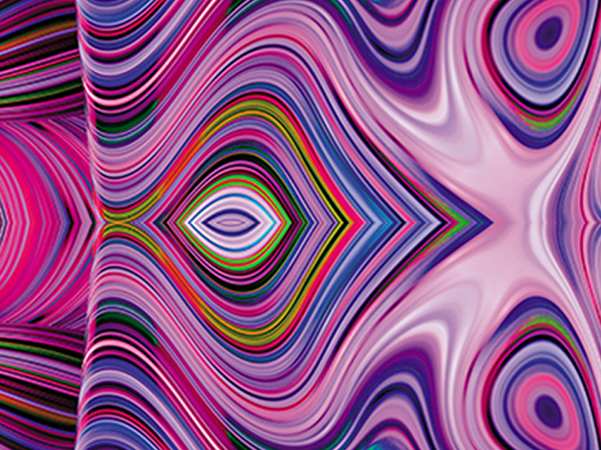
Ep. 84: Hybrid colouration solution is versatile and saves resources
By Jessica Owen
In this episode of The WTiN Podcast, we talk to Jeffrey Hsu, chief innovation and marketing officer, and Peter Decorte, chief operations officer at NTX.
NTX is a textile innovation and solution company that has developed a hybrid textile colouration system called NTX Cooltrans. Indeed, the pair say it is a mix of digital printing, sublimation and wet dye techniques – something they claim is completely new and unique.
In this podcast, Hsu and Decorte explain how the NTX Cooltrans technology came about, how the different machines have evolved, and what the environmental benefits are of adopting the system. They also talk about production benefits regarding the ability to print on both sides of the fabric and how the fewer process steps results in an end product that retains its strength and quality. Lastly, the pair explain the company’s plan to roll out the technology through joint ventures and how companies can get their hands on NTX Cooltrans.
-
Transcript
This transcription has been AI generated and therefore may have some inaccuracies.
Ep. 84: Hybrid colouration solution is versatile and saves resources
In this episode of The WTiN Podcast, we talk to Jeffrey Hsu, chief innovation and marketing officer, and Peter Decorte, chief operations officer at NTX.
WTiN
Hello, my name is Jessica Owen, and I'm part of the team here at WTiN. And this is the WTiN podcast.Join me, my colleagues and our guests every month, as we talk about new and interesting innovations from across the textile and apparel industry. Whether it's talking to sustainable startups quizzing experts on the latest research and development, or chatting to companies about their most recent products, you can rest assured that the WTI M podcast will connect you with everything you need to know.
In this episode, we talk to Jeffrey Hsu, and Peter Decorte. From NTX Call trans. The pair talk about the company's hybrid textile coloration system, the benefits and applications associated with it, and the team's plan to scale and continually improve the system through joint ventures.
Good afternoon, Jeff and Peter, thank you very much for joining me today. Are you both Well, yes, thank you. Very Yes. Good. So where exactly you tuning in from? So Peter here? I'm tuning in from Bangkok, Thailand, sitting in a beautiful restaurant by the river. So actually not a bad spot for today. Yeah, lovely. Lovely. And what about you, Jeff? Yeah, I was very jealous of where Peter is. I'm in Taipei, Taiwan. I'm sitting in the dog kennel because the family is trying to sleep now. So get myself away from everything else. I see. Okay. Oh, well, thank you both for staying up to talk with me. Anyway, I appreciate there's a time difference. But yeah, you guys have a very intriguing innovation that I think our listeners would love to learn about today. And so that innovation is something called NTX cool trans. Now, I'll let you to explain more about it in a moment. But essentially, to everyone listening. This is sort of a new sort of technology. And the company claims that it's sort of changing the landscape of the dyeing industry. So I wouldn't usually start asking you guys about the product itself. But I understand that what you've developed, there's quite a nice backstory, and I think it would make the product itself. I think people could understand it better if we if we hear about that first. So yes, if one of you could tell me about why you developed into X cool trans and your sort of journey to where you are today. I think that'd be great.
