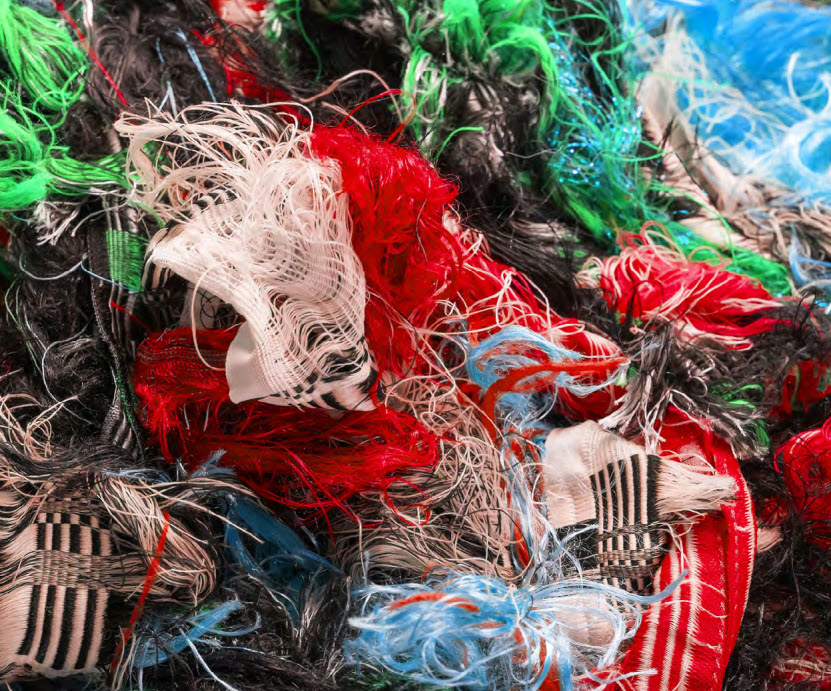
Ep. 66: We aRe SpinDye’s fibre colouring process reduces water by 75%
By Jessica Owen
This week’s guest on The WTiN Podcast is Andreas Andrén, CEO at We aRe SpinDye.
Founded in 2014, We aRe SpinDye has developed a colouring method that focuses on the coloration of the recycled material before it is extruded to fibre and spun into yarn. By melting colour pigments and the recycled polyester mass together, homogenously coloured yarns are created, without the use of water. This method helps to reduce water by 75%, limit chemicals by 90%, and improve energy consumption by 30-40%.
In this episode, Andrén talks about how the process works step-by-step and explains how brands – big or small – can work with the team to integrate this method into their manufacturing process. Elsewhere, he talks about the benefits of switching to spin dyeing, the challenges that companies would have to consider, how the company is exploring other applications in addition to recycled polyester, and how the business is embracing digitalisation.
To find out more about We aRe SpinDye, visit www.spindye.com.
-
Transcript
This transcription has been AI generated and therefore may have some inaccuracies.
Ep. 66: We aRe SpinDye’s fibre colouring process reduces water by 75%
This week’s guest on The WTiN Podcast is Andreas Andrén, CEO at We aRe SpinDye.
Speaker 1: WTiN
Speaker 2: Andreas AndrénSpeaker 1
Hello, my name is Jessica Owen, and I'm the Deputy digital editor at WTiN. And this is the WTiN podcast. Join me and my guests every week as we talk about new and interesting innovations from across the textile and apparel industry. Whether it's talking to sustainable startups quizzing experts on the latest research and development, or chatting to companies about their most recent products, you can rest assured that the WTiN podcast will connect you with everything you need to know. This week I am joined by Andreas Andrén, the CEO at we are spin dye, a company that has developed a more sustainable method for colouring recycled polyester. Andreas mentioned the significant water chemical and energy savings how brands can get on board with the process and how the company is embracing digitalization.Good afternoon, Andreas, thank you so much for joining me today to talk about we are spin dye. How are you?
