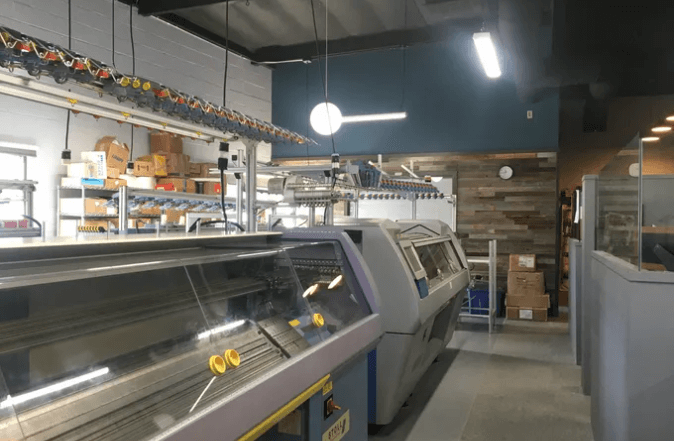
Ep. 49: Knitting industry significantly lacks skilled engineers
By Jessica Owen
In this episode of The WTiN Podcast, we talk to Connie Huffa, textile engineer and co-founder of Fabdesigns.
Founded in 1988 by husband-and-wife Bruce and Connie Huffa, Fabdesigns is the go-to company for all things knitting. The couple have spent decades developing cutting-edge 3D knitted products, reimagining machinery, innovating parts and materials and teaching these new technologies to brands, individuals and engineers across the world.
In this episode, Huffa explains the interesting story about how Fabdesigns came to be and what the company does in more detail. She talks about Covid-19, how knitting machines have evolved since she first started out at 19 years old and what she’d like to see from the next generation of machines moving forward. Elsewhere, she highlights the lack of advanced expertise in the industry saying that “digitalisation is putting the tools in more people’s hands who don’t know how to knit” and that knitting machine manufacturers need to set up training programmes that go beyond the basics.
Have your say. Tweet and follow us @WTiNcomment
-
Transcript
This transcription has been AI generated and therefore may have some inaccuracies.
Ep. 49: Knitting industry significantly lacks skilled engineers
In this episode of The WTiN Podcast, we talk to Connie Huffa, textile engineer and co-founder of Fabdesigns.
Jessica Owen
Hello. My name is Jessica Owen, and I am the Deputy digital editor at WTIN, and this is the WTIN podcast, the fourth industrial revolution is underway, and the world of textile and apparel is just one industry that is benefiting from new and innovative technologies. With this in mind, for this series, I'll be talking to companies across the textile apparel landscape about their new technologies, the benefits of digitalization, and the advice that they'd give to others who are trying to implement such solutions.This week, I am joined by Connie Huffer, who is the co founder of FAB designs. Connie has a wealth of knowledge concerning the knitting industry, and she talks about everything from the lack of advanced skills in the sector, how COVID 19 has disrupted the industry, and what she'd like to see from the next generation of knitting machines.
Well, hello, Connie. Lovely to speak with you today all the way from the States, I understand. So how's life with you?
Connie Huffa
We are very good here. I think it's 70 degrees here in Southern California, and thank you for having us. And we love the UK. And as you know, my husband is actually from the UK, so we're looking forward to visiting again soon as this COVID is over.Jessica Owen
Yes, yes. Well, we will come on to COVID later on, because we can't escape that topic at the moment. But it's good to hear that you're all well over there. Great.So today, then we're going to talk a bit about digitalization within knitting and the industry and so on. But before we go any further, please tell me all about your company, fab designs. Then, I mean, I think I understand that you and your husband started it together. Is that right?
Connie Huffa
Yeah, we actually did. We started in 1987 actually was January of 88 Bruce and I actually worked for Stoll and when we were pioneering the west coast. So we set up a lot of the industry here. We taught and sold machinery, did a lot of the programming here. Actually did all of it. We did all the customer service. So we spent a lot of time together, and we started dating after about six months, and we started buying a property together. Well, once the paperwork hit the office,I got fired immediately for getting engaged, and Bruce got a a telegram on the Friday, same day that he had to be back in New York, nine o'clock.