NTX
Yeah, sure. Let me let me run with that one, kind of a bit of the backstory. So I sometimes joke a bit that the intellects culture is started as kind of a love story. And it's not that far from the truth, which is our founders, Mr. Calvin, Joan and Sandra, Joe. Initially, they looked at the landscape of textiles, this was way back in the 90s. And they were looking at means of improving upon sublimation technology to create very high quality prints. Sublimation as we know, it doesn't really work on any other material, except for polyesters, or very, very, very low elastomeric blends of polyesters.But beyond that, it's quite limited. So they were looking at all right, it is a waterless technology, there's a degree of factory precision and efficiency associated with just being able to look at a design look at a colour and just print it in the same way that the paper industry already prints for, for the newspapers or magazine articles.
And so they wanted to say, Can we utilise the same concept here and paint print on on fabrics? And so they set out on a journey to explore what the limitations and what how far can we actually push sublimation technology?
I think it was probably about two years in, they realised that without a fundamental change to the base chemistry and the base process to which you actually look at putting colour onto textiles, there was no way that they could improve upon sublimation beyond where it already is. So back to the drawing board, right.
And that's where they started looking at the EEG chemistries, the various different types of equipment, and that's where they settled into an area in Shanghai that had occurred critical mass have both the talent, the workshops, the chemical expertise or the chemical engineering expertise in and in the relatively short radii from from anywhere.
And that began the whole process of looking at different types of application pick methodologies, different types of ways to bind, or introduce colour into textiles. And so whereas with paper, it's quite simple relatively to do that, since there's only four primary different types of paper in the world.
But with fabrics or textile fabrics, you got wovens, you got nonwovens, you got knits, you have polyester, various different types of synthetic materials, very similar types of manmade fibres, and various different types of natural materials. Each one has a very different type of chemistry associated with it as is. So rather than looking to recreate the wheel, so to speak with different novel approaches to die, they looked at how to create a novel ink chemistry. And so if we look at how we put colour into fabrics today, in a dye bat, you're creating basically, an ink. So water goes in fabric goes in, the dye goes in various different types of auxiliaries goes in, the whole thing is pressure sealed, cooks up to about 130 degrees, depending on which type of fabric you're trying to do lower about 9110, four, say low six. And then you just let it sit there. And looking at probability, the dye, you hope, you know, do the whole turnaround four times and then knock on your head and then pack your stomach and wish that the colour comes out accurately. Right. But that is exactly the precise reason why today in the industry, coloration remains that bottleneck is because it's based on a probability of getting colour into the into the material. But this dye back is nevertheless just a giant liquor of right. So rather than dosing it that way, and looking at it from a probability standpoint, they turn that around. And then that thing, a lot of the inspiration from the paper print industry have directly precise dosage on to the exact spot that you want it on within the fabric, and then fix it on that exact spot.
So because of that precision level, you can see, I'm no longer relying on a probability of getting it in. But physically because it's directly in contact with only that precise spot. And so you have the the colour fixed right there. This whole course of inspiration that I just completed, probably within less than four minutes, took them seven years to figure out.
And then an additional seven years on top of that, to get it to a point where it is commercial. So starting out from just purely research, academic level point of inspiration of curiosity, to expand on, can we do better? Can we not create so much waste, and a byproduct of that initial point of efficiency spiralled outwards where there's like, oh, I don't need to use water during the coloration.
Oh, the energy is actually much, much less because it's so precise. It's so efficient. And so everything else in terms of all the goodies come to play, including better coloration levels, better saturation levels. So yeah, I mean, that's that's kind of how it came to be.