Speaker 2
I'm good. Thanks. Thank you so much, Jessica, for putting me on. It's gonna be fun. Yeah,Speaker 1
I'm really looking forward to it actually, because I've seen the name we are spin die pop up quite a bit in my Google searches in my news and everything. So it's great to have the chance to wrack your brains about what you do.Speaker 2
Yeah, thanks. Yeah, that's it's fantastic that we got so much attention recently. Well deserved if you asked me.Speaker 1
So shall we start from the beginning then? Because I understand that a man named Martin Burling founded the company a few years back in 2014. So can you tell me a bit more about why he decided to create the company we are spin dye Yes, andSpeaker 2
I also can tell you when I came in, I always tell people that I came in at day two, which is basically almost true company was Su also wrote were founded by Martin Berlin, he's not operational in the company anymore, but he was he was part of the founding group. And the reason for for the concept of weird spin is because we together found out that there was a technology available that have the possibility to reduce the amount of water chemicals, co2 and energy that was conventionally used in dyeing of textiles, but it wasn't applied to fashion and apparel, it was quite widely used in automotive and other industries such as making producing carpets and stuff, but it was not applied at all in the fashion apparel. So myself and also some other people from that founding group we set out to Okay, we are going to have to search for the people that knows the most about this technology, how to make it work, what can we do to make it attractive enough and workable for fashion apparel companies? So that's, that's where it all started. And that's what we were we tried to pinpoint, okay, what's going to be needed for us to make it attractive and applicable for fashion apparel, and the first thing that we had to seek out was the amount of colours and improve the colour development process make it easier more more similar to conventional process of lab dipping. Another thing was as in all the other areas of textile industry, if you want to do something, particularly when it comes to sustainability in everyone who wants to who wants to do something, they also of course, would like to talk about it and if they want to be able to talk about it, they need some form of proof for a certification. Like for example, global recycled standard for for recycled material or GRTs for organic material, for example, but there was nothing even closely resembling this and for this kind of technology or water reducing or resource reducing technology for dying. So we developed our own certificate based on LCA methodology. We did it together with a research independent research organisation called rice here in Sweden, their lifecycle analysis specialists, and we did some cherry picking to make it a little bit more readable. So we we we picked out Four KPIs that we thought was most relevant to textile industry, namely, water consumption, chemical consumption, energy, and co2. So we added those on the certificate, we also added a transparency aspect where we have, where we record all the units that's been that's been involved in production of the, the product. And we provide these on a batch to batch level. So every time you order a batch, you get a certificate as well. And and pairing that with a communication programme with a hang tag. So customers brands can use them in their, in their, in their communication strategies. So, so those were the two sort of main components, and then a lot of other stuff has followed the digital Colour Management and all a lot of stuff that also helps out in the back end, so to speak. But that is, that is really what, what we created it. So we've we've made it possible and attractive and set out. But we say that we created an operating system for Sprint I basically. Yeah,Speaker 1
I mean, I think you just mentioned there those main KPIs. And I think I read on your website, that it's something like 75%, less water 90% less chemicals and 30 40% less energy. I mean, these are really big numbers, aren't they?Speaker 2
Yes, yes, I would say so. I mean, I haven't seen any other solution anywhere across the board that has these reductions. And it's, it's quite clear that there's been numerous reports recently that really points out that the wet proxy read processing or dying is the most resource intensive process step in the whole Textile Supply Chain, even the in a lifecycle analysis. So So yeah, and like you said, it's 75 in average, though, so 75%, less water used 90% less chemicals, 30%, less co2 and 30%. Less energy. So that's, that's ridiculous numbers, what you can do it just by just by just by changing one one little thing.Speaker 1
And I mean, you said earlier that it was a technology that was already available, but just not used in fashion. And I'm just so surprised that I mean, I don't know when that technology first came out, but how it's taken so long for someone like yourselves and the team to actually think, no, this could be used to make quite a big difference in somewhere else.Speaker 2