Moved, relocated. No relocation services. He had to move himself, or he was fired as well. So when that happened the same day I went downtown, into Los Angeles City Hall and filed a company. So I started the company basically the same day I was fired. Because what am I going to do? I stranded here in Los Angeles. I actually moved from Philadelphia to work for stole here in Los Angeles, and there weren't a lot of companies. All the companies that were in the knitting industry that had flat knitting were companies that we had sold machines to or trained and they were startups. So, I mean, I was basically overqualified to work at a lot of these these companies. So
Bruce and I ended up helping a lot of these companies, and the companies were very loyal to us because we were putting money in their pockets teaching them accelerating their learning curves. I don't know if anybody's had one of these machines or seen one of these machines, but they're massive, and they're a combination of electronics and software and mechanical parts that are all controlled by computers. So there's a lot of moving parts that make the knitting process actually happen. So all these fine tuning of these individual parts takes a lot of experience and takes a lot of time to actually get your hand at and develop a comfortability with working them. So a learning curve on these machines, whether anybody wants to say it or not, it's about 18 months to just get the basics down, where you're comfortable not jamming up the machines and and can actually make product.
And what we were doing was actually teaching the people on the product they were making, rather than teaching the library that the machine builder gives, because it's very basic and it's not really marketable. So to actually teach people they can actually sell almost immediately, is what we started doing here in Los Angeles.
And that's basically what we've continued doing over the last 30 years that we've been in business, is actually teaching people what they want to know, rather than a script or a formula of this is, this is a basic piece, and then basically they're not making any money.
So that's, that's what we did probably about six months into that, mister still found out what happened, and he offered us our jobs back by then, it was way too late. We were we were already invested. We already hopped all our credit cards and basically been on our own for six months. And it was tough, you know, but we we managed to do it with the assistance and the loyalty of the customers here in Los Angeles and then across the country as they learned. What happened?
Jessica Owen
Well, I did not know. That's how you started. I assumed that. Well, I don't know what's I've seen, but it wasn't that.Connie Huffa
Yeah, I was I was 24 at the time and Bruce was 26 so we're two years apart. So you can imagine 24 year old and a 26 year old that were stranded here in Los Angeles. Now, a lot of things the other a lot of people don't know is that Bruce was on a visa, and he could not work for any other company, but still, and a lot of the people at the time were also on visas, and that means that they're really captive to the particular company. So if he would have left, he would have had to left the country, and he would have lost his everything he owned. He would have lost his house, he would have lost everything, and they would have basically been deported. We were already getting engaged at the time. We were married six months later, so that didn't happen well.Jessica Owen
I mean, I could probably go on and ask you quite a few more questions about that, but I feel like we should probably stick to, you know, knitting. We'll have to have a separate discussion.Connie Huffa
Our focus is basically helping the customers with the what they want to make, rather than giving them a script of what comes from the machine builders or the libraries from the machine builders. And it's always been that from day one, right? So essentially, you're sort of an expert consulting business for knitting them, really? Yeah, my background is more than just knitting. I basically a textile engineer. So I understand yarns, fibers, polymers, dyeing, finishing, all the sewing, construction, everything from the polymer all the way through to the sales floor. That's that what we do. Yeah, I can completely see how you're overqualified for some of those other jobs.So I mean, you've given me a sort of a broad overview as to what fab designs does then, but can we break it down a bit? So one aspect is that you advise and collaborate with brands. So do they essentially, are they designers that come to you with ideas and basically just can't work out how to put it into reality. Is that the kind of thing you deal with? Yes, we do work with a lot of companies. We work with brands. We work with individuals, inventors, people who have an idea, they have maybe a design brief, but they really don't know how to connect the dots. A lot of manufacturing has left Europe, as well as the US and gone overseas, so people don't have access to what a manufacturing environment is and what manufacturing capabilities are. So you know, previously, this was all like all in one building. You had the sales people, the designers, and you had the factory, even shipping was all in one building. Now this is all over the place. It can be different states, different countries, and a lot of the companies are relying on their factories that are actually doing the manufacturing to source all these different materials. So a lot of the people that are coming to us, they don't even know where to find the materials to make their ideas come to life. So it's it's building not only their product, but it's also building their supply chain. It's also finding what manufacturing capabilities we can actually fit their product into. Because all factories have slightly different footprint, and some tweak things differently than the other. And that's really important. So what we are is basically a sandbox for people to bring ideas. We have state of the art manufacturing equipment and computers. And we also have Bruce, who is basically, like I said, the protege of Mr. Thomas still, who, sadly, we've lost let this last year, but he invented, Thomas stole actually invented CAD before there was Photoshop, and before there was anything to render digital designs into a computer system. So digitalization has actually been on.