WTiN
I seeso. Yeah. That really is quite a journey, I think for the company. And I'll come on to the benefits of it in a moment. But so am I correct in saying that this is neither sublimation printing or digital printing you've you've somewhat created like a hybrid or its own categories, right?NTX
That's that's spot on. It's It's neither sublimation it's neither digital it's neither wet print and it's neither batch dye or continuous dye but it's it's a little bit of everything all in all the benefits of taking out all the all the nasty bits of and yeah, it's what you said is perfect. It's a hybrid of all of those technologies. So it is its own Marvel process. It's there's nothing else like it.WTiN
Yeah, cuz that's what confused me when I first heard about you guys I couldn't get work out if it was an ink, whether it was a machine or what. So yeah, that makes a lot more sense. So how could someone actually use your technology, then I mean, walk me through one of your machines and how they take a fabric and then you know, all the way through to it having the design and everything at the end.NTX
So maybe I can talk a little bit about that. So I mean, next to what Geoffrey described. On the coloration part, actually, we wanted to make sure that end to end we were using the best available technologies to further drive down all the key indicators of carbonization of our, of our environment. So water energy. So we start with basically a novel way of continuous scarring.So we take integrate, we bring in plasma treatments.
To further activate and clean the fabric, before we go into the coloration steps. And we have to we have the two technologies, what we call the Coltrane's 2.5, which is designed for artwork printing.
That's, I would say an earlier generation but very commercially available.
So we print similar to a sublimation print, but we printed the inks on a on a film. And then in a second step, we transfer the inks onto the fabric. And what we call a cool transfer. So around 80 degrees Celsius, so we don't have the impact that sublimation has on the fabric, we use a high pressure and very high temperature. And you basically make your fabric shiny and you affect your Handfield. That's what the name Coltrane's comes from it actually originally. So we use a cool way to transfer the inks onto the fabric.
And then we go to a fixation process and in a high temperature steamer washing off of any residual dyes, which actually the efficiency of the printing process is very high as 95% plus. So even the washing off which again is on a continuous machine, that we adapted for the for the process. So the water usage also there is very low because and the beauty and the cod values of what is washed off is is very, very, very acceptable because there's a high fixation rate of the dice does. So that's for the print process. If we go into the solid, we developed something what we call the cool trans five, or nicknamed nicknamed the rocket, I think is cool a cool name forever Textile Machine. Now one of textile machines have cool names at least we have one.
So basically that that is a little bit the same principle where we but here we transfer the inks directly onto the fabric without an intermediate step of using media.
So and we apply them on both sides at the same time. And basically, that's where the gravure roller, so we could we for solid colours, we use a solid rollers, and for prints where we can make a print on the front and the backside. At the same time in a different colour. We use engraved floaters with a with a kind of a pattern. And then afterwards, it's the same step as zoom fixation, washing off of unfixed dyes and the final sets to add any functional finish that we would need like softening, antibacterial, water repellency, and so on. I hope that a little bit clearer.
WTiN
It is yes, I mean, printing on both sides. That's quite that's quite unique, isn't it? And am I right in thinking that it is unique? If you do it in one step? Yeah. So how come you guys have chosen to do that? I mean, is there a demand for that sort of thing? Like what are the benefits of printing on both sides?NTX
I've been I've been working in the sports industry on the customer side for a very long time on the sourcing. And every time we we took a development from a sublimation printer, our designers, they were always complaining Why is the back still white, and it's white and you basically see some of the print from the front coming through. So that's kind of what it was one of the reasons why it was driven for you know, and then also to create reversible garments to to make the printing look more valuable because many many many cases actually. You would find like for example, if you look at a reactive distort discharge prints on a reactive dyed fabrics, you dye the fabric and then you destroy it part of it right in our process we we die in print in a way at the same time we can do a solid print on the back end and the pattern on the front. So without using the harsh chemistry using in this charge printing on cotton.And you know, and without affecting any of the other properties on the fabric strengthen so. So it has many kind of I think we sometimes you still find additional benefits every day, like one of them is, for example, all the processes that are continuous, you know that the fabric is in touch with the equipment for a very, very short amount of time. So, we're very good with our process of doing very lightweight fabrics, which are normally very snack or easy to snack.
