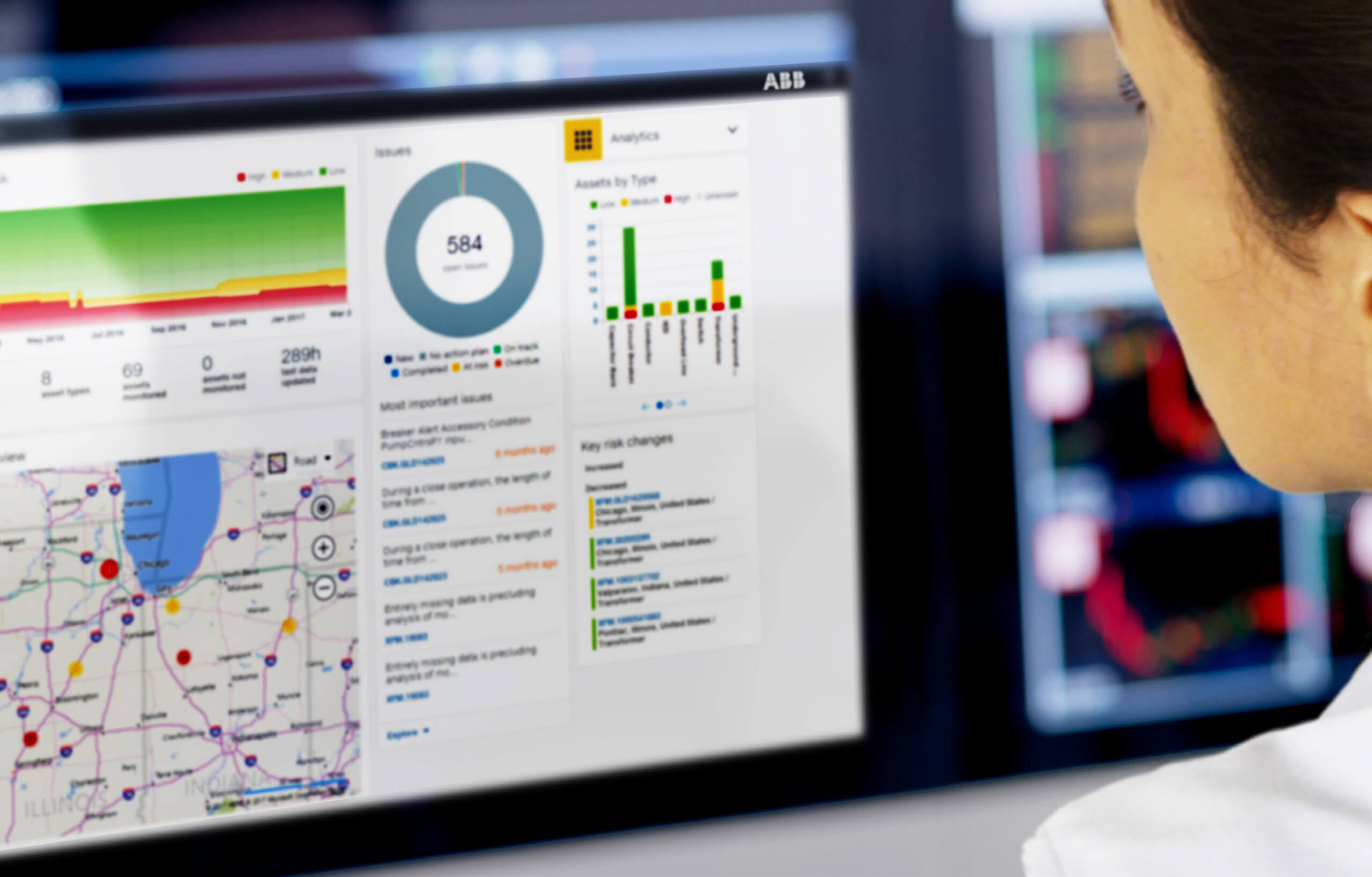
Predictive maintenance is often the gateway to Industry 4.0 for many companies. It is an easy point in which to start digital transformation as it is relatively cheap, can be used on existing technologies and return on investment (ROI) can be easily and quickly observed.
ABB is a global technology company at the forefront of Industry 4.0, delivering systems that drive efficiency and savings, as well as offering multiple other benefits to support operators in an ever-competitive energy landscape. Pier Vittorio Rebba, global technology manager, Power Generation and Water, and Will Leonard, product manager, Asset Performance Management from ABB’s Energy Industries team explain the untapped potential of a digital maintenance strategy across all verticals.
Predictive maintenance
Predictive maintenance monitors the performance and condition of equipment in real-time. It predicts the future failure point of a machine component so that the element can be replaced, based on a digital maintenance strategy, before it fails. In doing so, equipment downtime is minimised and the asset lifetime is maximised, according to ABB.
The company works on predictive maintenance and asset management across many industries and sectors, including power and water, oil and gas, process industries, marine and robotics. Wherever there is a critical machine that is performing a task via a process, you can consider applying predictive maintenance, such as in the textile industry. In essence, ABB can use predictive maintenance across all industry sectors.
Rebba and Leonard say: “The challenge rests in the question: ‘Can we solve the biggest industrial challenges by applying predictive maintenance solutions that may involve smart sensors, real-time monitoring and advanced analytics?’ This often depends on the current strategy adopted, the age and residual life of an asset, and of course, the maintenance strategy of the company in question.”