These machines since 1978 we actually started with Apple computers. If you can believe that apple to apple to see Apple to Gs, we actually still have some of these. We have couple customers that still use this system, and that actually linked up to 128 machines, and we were able to get reports and things like that. So our system in our company is state of the art, and people can actually work with us on the machines. We encourage people to come and work with us. So they can feel things, touch things, make this stiffer, make this stretch here. I don't like the way this looks. Tweak this a little bit, and they get to actually work on the equipment without actually having to buy it. And then once we work out their project, and most of these technical projects take anywhere from a year, 18 months, sometimes three years, to actually modify the product enough as well as tweak the machine. Because sometimes we have to change needles. We might have to change sinkers. We might might have to change the gap of the needle bed. We might have to add feeders. We might have to add different ways to feed yarns into the machine, depending on what the product actually is. So the machine actually develops along with the product itself.
Right? They don't have to buy equipment during this time, they can just play around on on the equipment we have, and they have expert guidance as to what materials they might be able to use, as well as building their entire manufacturing platform. I like to tell people, the knitting machine is almost like a piano. You've got 88 keys on a piano. There's so many different genres of music. There's so many different ways you can make things happen. And it's the same way for a knitting machine, you can make just about anything on the knitting machine. So whether it's a medical product or aerospace or footwear or even smart clothing, the same machine, base machine, can make it Yes, but you have to tweak different parts of the machine. So that's what people get to use at our place, right? Okay, well, that's such a great service. Then, because I'm imagining a lot of those people probably come to you, work out what they need and what they want, and then they go away and invest in exactly what they need without, you know, I don't know, buying something, this crazy machine that actually they're only going to use a tiny percentage of what it can do, and they just didn't need all that is that kind of what happens exactly. So they they understand their costing, they understand their efficiencies, they understand quality control, and they have their supply chain put in in place before they actually go out and buy machines. Now, a lot of people, they see these machines at the trade show. Oh, this is fantastic. I want to make this. I want to make that. But they buy what the machine builder has, rather than taking the time to actually investigate what type of machine, what modifications to the machine do I need to make. And it doesn't matter which brand, maker, model of machine. It still takes the investigation to see if you can actually make the product that you want to make on the machine. The type of gage, how many needles per inch, the size of the needle is important, the size of the hook is important, the number of feeders, and then also the efficiency. How fast can these machines make this product? Because all the factories that actually make apparel are basically charging you so much per minute. So if you have something that is going to take 10 minutes versus something that's going to take 20 minutes, obviously your costs, just for the knitting alone, are going to be double. So I mean, you said you've been in this business for what, since the 80s then. So how different are knitting machines today compared to when you first started out? How far have they come, and what are they capable of now? I mean, you said they can knit pretty much anything, really, I would say that. Yeah, I started when I was about 19 years old, and I was very lucky to start on a Shima system that was at Somerset netting mills in Philadelphia. Somerset was a pet factory of Shima, and they had the most shimas in the country at the time. And so I had a color system to work on. And so getting Jack guards into the machine was basically a new thing at the time, getting body graphs into the thing, into the machine. Previous generation of machines was 1224, 72 needle repeats, or you had steels on the machine where you had to do positive, negative. So either you had a peg in or no peg in, and that was it, or paper paste boards, and they were very laborious to set up. So everything has changed so much, even from the 80s, the computers have gotten faster. The.