And in our equipment they don't, because there's just no mechanical interaction. I'm going to add to that, Jessica, actually, which is your question of what is the benefit of that, right. So, colours getting into fabric, one of one of our customers told me, Hey, I got this cool, interesting material.
But we're concerned about the strength in the integrity of it.
Can you help us make it look pretty right colour at the end of the day is making the substrate to look nice. If it's just white, or the off white of the natural materials, there's only so much that you can go at the end of the day, people still want colour in there. And being able to do both sides simultaneously has two separate benefits one of them such as like plaids, or those tartan patterns, right? Generally, you would have to dye the yarn first, before you can create the fabric will now we can just create all the fabric, and then print that exact pattern on there. And it's visually indistinguishable from from from a yarn dye. And so that saves a tremendous amount of time, a tremendous amount of effort, and you don't need to use different types of yarns.
NTX
So the totality of the of the material that is saved the totality of the kerfuffles that happen, because you're using a variation of materials to create that aesthetic are are eliminated, they become obsolete, right. And then the second one reason to be able to do both sides. Traditionally, if we look at some of these fancy patterns that have a have a solid back, or a solid base of that fabric so that it doesn't have that white backing, traditionally, what you do is you dye full on dye the fabric first in a dye that then followed by either a digital a wet print and or a sublimation. And what that does is not only is the process much longer, the lead times much longer. But what are commonly not looked at is each time that you introduce heat, or let's to expand that a bit more each time you introduce high energy into these polymers, right? Whether it be natural, manmade or synthetic, they're, they're all polymers. Each time you can do heat into it, you change the crystal linearity, and that changes the strength. So something that you want it to make look pretty, now the strength of the material is lost. And then you'll have these jerseys on the on the football pitch getting torn apart because the football players were were a little bit rough with each other. Right? And that causes the brand to lose their image because they're like, Hey, am I producing a substandard material? Well, no, it's just that too many processes had to go into there to create that brilliant aesthetic, right? That design the designers took so much pride in because of the limitations of previous technology. That's that was the outcome. But now, we don't need to do that I can print that exact aesthetic in one step without high energy. And so all the intrinsic properties of the strength of the material are retained. So it doesn't weaken the loft. It's not calendered in the same way that you have with with sublimation. So the immediate hand feel of the material feels much more luxurious feels much more premium. And it looks because the colours are so much more brilliant, right when you're not this muted colour with sublimation. And so it pops. It's very eye popping. So I think that's that's another reason why many of the brands have have tagged onto this technology just because it's enabling their designers to do things in a very cost effective way to reach that initial design insight.WTiN
Now sticking with the colours and how it looks like I mean, do you mind telling me a bit more about the colorfastness the rub fastness. The accuracy and and even how it feels as well I mean is the quality any different to other printing techniques?NTX
Basically you know, I think the chemistry of the dyes is derived from if we talk about polyester if we talk about content the same exact dye stuffs that are used in the regular process. So, we are reaching if not exceeding the same fasteners values, but the way that we apply them is is giving us the better results. So, Jeff touched upon the handfeel because we're not using any heat during or any high heat contacted during the process the Handfield is is kept intact, as as best as it can be.We talked about you know fastness you know we have we have printing, we're putting the dyestuffs exactly in the right amounts where they need to be. So we don't have any access. We don't have for example, if we talk about spandex fabrics, we don't have this high absorption rates into spandex that we then need to do reduction clearance, it affects our fastness.
We're using the same dyes as a dispersed dive with a molecule molecular size compared to the smaller ones from sublimation. So we don't have the fastest problems for transport migration or just in general that you have from sublimation inks.
So it's basically trying to combine the best of both worlds and achieving the best in class results in in regard of handfeel colour performance. And all these things add to that generally, if we're doing as close an apples to apples comparison with the exact same patterns, the exact same colours, the exact same substrate that is used, nine times out of 10 are colorfastness going to beat anything else out of the water.
