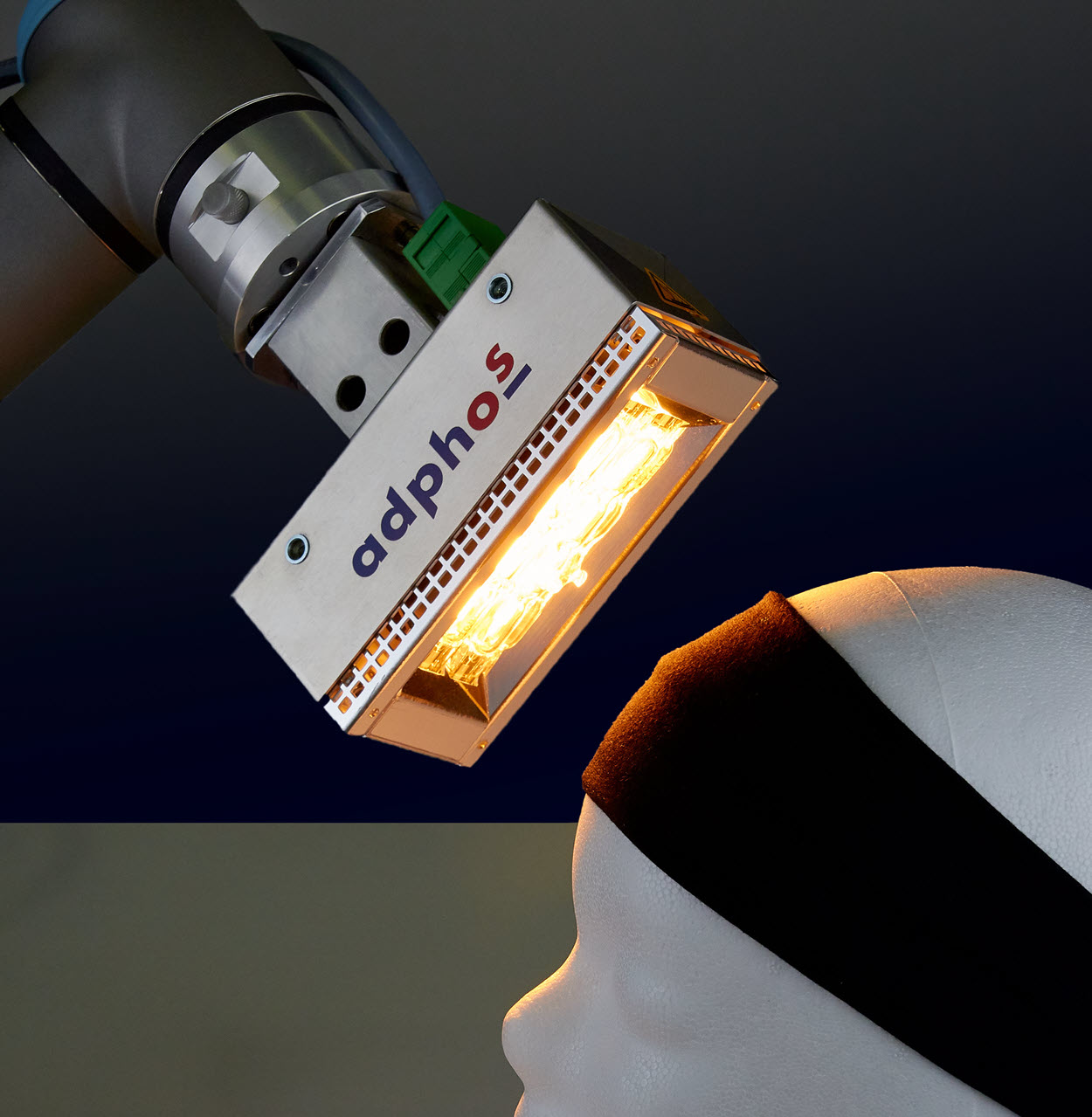
Many critics argue the textile & apparel industry has neglected its environmental responsibility for too long. And because of marketing ploys to suggest otherwise, the term ‘greenwashing’ has become mainstream leading commentators to call for change, which includes a greater degree of transparency.
But despite cynicism in certain quarters, there is hope that the textile finishing industry is turning a corner. Some original equipment manufacturers (OEMs) have combined innovation with the need for change and thus more sustainable solutions have entered the market. Meanwhile, consumer awareness is impacting buying habits, particularly among younger generations, which would ultimately hit the pockets of brands and manufacturers – this trend is considered likely to instigate change.
One company boasting innovative technology is Germany-based adphos with its advancedNearInfraRed (aNIR) platform, which the company says marks a milestone in improving the efficiency of energy intensive thermal processes in the textile industry – the company’s technology also applies to the metallurgy, plastic-forming, printing, and coating industries.
During the last quarter of a century, adphos has garnered a reputation for drying and curing machinery, but has only recently focused its attention on the textiles market – the second most pollutive industry to petrochemicals.