Capabilities of the machines that the memory in the computer systems mean that the jacquards can get bigger and more complicated, or you can put actual garments that take up so much memory into the memory, and you're not going to to lose your program as you're programming that used to be a huge problem. Or you were able to put one or two little 3d features into a garment, but not a lot. You could full fashion. You can shape things, but you weren't able to do a lot of a lot of them, because the memory was so small. I mean, it was 256k we had a megabyte card in our computer system. So So much has changed now. I mean, we can have almost any computer system now. And I mean, we have gigabytes and even terabytes in our our systems that we have 1000s and 1000s of programs in the same computer, and that wasn't possible. The other thing is that the way the computer system processes has gotten much faster, and the mechanical parts on the machine have gotten smaller and more precise. So our feeders are very precise. The ones that are on Steiger and she and Steiger and stole are basically belt driven, and they are independent from the can box. These are direct feed so they're vertical feeds. The yarn feeds from the top of the machine into directly into the feeders. You'll see the shimas and some of the stalls and some of the other tigers. They come from the side and the shazing machines as well in their side feed machines. So all the yarn has to come from the top of the machine to the side of the machine change angle, so you get drag, and then it goes to the feeder system that goes down into the knitting areas. So you've changed angle like three or four times as the yarn is changing. So every time your yarn passes through a yarn guide that's changing the angle. You get more drag, so it's harder to feed more delicate yarns, and you need different types of feed systems, whether it's positive feed or other systems that actually help drive the yarn into the feeder system. Those didn't exist in the 80s and even the early 90s. So taking care of yarn and getting the right system to push your yarn into the machine has been a major plus. Being able to control the speeds of them has also been an advantage, because a lot of this can be computerized and not left to a human error of a knitter, so you can get more precise, repeatable and more consistent in the programming and the feeding of the material into the machine. So that's been fantastic.
The takedown, pulling the yarn, pulling the fabric out of the machine, used to be weights swinging on the bottom of the machine, just holding it as you went one direction and the other. It's, it's been you'd have to make sure you were out of the way, or else it would hit you in the shin or the knee.
But, I mean, that's all digital. Now, we don't have any of that. The used to be where you had to be very low on the machine. They were almost the computers were, I want to say, not even waist high. They were much lower than that, so you had to stoop down. They were not ergonomic at all. The machines have become much more ergonomic, and because things have become lighter, you have more women in our industry. You don't have to use brute force to take a needle out of the machine change a needle bed. I mean, everything has has become touch screen, which is fantastic. You can actually see what you're doing. And the machine is very communicative to you, so it's telling you what's wrong. So you'll get these error codes, and it'll tell you, fix this, do this, oil this, and you get prompts now you didn't have that. You had to rely on the knitting technician to put a maintenance schedule together to make sure he oiled the machine. Somebody oiled it differently than somebody else, and everything was down to human error. So they've gotten a lot smarter. The machines themselves. Well, that's so interesting. I mean, even what you said about women now being in the industry as well, I hadn't even considered that kind of thing.
Jessica Owen
So bearing this all in mind, then what does that mean for the products these days? Can you make a lot of different things? Because, I mean, I think I read that you guys have been sort of responsible for the, say, the fly knit trainers, 3d shoes and so on. So would you say maybe that's one area that you couldn't have done back then?Connie Huffa
I would say that the flying it. Yes, we invented the flying it. And Bruce is on the patents, but he actually invented it. Other people are on the patents. They should not be. We've actually contested this. He used his own foot. But here's the here's the.The thing with the fly knit, it is a fantastic product. It is our best advertisement. What it's done for the industry is made people think differently about knitting. They look at it as additive manufacturing. How can I put stitches materials where they need to be to do a specific function, and that has opened up the industry, in aerospace, in architecture, in healthcare, in other places where knitting wasn't really looked at as a technology. It was looked at as something your grandmom did in a rocking chair, you know. And when people think of knitting, that's what they think of they don't really think of knitting as technology. Now they do so. It's actually changed the industry tremendously, and the perception and people are more willing to try different solutions to specific problems by using knitting. So are there any other sort of products that people are coming to you guys now with that you would never have sort of seen back when you first started composites. We're doing tremendous amount of composites. We actually have several patents pending right now being able to knit carbon fiber and fiberglass Kevlar all together and being able to reinforce it, but knit it to shape so that the you don't have these large panels that you need to cut, you can actually knit at the shape of the mold. You can put structures in it. We can embed wires into it so you can have, say, an entire automobile panel for an electric vehicle that is knit to shape with embedded wire harnesses and channels for Lidar and radar and things like that. So the other alternative, the other part of this is that we're a sustainable company. We try to save as much material as possible. We like to use recycled material, repurpose material.