And it's because we're we're we have that exact, precise dosage, the lack of access really contributes tremendously to that Connor colorfastness value, right, we're almost at the theoretical threshold of exactly how much dye should go into any any substrate. And then on top of that, we're not changing the base chemistry right the chemistry is the same as anything else. So what that means is previously colours such as fluorescence, right, forget it, if you want to do that via sublimation, because the colour fastness is going to almost be be zilch, such a high temperature, right, sublimation happens at about 180 to 200 degrees C, to be able to literally sublimate the dye stuff up to those temperatures, if you try using those temperatures with a colour that has fluorescent, right, something that is light sensitive in a in a by its very nature, it's going to kill that, that chemistry. And so we can also do fluorescent colours, without compromise to that colour fastness. We're not changing the chemistry. So generally, the photo sensitivity of of a fluorescent is still going to be the same at about standards about 234 depending on on the material, but A it's doable, and then B, you're going to get the best in class for for colorfastness.
WTiN
Okay, I see. Now, I wanted to ask you about the environmental sustainability of this as well, you did touch on it earlier on. But have you got any statistics around what savings can actually be made using NTX Cool trans?NTX
No, this is the core as I said, the initial starting point for this was how do we create a more better collaboration solution that was those the initial insight, right. And as a matter of fact, the more efficient a process becomes or the more effective the process becomes? The The side benefit is that the environmental impact becomes all that more better, right? I don't use the need to use as much energy I don't need to use a much solvent or carrier or, or, or water or just chemistry, right. When you don't need to use as much, it intrinsically becomes more sustainable. But it's very, very, very difficult to gauge. What is sustainable, right? For example, the exact same plant any kind of dye house today, if we have it, I don't know spit ball here in Indonesia or China. Let's use China where they burn coal, right? And it's probably one of the dirtiest coals in the world.Intrinsically, they plant is going to have a very, very poor proof portfolio or profile relating to the plant.
So let's call it that that has a pollution index of let's just say 100. To make it easy, the exact same plant, I move it over into France where they use all nuclear energy. Immediately, the Sustainability Index is going to go up because nuclear energy doesn't have any co2 emissions, in contrast to coal, and there's no heavy metal leaching sure you got uranium and plutonium, but all right, it was it was looking right. So based off of just those, it's very difficult to gauge what is sustainable, and what is intrinsically sustainable to just that technology. So one of our biggest points at the initial stage, when we're trying to make the claims that hey, this is a more efficient process. The natural question is, well, how much are you actually running on the metre, and without actually running a full LCA where that would involve a lot of long measurements and assessments.
From an auditing perspective of a third party, we collaborated with sustainable apparel coalition, and looked at the Higgs index, where they already have a means of looking at different types of materials, different types of processes, what the and benchmark against this, it's not perfect. There's still a lot of ins and outs of, of the Higgs index that are to be desired. Sure, but it is still at face the simplest ways to make an apples to apples comparison. So we went straight for that. And the Higgs index generates what is called an MSI score. In essence, what I was trying to do with 100 versus 10, here, the Higgs index generates a very, very simple MSI score, where the higher the number, the more impactful it is to the environment. So we said, Alright, I don't know what it's going to look like. But we know just because of how much more efficient it is, we're going to probably be better than any of the conventional technologies, if not comparable to some of the newer technologies, and we thought, supercritical die and or digital dying, or digital printing, we thought we'd probably be in the same ballpark as that comparable.
So what was super surprising, however, is not only were we better by two fold, than conventional dyeing.
