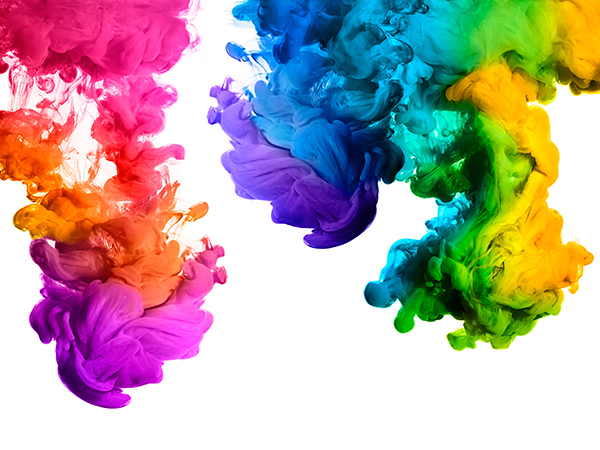
Sponsored by Colorobbia
After leading the digital transformation of ceramic decoration, Italian group Colorobbia has applied its expertise in pigment inks to digital textile printing.
The digitalisation of textile printing has been ongoing for over two decades, with the market share of digital textile printing continuing to grow.
Digitalisation has typically involved small and medium-sized manufacturers of printing technology, software, ink and process chemicals. Rather than causing disruption, this digital transformation has brought the entire supply chain together, such as in the ceramics industry previously.
Beginning with the first single-pass printers in 2000, by 2010 digitalisation in the ceramics industry was already well under way. This was due to the joint initiative of tile manufacturers, machinery builders and a few groups involved in the formulation of dyes and glazes. In the latter category, Colorobbia has 28 subsidiaries in 18 countries, over US€600m in turnover and 2,000 employees. The company holds a 13% share in the global ceramics market.
The Italian group, which celebrates its 100th anniversary this year (2022), has based its strategic headquarters for inkjet development in Castellón de la Plana, near the Spanish city of Valencia. It was here, in 1995, that Colorobbia opened its first digital R&D laboratory. Two decades later, in 2016, the company launched an investment plan to formulate and produce inkjet inks for textile printing.
Inkjet focused
Established in 1988 to produce frits, glazes, pigments and other products for the ceramics and glass industries, the production unit in Spain covers 400,000 sqm. It employs 470 people, 30% of whom are graduates and engaged in R&D.
Edoardo Bocini, system & processes integration, Colorobbia, says: “Colorobbia España has made diversification its strong point. We based the development of our inkjet dyes in Castellón because it was here that the digitalisation of global ceramic decoration began in the late 1990s."
Along with the district of Sassuolo (Italy), which has allied in favor of sustainable energy transition, the Castellón De la Plana cluster is Europe’s leading ceramic production hub. It is home to more than 200 tile manufacturing companies and manufacturers of frits, pigments, machinery, a university faculty, laboratories and research centres, as well as art and design schools for ceramics.
Like the textile sector, but for different reasons, the European ceramic industry experienced a sharp downturn in the early 2000s. This gave impetus to the efficiency of digitalised production processes. Colorobbia España produces over 250,000 tonnes of semi-finished products every year, including 10,000 tonnes of inkjet inks.
Gonzalo Trilles de Castro, managing director of Colorobbia España, says: “At Colorobbia we formulate and produce all our inkjet inks in-house using a team of researchers and engineers with decades of experience. We use the most advanced technologies and select the best raw materials to ensure excellent product quality and extended shelf lives.”
Since the start of its venture into inkjet textile ink production, Colorobbia has expanded its production facilities, built laboratories, expanded its mixing and packaging departments and hired 12 new researchers.
Global R&D
Colorobbia España’s R&D, analysis and testing laboratories, together with its technical and commercial departments, employ 30 researchers and form the backbone for the development and constant improvement of the group's inkjet chemistries.
Javier Pérez Martínez, director of R&D and innovation at Colorobbia Group, says: “In 1994, Colorobbia was the first company in Spain, in the ceramic sector, to invest in a scanning electron microscope with microanalyzer – a cutting-edge technology at that time."
He continues: “That was just the beginning of a journey of discovery and investment, which has led us to have one of the best ceramic R&D labs in the world. Today, it is part of a global ecosystem of excellence with other QC and TA labs.”
To develop new products and optimise existing solutions, researchers in the textile R&D lab use countless instruments, including particle analysers, viscometers, PH, conductivity and moisture analysers, dispersers, grinders and drop watchers.
In the analysis lab – serving all company departments and end customers – raw materials, semi-finished and finished products are analysed. This is to isolate individual components of a compound and understand the cause of unexpected phenomena or defects in a customer’s decorating materials.