“The industry standard when it comes to drying and curing textiles is to burn gas to heat the warm air dryer, in which there is a ventilation system to extract the steam that is produced,” says Frank de Jonge, sales director, adphos Group. “If you applied 100g-150g of liquid to one sqm of fabric and a company wanted to dry this, they would need to bring it to a warm air tunnel where the process eventually evaporates the moisture and dries out the fabric.”
adphos’ signature solution operates differently to reach the same outcome, however, and has been key to the company’s growth through the decades, explains de Jonge. “With aNIR, a sophisticated flow of warm air is combined with the specific characteristics of the powerful irradiation in the NearInfraRed wavelength spectrum, achieving a high-energy density up to 1.5 megawatts (MW) per sqm.”
The polar molecules of water react significantly faster to this kind of irradiation. “In other words, the water from the fluid evaporates at the speed of light, says de Jonge, while the un-polar fabric stays more or less cool.”
WHY INVEST IN CHANGE?
The advantages of adphos aNIR-technology for the textile industry have been validated in printed electronics projects for “electroluminescent wall decoration in a coating and printing process,” de Jonge says. The company’s aNIR technology is already being utilised by leading manufacturers across the textile industry, including companies at the forefront of the digital textile printing market that operate direct-to-garment (DTG) and roll-to-roll solutions.
adphos developed a dryer for an inkjet single-pass-printer following ITMA 2019 in Barcelona. The footprint of the adphos drying module is more than 80% smaller than a comparable warm-air-dryer heated by fossil fuels and up to 70% shorter than standard InfraRed dryers. In single-pass printing, the dryer and the printer are together which is why the machines appear to consume more floor space, but on the flip side there is less need for auxiliary equipment elsewhere on the production floor.
Nevertheless, de Jonge continues: “adphos’ aNIR technology can evaporate a water-based primer with 250 gsm wet application from cotton within seconds while maintaining a fabric temperature below 100°C.”
adphos can detail a whole host of features that support the argument to invest in aNIR technology. The simpler the solution is to implement and operate, the more appealing it is to the user, and improving uptime by enhancing a machine’s reliability and eliminating warm-up and stand-by times is a key factor in the purchasing decisions of countless textile manufacturers.
According to adphos, the benefits of implementing aNIR-technology include: significantly reduced energy consumption due to high evaporation rates; supported mass transport by the adphos WAVe-concept (Warm Air Ventilation); zero CO2 emissions courtesy of the electro thermal process; a compact design [two-metre long dryer for a 60 metre per minute line speed]; adjustable power according to the colourant-chemistry, its absorption characteristics and the fluid mass applied; an adjustable drying width; the possibility for vertical or horizontal positioning; and no energy waste during standby or start-up.
The company’s aNIR-drying systems are available as boosters to integrate into existing installations to speed up current processes, or as stand-alone drying and curing solutions. “[Our] aNIR concepts are fully adaptable to the performance requirements of the individual application,” says de Jonge. “Often booster solutions are paid for with productivity increases within a matter of months as productivity of existing equipment can be increased remarkably with a comparably low investment.”
SUSTAINABLE EXPENSE
The issue of sustainability, which has arguably lost its meaning in the decades since the term was first coined, has remained a prevalent issue throughout the pandemic and the economic turmoil that ensued.
If we focus on the good news, investments in research and development (R&D) have resulted in the emergence of a growing variety of environmentally conscious technologies for textile manufacturing that are either less energy intensive, consume fewer hazardous chemicals or produce less wastewater.
But these technologies are in their infancy, demand for them is still low, and as a result they are charged at a premium. And even operating the machines following initial investment can be a burden on finances compared to more traditional solutions.
Many businesses acknowledge that the environment poses a serious challenge to the textile industry. But the cost of environmentally friendly practices is delaying change despite the introduction of more stringent regulations in certain economies, particularly Europe.
De Jonge explains there are several ways to assess pricing, but it is also good to focus on the industry’s overriding ambition.
"If we say our efficiency is around five times better than gas [kilowatt vs kilowatt], and gas is US$0.03 and electricity is US$0.15, you're on par,” he says. “So there is proof that our [adphos aNIR] technology is much more efficient, but because of the low price of gas compared to electricity it [aNIR] is not attractive yet.
"It is true that investment in an adphos dryer is higher than in a gas dryer, but the CO2 discussion makes gas more expensive. We have CO2 certificates in many countries – in the UK the charge is £25 per tonne of CO2 generated and the prices are likely to rise. At the moment, Switzerland and Sweden are at the forefront; they are already charging more than EUR€100 per tonne of CO2 generated, which customers have to pay when they buy their fuel. So this benefits adphos’ drying technology and this is why we believe in our proposal for the textile industry. But there is an ethical and moral element to this, too, rather than simple cost savings.“
Have your say. Tweet and follow us @WTiNcomment