Which had an MSI score coming out at about 13. Not only were we better than continuous dyeing, which I believe came in at about 11 or 10 ish, not only were we better than supercritical Dine, which came in at eight, we were even better than then digital insulation, which came in at about seven I believe. So for polyester, our MSI score from input of raw material to an output of finished material, right, so the entire the full cool trans process, not just the coloration, the entirety everything, including the steaming fixation, and the washing for polyester came in with an MSI score of six. And for nylon, it came in at an MSI score of five. Right. So even we were taken aback because one point, it's huge. That's a That's a huge difference. So that was the starting point to really get our foot in the door to talk to the brand houses, talk to people in the industry to say, hey, look, this is not ours claim. But this is what the metrics came out to be.
Sure, it's a starting point, we'd be happy to work with you to look at a full LCA if you want. But hey, numbers don't lie. And this is not from us.
WTiN
Yeah, that's, that's quite impressive. Actually, I am familiar with the MSI. So yeah, that is quite an accolade, isn't it? I mean, it helps you sell the technology I imagined massively, because sustainability is such a huge thing that the industry is sort of well, trying to move towards. Yeah. Now, so far, we've only kind of mentioned everything that's amazing with this technology. But I was wondering, are there any downsides at all? Are there anything that you know, any improvements that you want to make in future?NTX
Oh, Peter, you want to kick off with some of the downsides that I'll talk about butI don't think we don't know what we don't know yet. Right. But, I mean, what is it obvious downside, if you can call it that way, it's that it's a new technology, that you will encounter some challenges.
You know, we when when we when when the company did the r&d for this equipment they
did not, we're not able to test this efficiency on every single substrate, or every single type of construction on every single fabric weight on every single, whatever special things we have indexed.
So, you know, sometimes we get surprises. But I do think that the company did one thing, right, that, you know, eliminated programme was probably the biggest challenge I always see that in our textile industry introducing a new technology is, it's a huge risk for the company that builds it.
Not because it is difficult to well not because of it's not going to work, because if it's not going to work, it's not going to be launched. But our industry is is a nature, still very conservative, and new equipment.
And new technology always gets approached with a large pinch of salt, and probably many other things.
I often compare it to you know, we in the very beginning, the company tried to sell its equipment to some of some established textile factories. And what we encountered was that there was these were like, little kids that got a new bicycle.
And they didn't know how to drive a bicycle. And they tried to bike out and it fell down three times. And then they said bad bicycle.
When I mean is like, you know, they they there was an easy to operate. So they blame it on the equipment, and they blame it on the technology. So I think that is still today one of the biggest challenges to overcome, because we've chosen now to manage our own equipment. So all the technology is rolled out in joint ventures with with partners, where MPX is having at this point in time, all of them are controlling stake. So that we can closely help our partners to roll out this technology. And then we can also get the feedback on things that are not working yet and fix them back in our r&d, that we also have the opportunity that any improvements that we come up with that they also get rolled out to these jayvees There's no opt out in close. So there's a continuous improvement programme in place. So that I think was was our biggest challenge. And it's still be I mean, there's still every day, things that have happened that we didn't think of, right, but I have not seen anything that was not able to be solved. And move on.
