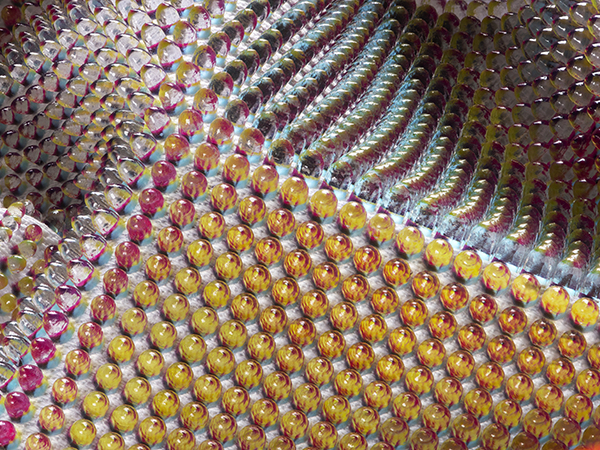
Sustainability requires new manufacturing methods, while fashion seeks advanced functional and aesthetic garments. Enter 3D printing technology – an additive manufacturing process that meets these evolving needs. Otis Robinson reports.
The automotive and aerospace industries are often, arguably, leagues ahead of other sectors regarding Industry 4.0. Their adoption of advanced manufacturing tools remains steadfast, and now other traditional industries – such as the textile & apparel industry – are lagging behind them. Academics argue the implementation of Industry 4.0 tools is not only favourable for soon-to-be-outdated industries but a necessity. Consequently, digitalisation is inevitable, particularly as sustainability efforts demand new manufacturing methods to oppose mass production.
The textile & apparel industry is thus fast digitalising (aside a few stubborn accessibility and adoption hurdles) but remains largely out of touch with an increasingly popular technology: 3D printing. A notable alternative to traditional manufacture, 3D printing (or additive manufacturing) stands poised as an attractive digital tool to provide solutions to the textile & apparel industry.
“We have lots of customers in automotive and aerospace,” says Dave Hayden, application engineer manager at Stratasys. The company, a manufacturer of 3D printers and 3D production systems, supports rapid prototyping and direct digital manufacturing solutions for a variety of industries from aerospace and automotive to medical and electronic sectors. The company stands alongside a growing number of 3D printing technology providers – the market size is expected to grow from US$17.4bn in 2022 to US$37.2bn in 2026, according to Statista – and is now tapping into the needs of the textile & apparel industry.
Parts manufacture
A notable application area for 3D printing is the manufacture of tooling and parts. Hayden says: “[Our automotive and aerospace customers] have production machinery that must run. Any minute that the production line is down is a big dollar loss.”
These production bottlenecks are just as unattractive in the textile & apparel industry. Therefore, Hayden notes the industry could utilise 3D printing similarly to automotive and aerospace manufacturers. He says: “If a fabric cutting machine fails – some bracket that holds a sensor [breaks] – then an [additive manufacturing system] can print that spare bracket overnight. The next day, the system is back up and running, rather than having to wait two weeks for a spare part.”
But Hayden suggests the use of 3D printing technologies for parts manufacture is not incredibly common in the industry. Rather, the textile & apparel industry shows eagerness to wield 3D printing technology for product manufacture. From design to runway, many creatives have tapped into the aesthetic and functional capabilities 3D printing can bring to a garment.
Evolution
Thus far, four generations of 3D printing exist that track the technology’s relationship with textile & apparel product manufacture, says Hayden.
Generation one enabled advanced prototyping. It saw fabric mills 3D print tools to help cut fabrics faster or more accurately. Alternatively, the printer could produce prototypes of buttons, zippers or other garment accessories.
Generation two was characterised by more creative tooling – “brands might print their logo with an additive manufacturing system and use this as a tool to emboss the logo onto leather or fabrics,” notes Hayden.
The third generation allowed customers to customise garment accessories like buttons. For example, in 2014, Florenradica, a manufacturer and provider of accessories to the fashion industry, adopted Stratasys’ J Series model 3D printing technologies to produce prototypes of customers’ fashion ideas. The technology proved such a success that it is now the sole technology deployed in-house for design and manufacturing, a Stratasys case study notes.
Hayden explains: “They’re printing buttons in full-colour to be sewn onto garments. Customers can specify what they want – actually personalise their clothing with their own designs and colours – print that onto a button and sew that onto something.”