The engineers of the technical and commercial department produce samples for OEMs and integrators. They also support end users from initial use of the product through to colour profiling and the start of industrial-scale production.
Pérez adds: “We created the T-Inks range to ensure extreme reliability, reduced setup times and minimal maintenance in industrial inkjet printers. For textile printing companies, the ink and printer combination is crucial. That’s why we work closely with the most important OEMs in the digital world.”
In the testing lab, equipped with printers, impregnation systems, dryers, crock metres and washing units, fabrics printed with T-Inks are tested for abrasion resistance, washing, and UV exposure.
“Pigment inks have always been used in home textiles, but it is challenging to create a digital version with all the required properties,” Pérez explains. “By formulating T-Inks, we have developed a product with extraordinary wet and dry rub fastness, and we are proud of the performance we have achieved."
Going beyond the ink
With the strength of Colorobbia’s experience in ceramics – where inkjet printers are subjected to exhausting production cycles, consumption is very high, automation is total and production costs are reduced to the bone – the company says it entered the textile market to change the rules of the game.
The company focused on pigment chemistry, a candidate to replace reactive inks and simplify an objectively complex and energy-intensive process. The group appointed Alberto Ghisellini, an engineer and salesman with a long experience in industrial inkjet, to head up its textile division.
Ghisellini says: “In the textile industry, pigment inks will revolutionise production and eliminate the need to steam and wash fabric. [This will bring] huge operational and environmental benefits.”
He continues: "Colorobbia has invested not only to meet existing demand, but to create and supply a quality textile pigment that will accelerate the transition from analogue to digital at an unprecedented rate."
With product development completed, Colorobbia conducted its first T-Inks tests in 2017 and previewed the product at FESPA 2019 with Zimmer Austria. At the same time, Colorobbia started alpha testing on KERAjet multi-pass printers with a Spanish print service provider. In February 2020, the company finally started beta testing at Spanish company S.G. Hogar, again with KERAjet technology, which was completed in February 2021.
Ghisellini explains: "We have completed a five-year process of market analysis, research, development and formulation. Today, we are ready to support the digital transformation of the textile industry and the decorative markets using pigment inkjet inks."
Performance vs affordability
With T-Inks, Colorobbia wanted to overcome all the limitations inherent in inkjet pigment printing. This means offering products and services capable of effectively supporting the high production volumes of industrial customers and guaranteeing quality and cost-effectiveness that would justify replacing pre-existing analogue and digital technologies.
Ghisellini says: "Our offer goes beyond colorants and focuses on technical and application support. In textiles, we offer consulting throughout the entire workflow, from substrate preparation and colour management to printing and finishing."
T-Inks are available in CMYK process colours, plus Red, Green, Orange, Light Cyan, Light Magenta and Light Black. The product is packaged in 1kg bottles, 5kg canisters and 1,000kg tanks to feed centralised pumping systems to printers. T-Inks are compatible with Fuji Dimatix Starfire print heads with recirculation, on which Colorobbia offers a two-year warranty. Other print heads, with and without recirculation, are currently being tested.
Prints made with T-Inks have been tested for washing according to ISO 105-C06:2010, and wet and dry abrasion according to ISO 105-X12:2016. The inks never scored less than 4 out of 5 and 3 out of 4 respectively.
In the bleaching resistance test, performed according to ISO 105-N01:1993, and in the light fastness test, performed according to ISO 105-B02:2014, T-Inks achieved an average score of 5 and 8 respectively - the highest score available.
In addition, T-Inks successfully passed (5/5) the dye migration test in PVC coatings. These were conducted in accordance with ISO 105-X10:1996. Moreover, T-Inks have achieved Eco Passport by OEKO-TEX certifications and the ink range also complies with Inditex protocols on the absence of formaldehyde, amines and phenols.
Courtesy of flexible manufacturing, a 12-month shelf life and a direct distribution model that does not depend on external logistics, distributors and retailers, Colorobbia delivers T-Inks directly to printers, reducing time-to-market and product price.
Ghisellini says: “T-Inks cut decoration costs by 30% compared to average market values. We are competitive with both inkjet reagent and screen-printing pigment. In the future, T-Inks will be even more advantageous.”
Ready for the challenge
Colorobbia comes to the textile pigment market with the strength of its production and logistics units in some of the most dynamic textile markets: Italy, Spain, Portugal, Turkey, Brazil, Mexico, the US, Vietnam, China, India and the UAE.
When adequate volumes are reached, the group is ready to build mixing and packaging plants in one or more locations. Colorobbia has a global team of hundreds of field engineers, customer service representatives, colour and application experts and a physical and remote support infrastructure covering all major languages and time zones.
Have your say. Tweet and follow us @WTiNcomment