WTiN
Okay. And Jeff, you said you've got some thoughts on the future?NTX
Oh, absolutely. I mean, so I've spent practically my entire adult life in research and innovation, this is probably the, the the first for me to actually get into the full commercial side of things, the the actual, you know, getting into the trenches and fighting the good fight. But I joined and TX because this is just the beginning. And having that control of the actual manufacturing the operations as Peter said, This is so critical for your ivory tower eggheads, right? We we pump out great stuff in a laboratory, I can do almost anything I want, I can create this incredible sensor that can look at magnification or sensing of a chemical at the parts per billion level. But then that sort of vernacular on on the everyday person it's like okay, why do I even care about something like that? And then you go into the details of all right, cancer detection, various different types of genetic detection, I mean that that has its has its place. But the critical bridge that has been limited missing and why we often on have brilliant innovation, brilliant research, but you don't really see that going into the the the actual commercial side of things or you don't really see that going onto your shelves, is because to commercialise something to scale up is ridiculously difficult. It's a completely different lexicon between the laboratory and the factory floor. It's completely different vernacular, again, where you're talking about from the company and then on the on the consumer to actually do manufacturing for the brand houses. They speak in acronyms that your general person has absolutely no clue what it even stands, but because everybody has gotten so used to it and they're on tight schedules, looking to meet timelines and deadlines for for their customer at the retail level and so on and so forth. That that efficiency becomes a culture and of itself. And so the laboratory completely loses it right. They don't know. Why is it my stuff can't get out there.And it's because as Peter said, Everybody's blaming the bicycle. But the lab technician doesn't have the insight of what's happening on the laboratory floor on the factory floor, they don't have the insight of what the what the brand house is actually asking for. And so here, potentially x star started out as an innovation and research facility, that is still the core of the company, that is still the heart and soul of the company, which is in research and innovation. So we know what we know, today. We know, as as Peter had also mentioned, we have our series 2.5, we have our our five with the sexy name of a rocket. But each one of those is a is a tweak on the previous one, because of knowledge gained from the factory floor from the, from the brand house, right? This type of ecosystem never existed before it was you had your machine manufacturer on one side of the table, you had your chemistry, let's call them the software. So the engineering would be the hardware, you have your dye chemistry, that would be the software. And then you had your user. These are three different companies. And then at the end of the day, you had your brand house was was the fourth leg in the room. And none of the guys were spoken, speaking on the same terms. Now, all three, the engineering, the hardware, the software, and the user are all in one singular unit. And there were speaking directly with the brand houses. So it is unparalleled in terms of the degree of insight that our researchers in the labs actually have, it is unparalleled in terms of the actual detailed problems going on on the factory floor that again, can be solved with with clever solutions. And so also what that tells us is now what can I do better? Right? We have our rocket Well, what's after this warp speed? I don't know.
It just becomes completely different language that we're talking now. Because we have that insight. So it's very, very exciting. Yes, it sounds it'll be interesting to see what you guys will be doing in another seven years and another seven years after that and see where you are, then no more seven years. Let's cut that down to seven months.
WTiN
Okay, well, I'm just looking at the time. And unfortunately, we've only really got time for one more question. So if anyone listening to this podcast today is really intrigued by your technology. How can they access it? I mean, Peters already mentioned that you kind of work on a joint venture basis. So where are your production plants? And you know, how much capacity Have you got to work with people.NTX
So I mean, we have an aggressive plan. So as of today, we have facilities that just do the cool trends 2.5 printing only in Thailand, and Vietnam. That's just for the printing side. And then we have the facilities where we're rolling out the rockets, which means purpose for the moment is solid die, which is Cambodia,Indonesia, and two facilities in Vietnam. And the locations are actually chosen to develop, meeting the needs from from our brand house customers.
So it's localization, to be near to their gown making facilities, and also differentiation. So the first focus is on polyester. Cambodia, is focused on knitwear, Vietnam's first facility will be focused on woven products. And that's how we plan to continue to roll out we hope to have one or two more facilities in Vietnam by the end of the year, one focusing on accessories, products, and other focusing also on knitwear and with a kind of a new way of vertical integration. So yeah, it's it's, I mean, as for partnerships go, it's to be in the right location, we want to expand our products, we want to expand looking at cotton. Next, I believe, but then as a customer as a as a brand itself, get in touch with Jeff and his team, that is specialists that are going to get your beautiful fabrics. Log on to www.ntx.global. Plug that right there.
WTiN
Well, it sounds like all systems go then yes, definitely. Well, I mean, as I said, I think that's all we've got time for. But thank you so much to both of you. It's been a pleasure to have you on the podcast today. And I mean, this really is an intriguing technology, I really mean that. And so thank you for sharing your insights about it. And well, I wish you all the best with this solid plan that you've got moving forward. Thank you.NTX
Thank you, Jessica. Thank you very much. Yeah. Appreciate it.
Have your say. Tweet and follow us @WTiNcomment