Yeah. I mean, of course, I can only speculate, but it's looking at it from a perspective of sustainability. It's it's not that long ago, where, since it was not really an issue, if whether you used a lot of water or chemicals or energy. It wasn't no one really cared. Look, looking back 2015 20 years ago, I mean, there was there was there wasn't an issue with that. So there was just no reason I think to dig into it, the reason why it was first applied in the automotive industry was because it had so a lot higher colorfastness performance. So that was that was the main reason why they why they started over in automotive, and then they realised it would have also had a positive sustainability impact. SoSpeaker 1
I mean, should we talk about the technology then in actually how it works? So, I mean, where does it all begin? What's the very first step? Okay,Speaker 2
so, we're gonna start talking about I think it's first quite important to understand how the arts done conventionally. So conventional dyeing works, that you start off with a polyester fibre. So the polyester yarn is produced using raw white chips, and then it's extruded into, through a spinner, it becomes a yarn, it's now it's raw white yarn, then it's texturized. It's made into a fabric by knitting or weaving. And then when it's done, weaving or knitted, it's, it's ready for dyeing. And then it's been it's sent to a dye house and died in the correct colour and it's in this dyeing stage where all these resources are needed. Very high temperatures, it's a very tough and long cycle of process, high temperature and high pressure, chemical salts are used. So, in in SPIN nine, what you do is we go back to the first step where you actually are creating the shape of the yarn so it's in the melt spinning process. So in the melt spinning process, As there we add something called a masterbatch, which is basically a compound of pigments and sometimes also dyes, but mainly pigments added to the spinning solution, before it is extruded through the spinneret. So, when it comes out as a yarn that needs to also already have a defined colour. So, the process step of, of dyeing wet processing is completely obsolete.Speaker 1
Gosh, right. And so, have you developed a new technology any new equipment? Or is it something that's actually very easy to implement into the existing manufacturing process, if you're just adding it to that first stepSpeaker 2
is fairly uncomplicated to onboard? What we do we tap into existing sort of additive modules. So we're adding colour in the melt spinning process. So there is a there's a lot of spinner spinning facilities out there in Germany, Turkey and China. Most of them have part of their spinning lines are equipped with an additive module. So as long as it is equipped with an additive module, then you could actually produce our products.Speaker 1
And I imagine that it's actually quite important that it's that easy, because people don't have an excuse, then if they've got this extra module not to do it. No.Speaker 2
And of course, I mean, since it is, you're adding colour in a different part of the process. So that means one of one of the changes in your process means that you as a brand would have to make your colour decision usually slightly earlier than you're used to. So that is a that is, if you'd say one of one of the hurdles. But we have found a lot of good ways to either get around that, or by using products that are very stable when it comes to colour. I mean, everybody that works in this industry knows that black is a very safe colour usually sells 70% of all garments being sold are black, so and then using colours that are recurring. Also working with products and production lines that have a decent volume, it doesn't it doesn't work particularly well. If they if you expect to sell or produce a very small volume, then it's a little bit a little bit inflexible.Speaker 1
Okay, and are you limited at all by colours? Or is there actually quite a vast range to choose from?Speaker 2
Yeah, no, there's no no real limitation, I would say all substrates have limitations. If it's we talked about cocktail, we talked about polyamide all substitutes have have limitations somewhere in the ColourSpace when it comes to depending on what requirements you have in terms of colorfastness or cost or anything. So, so, also spin dying has some some limitations, some in some places in the colour space. But we have done we developed several 100 colours that exists, we have simulated more than 1950 colours, based on the NCS system. So which we know that we can produce if if we need to. But we did, but there's also there's also a lot more colours in between colours that, that we also know that we that we can produce. So, so a lot of colours, but yes, as as all substrates and all technologies have their small, small limitations. Yes.Speaker 1
Right. Okay. That's interesting then. And you said that as long as a manufacturer has this extra module, and you're actually eliminating the wet dyeing process completely, can I assume that is slightly cheaper to practice colour garments in this way? Or is it actually more expensive at all?Speaker 2