When you're making some of these things, it is. We had to find places that actually recycle fiberglass. There's a company the US that recycles fiberglass, and there is a company in Germany that actually recycles carbon fiber, because it had to sit well with us to be able to do this, if people could take it apart and be able to reuse it and repurpose the materials, because you're making something that's completely indestructible, and if the bits and pieces that are cut off from these panels. When you're doing traditional composites, they're thrown away. They're not usable for anything else. And we wanted to be able to make something that was knit to shape, but also structurally, you had the integrity of the structure. It actually makes a better composite because it's it's to the shape of the mold, but also when we're finished with it, or when the end life of the product is is at its end, we're able to take it down the supply chain. So if you started with aerospace composites, you can reverse engineer the resins and separate the fibers out and then reuse the fibers for something else. Say it goes from aerospace to automotive, and from automotive it might go to sporting goods, and from sporting goods, it might go to something else you might have in your home that doesn't have a lot of impact or need for as much precision, right?
Jessica Owen
Okay, interesting. And while we're on this topic, then of sustainability and so on.How has digitalization helped when it comes to this topic? Then, because I'm assuming that if you can automate things, and you can now do 3d knitting and things like that, there's a there's maybe a lot less waste going around and so on.
Connie Huffa
It has it. That's a double edged sword, because you have 3d knitting. We only knit with what we actually need and knits to shape. There are very few people in the world that actually can program this, and it doesn't matter which brand, model or make of machine, so you have very few experts that are able to program in 3d the machine builders teach a WYSIWYG what you see is what you get. So when you learn the system and it has cut and paste and its modules that you that basically they've set up and you plug this in here, plug that and they're, they're making sure you're not breaking the machine, and that you can actually knit what you are seeing on the screen. It's not necessarily efficient. Our program, the way we program, is anywhere from 25 to 50% faster, and it, and this system, is actually using more machinery.Be more floor space, more yarn and more waste. So it's actually the opposite. It's, it's really not saving anything. It's, and you have to really spend the time to find out where the waste is coming and build your own programs, and not use the WYSIWYG system. The other thing with WYSIWYG, if the machine builders are teaching people in the UK, people in the US, people in China, people in Ethiopia, the same WYSIWYG software, which company is going to end up getting the product or the order it's going to be, whoever is going to do it for the least amount of price. So it sets up a competition where the lowest price is always going to win anyway. So unless you do something yourself to make it better, to use better materials, to find a way to reduce the waste and the cost, it's it doesn't make any sense. Digitalization is putting the tools in more people's hands that don't know how to knit. That's what's happening today, unfortunately, right? Well, that's so interesting. You say that because I was oblivious to that issue. So you're saying then that there are opportunities for digitalization in the knitting industry to enable a really sort of circular economy. But it's not going to happen unless you've got the people who know what to do the machine the machine builders are interested in selling machines, and they're interested in getting as many machines into the hands of as many people as possible. They're not necessarily is interested in sustainability. They might say they are, but they're not teaching sustainability. They're not teaching reducing waste. They're not teaching using recycled materials. They're not teaching the things that people need to understand and to know. And this is why we do what we do, is because there's a tremendous need out there, and there's a tremendous void of information, of real information, of what people actually want to make, and giving people the tools to make what they want to make, rather than just selling the equipment off the machine floor. So going back then to this issue of there's a lack of education, is there something that could so let's pretend your company doesn't exist and people don't have that option. Is there something that people can go to university for? Are there textile knitting courses that could teach this? So I have had this conversation with people from Kent State, RISD,
NC State, they don't teach, they teach the basics.
Philadelphia is now Jefferson University. People will get the basics. And we've had several grad students come here doing their doctorates and their masters, and honestly, some of the stuff that they're doing in their masters we did in undergrad 30 years ago. The problem is that most brands go to Asia, and they use the sources of the manufacturers there to source the materials, and they rely on the technology at the factories where they are, rather than taking or learning in house, there aren't machine builders have the best place to learn their technology. The schools really don't go deep into the technology. Even when I was learning, I learned the Shima my teacher at was Philadelphia College of textiles and science at the time, didn't I was learning more than she could actually teach, because she was learning at the same time and I was learning in a factory setting. We had Shima there almost every day teaching us directly, and so we knew we knew more on the factory floor than in the colleges. And I would say that's still true today, because the students, really in most of the colleges don't even get to touch the machines because of insurance issues. So they might make the jack art of a program. Somebody else writes the other part and and then a technical person puts it on the machine and runs the machine for them. This is true at fit. It's not true at Kent State. Kent State, the people actually touch the machines. A lot of the colleges are teaching hand knitting on hand knitting machines. This is great. They get to understand how loops and and yarns interact with needles on the machine. They get the basics. But nobody's teaching anything like what is what people want to learn? There's no place for anybody to go to learn this at all. So what, what do you have any sort of ideas and solutions as to how we can sort of fill this gap of knowledge? Again, sort of, I mean, in an ideal world, you could probably, you know, get fab designs everywhere, helping everyone. But I'm.