They continue: “Increasingly, operators are challenged to build infrastructure and make investments that last for future generations. This often means examining how to maximise the performance and efficiency of operations for a facility set to run for the next 20 years.”
As a result, operators are consistently looking upfront for “how to employ best philosophies for maintenance and switching from a time-based maintenance program to a condition-based predictive one. With rapid improvements in technology and operations, a facility can even pave the way for predictive, prescriptive or even autonomous operations,” according to Rebba and Leonard.
Influential driver
Digital technologies are driving innovation and predictive maintenance has been labelled as the ‘biggest driver behind digital transformation’. Rebba and Leonard say this is because predictive maintenance has “untapped potential.” They add: “Most operators are still using a time-based maintenance system, even though studies show most equipment failures or maintenance issues are not, generally, a result of time-based conditions.
“Predictive maintenance allows operators to monitor, in real-time, the condition of their assets, and therefore accurately predict possible problems before they happen, avoiding costly and unplanned shut-downs and downtime. This added reliability can have a substantial impact on OPEX [operating expense], with maintenance savings of between 15-30% achievable.”
Moreover, with improved visualisation of assets and their performance, operators can make informed decisions about how to create efficiencies and implement energy management programs that reduce fuel consumption and emission levels, while not affecting production yields. “This is another driving factor in adopting a predictive maintenance strategy,” Rebba and Leonard comment.
Also, as the ageing workforce reaches retirement, which is particularly true of the textile industry, a digital maintenance strategy can help ensure plants continue to run smoothly and ensures knowledge transfer from peer to peer, therefore future-proofing facilities for the long-term.
The next step
When it comes to machine monitoring, more than one approach is needed to get the most out of the solution. “What is increasingly powerful now is a combination of data-driven analytics with a model-based approach,” Rebba and Leonard say. They explain: “A simple mathematical approach using data and statistics is good for early warnings, but not so good for identifying the behaviour of specific components or the causes of failure. Deep machine learning, where neuro learning is utilised, enables the network to continually improve and recognise anomalous behaviours, by leveraging physics-based models that are reliant on knowledge of specific products and systems that change from plant to plant.”
Ideally, a combination of intelligent systems is the best approach to get the most out of a monitoring solution. “That way, not only can anomalous behaviour be identified and warned, but it can also provide actionable recommendations,” Rebba and Leonard continue.
Asset management
Advanced analytics with the use of data are enabling experts to provide insights into predictive maintenance and asset management, which positively impacts business, improves risk management and avoids long-term problems. “Put simply, quicker and better insights drive competitive advantage,” say Rebba and Leonard.
Asset management allows manufacturers to get the best out of their machinery, increasing operational efficiency. It is therefore a critical part of digital optimisation.
Now is the time
Today is the right time to invest in technologies such as predictive maintenance, machine monitoring and asset management. The maintenance market is more accessible than it has ever been with product maturity. “The technology architecture and predictive maintenance and asset management systems are here and ready to be deployed,” say Rebba and Leonard.
“Industrial operators have always been aware that it was a big area for improvement, but with more and more focus on reducing cost, risk, improving reliability and in the drive to become more sustainable and efficient to compete, it must become a key component of operational strategies,” they continue.
This is where ABB’s technology comes in. Using machine learning, ABB offers innovative predictive maintenance solutions utilising sensors, data and advanced analytics to constantly assess the real-time condition of assets, identifying when they might need repair or replacement well ahead of potential failure.
“Our ABB Ability Asset Performance Management (APM) software helps companies to more accurately predict and prevent/reduce equipment and infrastructure failures, enabling more efficient planned maintenance practices through predictive maintenance,” Rebba and Leonard claim.
However, predictive maintenance needs a holistic approach. “It is not just about addressing one issue or providing one solution in isolation,” say Rebba and Leonard. “Operators need to look across the entire plant. It requires full integration within a whole system – it’s about monitoring all processes, components and people and interconnectedness with other critical plant systems and IT like, for example, the Manufacturing Operations Management (MOM) process.”
More than ever, operators are being challenged to maintain high asset availability, reliable capacity and safety with the financial pressures caused by ageing infrastructure, and the limited capital for maintenance or replacements. “Implementing a solution that combines an asset management system with asset performance data and a comprehensive workforce management solution for dispatching crews helps companies achieve a proactive approach to maintenance,” Rebba and Leonard add.
And it is not just about technology. A culture shift and the education and training of people are also required to embrace a change in process around infrastructure management and maintenance.
Also, Rebba and Leonard comment: “Understanding what an organisation’s digital strategy is, and where they are on their digital journey, is very important. When it comes to maintenance, is an organisation reactive or proactive? Are they preventative, predictive or prescriptive? How reliable are they? What is the next step for them in the process to becoming world-class in asset performance management?”
ABB helps its customers to get value from data. The company invests in R&D – nearly US$1.5bn every year – and has the expertise to work with its customers to find digital solutions that meet their potential problems, lowering risk and reducing capital and operational costs by 20-30%.
“Asset performance management is one of ABB’s key areas of business, where we are helping our customers transform routine maintenance to predictive maintenance by making better decisions and understanding risk and failure. This is an approach that is revolutionising monitoring and maintenance,” Rebba and Leonard conclude.
Have your say. Tweet and follow us @WTiNcomment