I would say looking at it today. It is slightly more expensive, I would say slightly more. But that I think that also has to do with that. A lot of the fabric mills that are working on the technology are also picking up date. They don't they have they don't have a structure for quoting prices without wet processing. So there's always there's always some little extra added cost that sneaks itself in there. So we always encourage our customers to really be careful when they because if we delay Over yarn into a nominated fabric belt, for example, to make sure that they get an open costing, so that they can see that, okay, the decoded price is actually without any wet processing to reduce the price, but looking at it in general terms, yes, it, it becomes slightly more expensive, I would say maybe a premium of 10 15%. But it's it's very quickly gets competitive if you can increase the volume. And we're seeing that as this technology is increasing in volume and taking, taking space. And looking at what's going on, when, when it comes to managing water, especially in places where they have scarcity. It's just a matter of time before regulations are are tightening even more, they've been tightening every year for for several years now, both when it comes to polluting, but also when it comes to water use. So we do see that in just a matter of time, we would probably be on par with conventional dining. ISpeaker 1
think that's the case with a lot of the sort of sustainable alternatives that right now they're probably more expensive, because they're just not, you know, on the same scale as all these other technologies. But yeah, I think as you say, one day when it becomes more mainstream, all these prices are gonna come down in terms of economies of scale and everything. So we just need more people to get on board with it. And then, you know, make that change that a lot sooner.Speaker 2
Yeah, and I mean, they're all the all the manufacturing countries that are heavy on textile looking at Bangladesh, China, they have severe water scarcity issues. And there's just not enough fresh water and all textile, you when it comes to dyeing and processing, you need very keen water, otherwise, you will contaminate your products. And since this is a solution that really takes away that step i There's no, there's no logic to why it isn't more widely used.Speaker 1
And so can I just clarify then, is this a technology that you'd licence to people? Is that how it works?Speaker 2
No, we, we could do that too. But what we normally do is we're involved in the process, both in terms of developing a project. So we work together with the brand to find, find the first most suitable project, and then we call it we helped in colour develop. Sometimes we work with their nominated spinners, we sell the ER, we produce the yarn together with their spinner and then we sell the yarn to their nominated fabric mill. But we can also in terms if we there's a let's say there's a smaller customer that doesn't have a very tight control of your supply chain. Maybe they're not dominating all all their tears, in that in those cases, we have a tailored supply chain where we can actually also supply yarn. So we can work we can work depending on the situation, depending on how the customer the brand normally works. We could either licence and certify, we could deliver yarn or we can deliver fabrics. Well,Speaker 1
I think that flexibility is really important actually. Because, I mean, I know you've worked with h&m and they're a huge company, and they've got all these capabilities, but maybe there's like a boutique startup company that would love to adopt your technology, but you know, it's maybe a bit harder for them. So that's so important.Speaker 2
Yeah. So, we make that possible we make it possible to nowSpeaker 1
at the moment I understand that you work with recycled polyester, but could in theory the technology be used for other fibres one day,Speaker 2
yes. Today focuses on recycled polyester. And the reason for that is because when we set out we we aim for the raw material that was the of course the largest portion. So I think it's about 65% 60 65% of all textile being made is polyester and the recycled part of that is just continuously growing. It does work the technology does work on polyamide it works at least similarly on viscose and those type of fibre products. But then the setup would have to be completely but the the the logic works the same way where you add colour in in sort of the in the spinning process. But in technic The detail, the process itself is, is completely different. And you use different kinds of dyes and compounds. But the logic would would would work the same way. And yes, we're, we're definitely looking at applying our way of structuring it into several different raw materials, raw materials as well.Speaker 1
Well, that's interesting to hear. Because I mean, from my perspective, it sounds like there's such a great potential here that it'd be amazing if you could just apply it to all sorts of fibres. But I am an optimist when it comes to these things. So. So you've already mentioned colorfastness, is something that has not been compromised at all, with this new method. But I mean, how is it performance in other areas? I mean, are there finishing opportunities? I mean, can it be treated the same as other fabrics? For example?Speaker 2
Yes, we we haven't found any other let's say post finish or anything? That was not. That was not compatible? We haven't seen that. Like, yeah, you mentioned the upside of being more colorfast. Also, there is no same thing. I guess it goes hand in hand with the colour fastness, but migration doesn't it's not a problem, either. Colour migration. I think also colour constancy when it comes to batch to batch is also higher than conventional diet products. So in terms of that, no, there's no there's no downside.Speaker 1