And lastly, generation four – which Hayden describes as an incredibly cutting-edge application area –involves direct-to-textile 3D printing and the 3D printing of whole textiles from scratch.
On direct-to-textile printing applications, Hayden asks: “What if we start to [3D] print on fabrics with materials that can change the stiffness in a certain area? Or what if we [3D] print onto fabrics with materials that react to moisture, and therefore open and close pores to give that fabric a property it did not previously have?”
This is the ‘lower-hanging fruit’ of 3D printing applications for textiles, says Hayden, in that it is much easier to implement.
Stratasys has thus far explored aesthetic purposes for direct-to-textile 3D printing. In 2020, it worked closely with fashion designers Julia Koerner and Ganit Goldstein as part of Re-FREAM, a collaborative research project funded by the EU to co-explore the use of 3D printing in the future of fashion. Among other fashion-based projects, the so-called aesthetic freedom of 3D printing has attracted significant interest from high-end, luxury markets.
In parallel, 3D printed elements have been used to add functionality to footwear: Spain-based designer Silvia Fadó creates hydraulic heels that constitute a cushioning effect, for example.
Printing textiles
When idealising the potential of 3D printing, most turn to the additive manufacture of whole textiles.
In 2022, Stratasys 3D-printed the Mega-Textile PA11, a 3.5 m long mesh material formed from thousands of individual links. The team utilised its H350 3D printer with selective absorption fusion (SAF) technology and produced the textile using high yield PA11 powder, a bio-sourced material extracted from castor oil.
Prior to printing, a textile comprising chain links was modelled in a computer-aided design (CAD) programme. During the process, a series of inkjet heads jetted fluid, layer-by-layer, onto extremely fine PA11 powder. The fluid allowed heat to be directed to specific areas, selectively melting and fusing together grains of powder into a monogenous part. Hayden explains that once the printer completed the process and had cooled down, a block of powder remained with the textile ‘coiled up inside.’
He says: “You could then take the textile out, clean the loose powder away that hasn’t been fused together, and you’re left with individual links in one continuous piece.”
Alternative manufacturing
The demonstration highlights the potential for 3D printing to create textiles from scratch – perhaps on-demand, an alternative to mass manufacture which leads to environmentally detrimental waste product. But Hayden notes that it is not a priority: brands and manufacturers will likely grasp at those aforementioned lower-hanging fruits for the time being.
Hayden muses that this is because direct-to-textile applications present a more attractive and immediate use case in the industry. In September 2021, D-house, an R&D laboratory for new fashion technology applications, leveraged Stratasys’ direct-to-textile 3D printing technology for a collection developed with non-profit The Woolmark Company. The collaboration saw ‘unique patterns’ 3D printed directly onto Merino wool knitwear using PolyJet J850 3DFashion technology.
A press release noted: “The team at D-house is also exploring entirely new production methods for high fashion garments, bags and shoes, including the combination of direct-to-textile 3D printing with other processes such as thermoforming, as well as the use of the technology to repair vintage garments to further increase sustainability within the industry.”
Alternatively, the 3D printing of whole textiles has seemingly no industrialised use cases and is slower and perhaps too far a jump from contemporary market requirements in the garment sector. For example, batch size one production – a completely different model to traditional manufacturing – puts mass production off the table, which is currently the standard for fashion and apparel industries.
Hayden says: “This technology is good at producing batch size one. This is possibly not for commodity markets – [in the textile & apparel industry] when you’re looking at millions of garments in a single production line, single size, single type, that’s commodity market. [3D printing] can’t produce parts in the millions – but it can produce parts in the thousands and tens of thousands. Ultimately, [this type of application area] is very much aimed at the luxury market.”
Hayden concludes that although the demonstration is a great feat, the industry at large is not quite ready yet: “[The Mega-Textile PA11] is a nice demonstration of the capabilities of the H350 3D printer – but does it mean that the [printer] is a machine designed for printing textiles? Probably not. […] I think that’s probably not the way that the industry will go – [we won’t just] print finished fabrics from only 3D printed materials – but I think we are going to see a more hybrid approach where we combine additive manufacturing with traditional technologies.”
For more information, visit www.stratasys.com.
Have your say. Tweet and follow us @WTiNcomment