Mean what? What sort of ideas do you have? There used to be a lot of FAB designs or type companies everywhere, and unfortunately, we were the younger generation at the time. A lot of people have retired, but a lot of people have moved to Portland, Oregon. They've they've given in, and they've given into basically companies that are a specific company that's willing to pay them double or triple what the industry was. And they've taken a lot of people off the market and just to occupy them so that nobody else can can use them. What needs to happen, I think, is that the machine builders need to understand more of what customers, customers want to make, and I think they need to start training programs that go beyond just the basics. I know that Shima was doing things like that as was still they're doing a lot of like the GS they have every year at Shima, brings a lot of people together. I think networking people that understand yarns and understand other parts of the industry and what people are actually doing is very important. We had a summit ourselves for three days. We had people from all over the world come we had 90 people. This is all that we can accommodate in our building at the time. And people came from Copenhagen, they came from the UK, they came from South America, they came from Sri Lanka, they came from China, they came from Germany, all over the place. And there is a real need and a thirst for getting more information about materials, about structures, about putting materials and structures together, about being able to program but also the capabilities of the machine. They need to understand the capabilities of the machine. I think the machine builders can do a better job, you know, I think they'd sell a lot more machines, and they'd have more customers really appreciate what their the industry can do. I know Shima does a great job in in Japan, and stole does a great job in Germany. They also have, I think both companies have satellites in like Carpi in Italy and places like that, and I unfortunately, a lot of the professors were also poached, and they're also in Portland, from a lot of the colleges. So I mean, it's, it's it's just that's the double edged sword of the fly knit. Is that, yes, it made people think about knitting differently, but it also put a spotlight on wanting to get as many people as possible that know this technology, and unfortunately, a great majority of them are in Portland right now.
Jessica Owen
Okay, so I mean, do you think that the industry will ever get to a point where people are well trained and they know what they're doing, or do you think that's just not really on the cards?Connie Huffa
I think they want to. They want to. And I think where there's a will, there's a way we get people that want to learn all the time with this onshoring, where people are trying to bring manufacturing back to Europe and bringing back to the UK and bringing back to the US. I think it's it absolutely people are learning.There are online classes at Shima. There are online classes at Stoll. Honestly, the people need to practice on the machines. Like I said, it's like a piano. They have to practice. If they have the machine. They keep practicing. They get better and better. So yes, I think, I think definitely there. It's there. They just need to understand the learning curve is not two weeks. It's not a printer. These are, these are things that they have to put in the time they have to really want to do it. I will tell you that of the students that we get and the companies that we get, maybe two out of 10 people are really, sincerely interested. And maybe one out of 25 really wants to learn these machines. Really wants to get into the heart of the machines and learn it more deeply, right? Wow. So I mean, I'd love to talk about this, probably a bit a bit more, but we do need to move on a little bit. So, no, don't worry, you've highlighted such an interesting issue there. I'm gonna have to look into that a bit further.