Well, I mean, it sounds like such a great alternative to dying that and so I mean, do you ever think that you'll be able to put traditional dying out of business one day?Speaker 2
I hope so. But I know I don't know. I think it there are there are probably applications and situations where you where you would need conventional peace dying. Hopefully there, there's more being done in terms of water reduction and resource, resource saving, technical, like machinery and whatever they whatever they're working on. But but when it comes to synthetic materials and materials that are being a man made spun, man and being made similar to polyester and viscose, there is a there's no alternative that code can compete in terms of resource need than this method. Well, ISpeaker 1
mean, it's interesting you say that, because I think the only thing that is sort of come close that I've seen recently is I think it was Ralph Lauren has just launched something called colour on demand. But I think that's more to do with cotton, not synthetics. But yeah, I mean, as you say, I don't think I've seen anything quite like what you're doing anyway. And I mean, you're already working with some great brands. So you're definitely on the way to sort of putting those other people out of business. So I mean, are you able to sort of tell me a bit about the work you've done? I mean, I think listening some here, there's like Quicksilver Birkins. And Norway, h&m, as we've already mentioned. So, I mean, if we take h&m as an example, you're able to tell me about the collections that you've done with them so far?Speaker 2
Yes, I can mention just briefly so we've done first launch was in December with their waste collection, where we had a where we where we delivered some parts of the recycled polyester, which was dyed using various panel technology. We also had product launched with our kit, which is the latest I think, the latest addition to h&m group. There was a a running pant. Unfortunately, I can't tell you much more What if if or when it could be anything in the pipeline. But then also, we had a very nice trench coat with h&m women's wear just launched a few weeks ago. And then recently, which I am very proud that we took part in is the innovation stories colour story. So that is also I think it's a part of the conscious exclusive line or edge e&m where focus was particularly on colour and different dyeing methods. So, sorry, it was a it was great that we could take part in that and hopefully that puts a spotlight on different timing technologies and which one is the most sustainable? Yeah, that was fun. Yeah,Speaker 1
I actually saw the I think it was a press release for that. And they had some of the images of I think there's a skirt or a tarp. And it's sort of a lovely yellow we and there's some blue and pinks in there as well. And it does highlight that colour, you know that you're not compromising at all? I mean, who would know the difference when you look at something like that? Yeah, exactly. And I mean, these other companies I've mentioned like Bergans of Norway. I can never pronounce St. But for Hallo Raven, the the rucksacks it clearly, there's quite a few different applications here. I mean, you've got accessories outdoor wear, so it can just be used as any other synthetic for any other application.Speaker 2
Yes, there's, there's really no, no real limitations, as long as you're willing to look at what you have. And maybe, because we touched on that in earlier on, it's a lot more sort of smart, if you reduce the amount of different yarns that are used in a particular fabrics, because then you can consolidate production, maybe you can use that same yarn. If you're making a backpack, you can make it you can you can do an accessory, you can make something completely different, but using the same yarn and you will have the same colour. Usually you have similar colours in a lot of products in your range. So by being able to consolidate, you could do a lot of interesting things. But yes, no, not really any of not really any limitations we've done. you line them up yourself. We do outerwear, well, jackets, we've done accessories bags, we're doing. We're doing light ball winds, we're doing knit, it's knitted stuff, we're doing golf and stuff like heavy. It's just a matter of creativity. Right.Speaker 1
That's so interesting. And I mean, have you got many more brands sort of lining up at the door trying to test out this technology with you?Speaker 2
Yeah, I mean, we can't really tell you too much. We're, we're we're listed companies since December. So unfortunately, there's not much I can say. But yes, we do. We do get contacted. On a regular basis. We have got, like you mentioned as well. Got a lot of attention recently. Especially, you know, h&m is a big name draws attention to it. So, yes, we do get, we do get a lot of attention. WasSpeaker 1
it was it super dry? That was the latest brand that you announced that you're working with? Is that right? Exactly? Yeah,Speaker 2
that's right. So that's that's announced? What we're doing is a secret. But we have we have we have taken the necessary steps to go into collaboration.Speaker 1
Now. I mean, these are some big names that you're working with. So I'm assuming that scale isn't an issue with you. Can you grow as the demand grows?Speaker 2
Yes. Yeah, definitely. We're well prepared.Speaker 1
