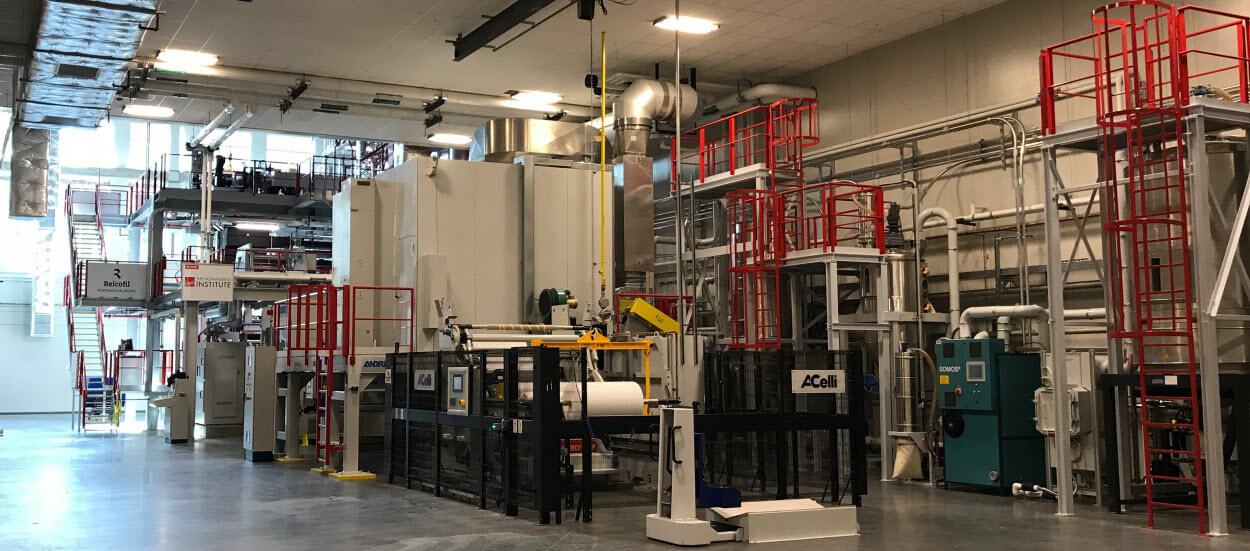
NatureWorks and the Nonwovens Institute have created a new spunbond nonwoven technology enabling the production of at least 10 million additional N95 surgical masks. Jessica Owen finds out more.
As the world faces a critical shortage of personal protective equipment (PPE) for medical workers confronting the Covid-19 crisis, a longstanding partnership between NatureWorks and the Nonwovens Institute (NWI) at North Carolina State University has resulted in a new spunbond nonwoven technology enabling the production of at least 10 million additional N95 surgical masks.
NWI has converted the use of its research and training pilot production line to produce the face mask materials, and NatureWorks has donated the Ingeo resin needed to produce the spunbond material.
“Donating the Ingeo needed for this application was an easy decision,” says Rich Altice, president and CEO of NatureWorks.
“We wanted to support NWI as they create devices that will protect the healthcare workers who will take care of us, our families, our colleagues, and our communities in this crisis.”
Typical N95 respirators and surgical masks are a multilayer structure of one or two spunbond nonwoven layers that provide mask shape and protect the inner filtration layer. Those layers are combined with an electrostatically charged layer of meltblown nonwoven material which serves as the filtration layer capturing microscopic unwanted particles such as viruses and bacteria. The charge is what boosts the meltblown’s filtering capabilities, but it also means that the masks cannot be reused since the charge can be lost during the cleaning process.
“Due to the Covid-19 crisis, we took the spunbond technology and created a new generation of unique filters that have excellent filtering capability without needing to be charged, meaning they can potentially be reused after cleaning with peroxide, or an alcohol solution,” adds Behnam Pourdeyhimi, executive director of NWI.
“Because these materials are also strong, they can be cut and sewn by traditional techniques.”
The fact that the material is potentially reusable is quite an interesting development. Under normal circumstances, the reuse of N95 masks and surgical masks made from meltblown nonwovens is generally discouraged as disinfecting procedures can reduce the efficacy of the electrostatic charge used to achieve maximum filtration efficiency. “However, in this pandemic reuse has become a necessity, making disinfection after each use a requirement for preventing the spread of Covid-19,” adds Robert Green, vice president of Performance Polymers at NatureWorks.
“That’s where this new spunbond nonwovens technology shows promise. Since this fabric does not require an electrostatic charge to achieve high levels of filtration, it is possible to clean them with peroxide and potentially ozone without reducing performance.”
The new nonwoven fabric is a bicomponent fibre made of Ingeo biopolymer (PLA) and polypropylene (PP), providing significant strength and bulk with equal effectiveness in filtration. Additionally, Ingeo improves the productivity of the spunbond process by at least 30%. Leveraging these benefits, NWI’s pilot line can produce enough material to make two million masks per week.
“Ingeo is an advanced biopolymer that we make by using plants to capture and sequester CO2 transforming it into long-chain sugar molecules,” Pourdeyhimi explains.
“We ferment those sugars to make lactic acid – the same chemical produced by our muscles after some hard exercise. This lactic acid is the building block of the portfolio of advanced materials we call Ingeo.”
Today, Ingeo is valued as much for its low carbon footprint as its performance attributes in applications from coffee capsules and tea bags to paper coatings and appliances. In the new spunbond nonwoven structure the use of Ingeo with PP in a bicomponent fibre is what allows for both increased rates of manufacturing and filtration performance. During development, NWI tried other polymer combinations, but found it could achieve the best results with the current structure using Ingeo.
“Typically, one metre of spunbond material provides enough for around 20-25 masks when using the current designs,” adds Pourdeyhimi. “One of NWI’s production lines started producing 2,000 metres of spunbond material per hour, with the potential to create some 20,000 metres of spunbond material in a day.”
NWI currently has an agreement to provide large amounts of spunbond nonwoven material to several key partners, which will make masks at their manufacturing facilities. The organisation plans to provide the new masks to local communities in need.
At the moment, the two organisations are not sure on how long they will be producing the masks for – it all depends on the need for masks brought about by the current pandemic. Although, according to Green, NWI is prepared to manufacture for as long as necessary.
“We don’t expect this to be a one-time run,” he says. “NWI, with the backing of NC State, has ordered two-mask making machines that should arrive shortly, which will allow NWI to manufacture masks from their new spunbond material onsite.
“NWI is known to be the global leader in nonwovens innovation, creating high-tech fibres across applications,” adds Green.
“Their development of this spunbond structure has come to fruition at a critical time when high performance nonwovens are needed to meet the urgent need for PPE by medical professionals during this pandemic.”
NatureWorks and NWI say that the safety of their workers comes first. Both organisations are following recommended guidelines from the CDC for maintaining the health and safety of those who work in their facilities. This includes maintaining appropriate social distances and wearing appropriate PPE while onsite. In addition, NWI’s facilities are GMP certified.
Have your say. Tweet and follow us @WTiNcomment