Jessica Owen
But moving on then in your experience and your knowledge, and you seem to know these machines sort of inside out. Do you have a wish list at all for what for?Connie Huffa
I don't know something that you want to be able to do, but the machines just aren't capable of it yet. Well, I'd say that all the machines doesn't matter which brand they're using technology for the feeder systems and some of the knitting systems that are from the 70s, 80s and 90s. And there are so much more that these machines can do if they would put the work into the feeder systems we run.Into this with creating the fly net, because there was no computer system. We had the first m1 plus ever, and there was nothing in it. We had probably about 400 tickets for machine and computer bugs. So, you know, people are working on it. It's just that what we do is technical textiles. So I would say for 98% of all the machines that are sold, they're sold for apparel. It's probably not a problem for the companies that want to make for Chanel's and Pradas and fendis, they're going to need the same kind of technical upgrades in software as well as hardware as we'd need for smart textiles. We've had to basically build our own feed systems to get wires into the machines. So what we love is to mix the overhead feed like you have on the staggers and the ADF with a four needle bed like you have on the Shima. So your your Shima machine, the X machine. We love that machine. It has tremendous sinkers. We'd love to be able to knit on the top beds, as well as be able to knit on the bottom beds. We'd be able to do so many more things, so much more efficiently, especially in automotive. Automotive, we have pieces that we've made on our four needle bed machine that takes six minutes, same piece on an ADF, they're state of the art. Latest technology takes 48 minutes. So if we were able to improve that, it would make 3d knitting, 40 knitting, and even 5d knitting with interactive materials, so much more cost effective to be able to knit them so quickly. So imagine if you were doing the next generation on automotive seats, where you have to have switches in them, and you need to have more creature comforts, lights, possibly sound. You want to put these things into a seat cover that you can knit. You don't want the thing to take three hours to knit, because then they can just cut and sew it. You needed to be able to take 45 minutes and or less, and that would make it more widely received. So you can imagine, if you wanted to do smart wearable textiles, same thing, we can be able to knit a lot of the harnesses and the wire connectors and sensor ready options right into the garments right now. Shima, you can get one wire into their machine to inlay. They have a floor model that unspools the wire and stole has two. They have a dancer system. You have to put one on either side, or it takes up the entire machine. So it's probably about $25,000 for each dancer. This the one, I believe, is about $10,000 so it becomes really cost prohibitive. So we actually created, and we patented, an unspoiling device. We can get 22 on the machine. We'd like to be able to put them into four needle bed. So we can put a lot of these switches and things, and we can actually put wires in horizontally as well as diagonally and vertically. So that's my wish list. Is if they had the four needle bed machine with the overhead feeds combined, I think that would be the next generation of machine to look for, right? Okay, interesting. It's funny, you say inlay there. I think it was, I'm probably going to get this awfully wrong now, but I think it was last year, stole introduced some inlay system. And I remember queuing up at ITMA in Barcelona to I think they were offering a flag with your face knitted into it, and then they fed in the the little plastic, big bit into what would be essentially how you'd join up the bunting together. I'm not explaining this very well, but that's what they were showing anyway. So that was quite interesting. That is correct, it was actually an insert. And it was a robot piece that actually would insert the the strip of plastic, or whatever you want to put in there, into the edge, so you had a flag and it would have a stiff component. So that stiff component was inserted by a robot. We've We've toyed with vertical inserts. We haven't done the horizontal we've done some vertical inserts. Inlay is actually what makes the fly knit shoe possible. We actually invented a feeder that inlaid the wire to make the zigzag cable into the fly net. So that's all one cable that self adjusts to your foot so that. That was a special feed device that we actually invented. Weren't paid for, but we've actually invented it,
Jessica Owen
right? Wow. So you've mentioned here, like the other possibilities to do, say wearable, smart textiles and so on. Do you think we're going to be seeing a lot?Connie Huffa
More of knitted products such as these in future. Absolutely, I think that the desire for these are out there. Absolutely people want this technology. I think that there are a couple challenges. One is washability. They want to be able to wash the batteries, and they need to figure out what might have to be modular or disconnected, or be able to put it through the washing machine and deal with the agitation and potentially drying. The other challenge that we have is, what do we do at the end of the life cycle? So you'll see, if you look at what Levi's did with Jacquard their jacket. It's a great jacket, regardless of if the electronics work or not. You know what I'm saying? It's a really cool looking jacket. So I think people have to understand whether they're going to keep the product even after something stops working, or how do we recycle these things? How do we get the electronics out of it so that it doesn't end up in the landfill? What? How can we create these products with a lifespan that's going to exceed what our normal 100 washes, and maybe three to six, three months. So right now, in the US, the law is things have to last one selling season. So it's like three months. I mean, I think people