Now, I've only got a few more questions as we are sort of running out of time. But I mean, in terms of logistics, I mean, what are the main concerns that brands have about adopting this new colour dyeing methods? And how do you sort of assure them? I mean, what are the main barriers that they think there? But actually, I mean, how easy is it for them to just get on board with you guys?Speaker 2
Oh, I'd say I touched on one little bit before that, I'd say colour decision needs to be made slightly earlier than there than there used to, at some, sometimes at least, it depends a little bit on what kind of company it is, if it's more of a fast driven company, where they usually try to push the colour decision as late in the process as possible. Or if it is a more of a conventional process where you do salesman samples, and you go out and you go to retailers and taking orders. In that sense, it's it's still not too far away from the conventional process, but when it comes to more fast driven companies, then of course you need to you need to be confident that what you are ordering you need to have confidence in us as a supplier. But also looking at finding the right entry point finding the right programme that is mostly suitable but and then it usually snowballs from there. Once you have started and you've you have a you have a colour that is continuously running, you have a yarn specification that is continuously running that you're happy with. And then you just continue and building from there. You use that yarn specification, you make a new sample, you start to build your, your collections from the ground up. It's it's much more efficient. You can consolidate yarns, you can consolidate colours. It is it's Just a matter of looking at it from a slightly different perspective, from from, from our point of view, this is how it should be done. Of course, that's not always how it is done. There's a lot of people that have their own ideas. And of course, you know, there's a lot there's a lot of people, when from start to finish building a collection or or creating a product in fashion, where there's so many people that has a say in it. There's a designer, there's a product developer, or there's the buyer. So everybody wants to say, but it usually works quite well. If if customers are listening enough to us. Yeah,Speaker 1
definitely. Well, finally, then Andrei, is I mean, you've touched on these brands that you're working with, and you're even potentially considering other sort of fibres and so on. But I mean, what does the rest of the year hold for we are spin die, what are the next step for you guys? NumberSpeaker 2
next step is we're continuously working on on on digitising. So this company was formed not only on the aspect of bringing this technology to the fashion apparel industry, but also that it should be tailored for digitalization. So we're our, our mission is to reduce the amount of samples being sent, we are trying to we're trying to move away from physical samples all in all, so we're trying to move away from visual assessment when it comes to colour, just relying on spectral data and sending that back and forth. So so that is a does a big thing for us. We're working with a few very good partners into moving the needle in that way. A lot of I think, in general, American companies has become a lot further on moving at least column management to digital space more than than European customers. So there's a lot of customer, European customers that are still very much attached to visual assessment.Speaker 1
I say, I mean, do you think COVID-19 is going to maybe change that mindset at all in Europe? I mean, we're all having to be more digital these days and sort of take advantage of those sorts of tools. So do you think that will sort of change soon?Speaker 2
I think it has, it has giving it some, you know, some added added force? Yeah, definitely. But it is it is a it's a character kind of conservative industry, though. So there's small changes, takes takes time. But yeah, definitely, it's going in the right direction. We're also seeing what we're trying, we're aiming to be fully implemented into, let's say, you know, 3d design software such as Cloud 3d and the likes of those to be able to select and use, we're spinning yarns and colours, fabrics directly into them. So that's also something that we that we see is going to be really important in the future.Speaker 1
So I mean, you're not only sort of changing the way, colours and dyeing works, you're sort of building this whole sort of different textile ecosystem by the sounds of it,Speaker 2
and not really building it by ourselves. But we're tapping into the, I'd say the leaders of change that they're the ones that are trying to change it all the software developers that are trying to build tools for moving the textile industry to digital space. We're we're working together with them and we're trying to tap in and we're building modules so that we would be suitable for that industry when it when the time is right.Speaker 1
Well, I mean, it sounds like you're doing some really brilliant work. And I mean, as I said, I think we've not got enough time to talk about anything else. But I mean, good luck with everything and I can't wait to see what this new super dry collection is. What if you'll be doing any more with h&m? I mean, we've got to keep an eye on you guys, for sure.Speaker 2
Thank you so much.
Have your say. Tweet and follow us @WTiNcomment