would want to keep this a lot longer, rather than things into a landfill that you really can't repurpose or reuse, or in some cases, recycle. Yeah, and I'm very interested in sort of end of life of smart textiles, because I think a lot of companies sort of justify the fact that, oh, it's a new it's a novel garment. People won't throw it away. Or, I don't know, people buy less of them. So does it really matter? When you can compare it to fast fashion and so on. So it interesting to see what companies do in this space. For sure, it's I've seen a lot of people. You're correct. If people consider it novel, they don't want it to be a trend, because they don't want to get in and out of it that quickly. But what we finding is that when people are able to customize things, and they put some of their own ideas into whether it's color or placement or something like that, people tend to keep things far longer, regardless of whether it's a wearable or a regular product, they don't want to part with it. So I think that combination also has some legs, right? Okay, now, before we sort of finish for today, I wanted to obviously bring up this subject of COVID 19, which I mentioned at the beginning.Connie Huffa
So what has been your experience with COVID, 19, with Fab designs, and what have your observations and it's been for the wider knitting industry, I would say that a lot of companies, if they're making masks, they're ticking over, they're maybe paying their employees. But COVID For us, because we work in a field where things need to be touched and felt, and the projects, I mean, dealing with FedEx has been a challenge, but I mean, it's doable. I would say we're down probably about 50% we have been making masks. We made our own masks. We made four different styles, and we made like, four different sizes, all the way up to XL. The challenge is that the CDC, or the government agencies, only give you one size for an adult. So obviously people come in all shapes and sizes. So we've had to grade things and fit test them, and, you know, use real people, real subjects, to go up to a double extra large you can imagine, the government wants the same mask to fit somebody who might be a teenager with somebody who might have a double chin, and it's just not going to work. Their grandmother, it's not going to work. What we actually started doing was we used to do quarterly classes. And people used to come to fab designs in person, and we take them through a three day seminar on the materials, on everything from Polymer to fiber to yarn, manufacturing structures and even working on the machines, just to look and things, see how things are programmed, and that we've started to transition to do some of the what we can teach in online. We've started to create online classes to try and teach people the basics of knitting, of 3d knitting, and things that the machine builders don't teach what we discussed earlier, what what people really want to learn, and they're not finding anywhere.Jessica Owen
And so I mean this pandemic, then, has it held the industry back further from where it was already struggling anyway, when it comes to education and training, I think it has, because we really need to be on in.Connie Huffa
On the machines, in person, even networking at the trade shows pushes our industry forward. It shares ideas. When people are able to share ideas. I mean, I've been to a lot of online trade shows, some of them are have like, their pop up little booths, and information pops up. But a lot of the information you can get from the same vendors on their own website, but actually talking to people and engaging in conversation about the industry. I speak on a lot of different panels, just talking to the other experts. I mean, it cross pollinates so many parts of our industry, from fashion to obviously, composites and people get ideas from each other. And I think you know that sharing is so missed this year, so I think a lot of people are just on pause. Yeah, yeah, completely. I think everyone I've spoken to has said pretty much the same thing.Jessica Owen
Well, Connie, I guess the final question that I wanted to ask you say then is we're nearing the end of this crazy year, and hopefully we can put it behind us. But has fab designs got any interesting projects or plans for 2021, and onwards?Connie Huffa
We actually do. We actually have spent a good portion of this year finalizing a lot of our patents. So be looking for the next generation of shoes from us, also the next generation of composites as well, and as new feed devices to actually get very challenging machines, yarns into the machines. So we have, we have six patents pending right now, so they're close to grant. So I'm very happy. We're very happy about that. We spent a lot of time and money on that, we think it's going to help seller our customers, tremendously. So that's that's next.I would say that a lot of the interesting projects we picked up, we actually are in Southern California, so people that were not able to travel a lot of places include a lot of the movie studios. So we worked on a lot of major movie costumes, so you'll see some really cool stuff coming up in movies next year that we worked on, and some TV shows. So that was, that was some new business that we picked up. We've done some in the past, but because these people are not able to travel, we've got probably about four times the amount of movie costumes.
Jessica Owen
Oh, interesting. It's amazing how well one area of your business might you know completely well be disrupted because of this pandemic, and how other opportunities can arise that's so interesting. Um, well, Connie, I mean, we are sort of running out of time today, but thank you so much for giving up your time and talking to me about fab designs and and the industry, and I feel like I've had my own Knitting Lesson somewhat. So that's been great. Thank you very much for coming on the show.Connie Huffa
Thank you so much for for having us. I really appreciate it, and I want everybody to stay safe, and hopefully we'll all be able to talk in person and share a lot of ideas you.