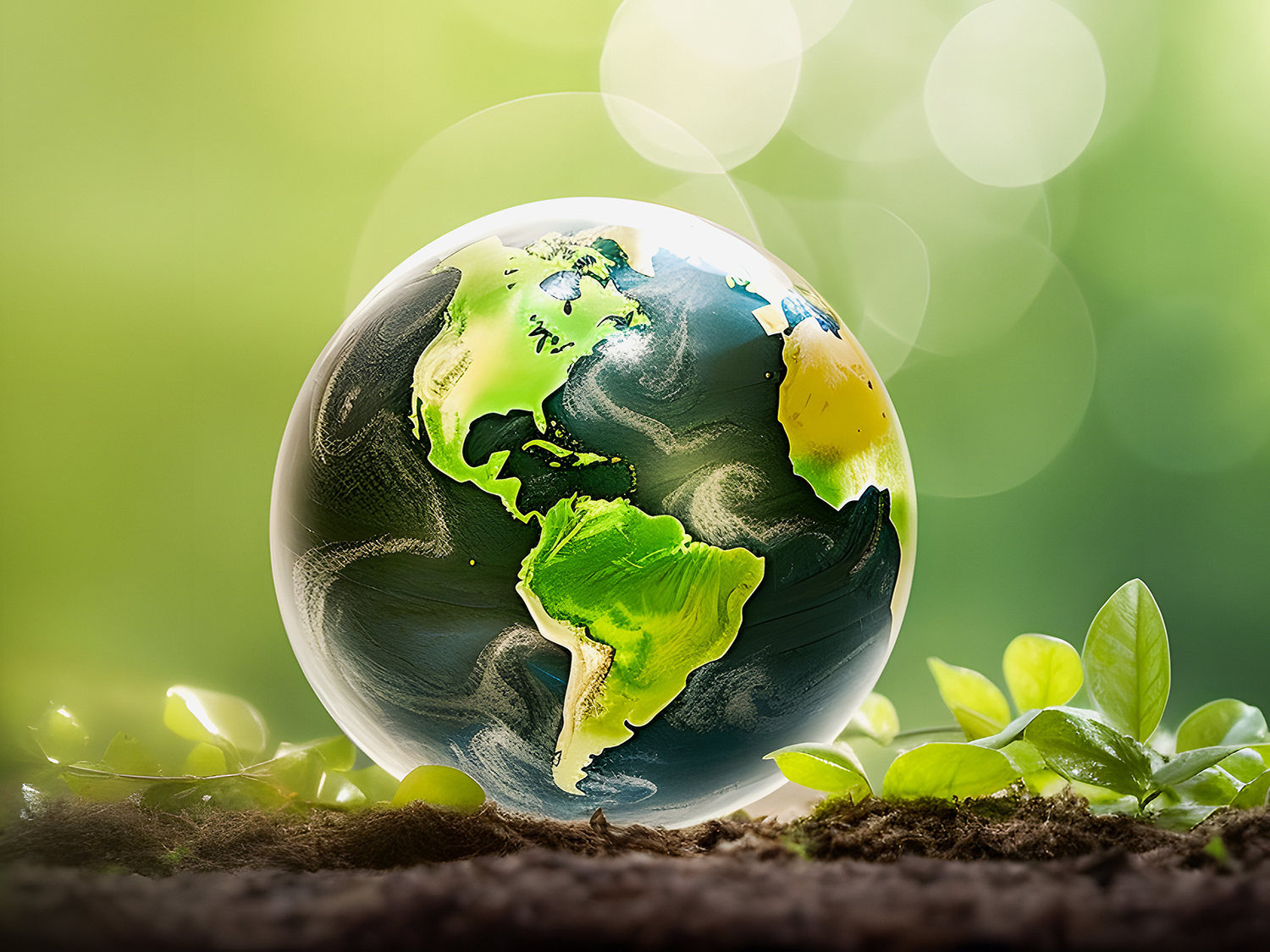
Sponsored by Fibrant
WTiN’s recent Innovate Zero Carbon event highlighted the importance of reducing the carbon footprint of the textile and apparel industry. This emphasis is closely aligned with the industry’s ambitious emission reduction targets to:
- drive the pressing need to combat climate change
- evolve public sentiment
- prepare for the upcoming legislation under the European Union’s Green Deal initiative
To effectively decarbonise the textile apparel market, it is critical to assess the entire value chain – both upstream and downstream – and to focus on processes and materials that have the greatest impact on the overall carbon footprint. It is critical to recognise that the textile and garment business extends beyond the yarn level, particularly when working with synthetic materials such as nylon or polyester.
Upstream chemical processes responsible for polymer manufacturing frequently have a significantly larger environmental impact than yarn spinning (see Figure 1), weaving/knitting, garment assembly, or transportation. As a result, it is evident where the most significant reductions can be made.
When looking downstream, nylon is well known for its versatility and comfort, as well as its outstanding durability, which makes it the ideal material for re-use. It has more longevity than other textile materials, which greatly reduces its overall environmental footprint – a fact that is often overlooked in material selection.
Examining the upstream perspective, nylon is associated with a relatively high carbon footprint due to the complex and energy-intensive polymer manufacturing process. Recognising that more than 90% of the carbon footprint of one kg of nylon yarn is attributed to the precursor’s (caprolactam) production highlights the huge potential for decarbonising nylon-based garments.
Fibrant has taken on the challenge of decarbonising nylon. It has invested heavily in proprietary technology, process optimisation, conversion to 100% renewable energy sources, and cutting-edge technology for capturing and neutralising the vast majority of greenhouse gases (GHG), transforming them into harmless non-GHG gases.
This initiative resulted in the invention of EcoLactam®: an ultra-low footprint nylon solution. EcoLactam® Impact has a carbon footprint that is up to 70% lower than standard nylon. In practice, using EcoLactam® Impact can save up to eight tons of CO2-equivalents for each ton of nylon consumed, contributing significantly to Scope 3 emission reductions.
EcoLactam® also comes with a fully accredited and third party-reviewed cradle-to-gate life cycle assessment to ensure transparency and validate sustainability claims.
With this level of reduction, EcoLactam® impact offers a footprint even lower than traditional polyester and cotton. In Figure 2 the results of comparative footprint study are shown between a knitted shirt made from EcoLactam®, polyester, cotton and traditional nylon.
Time is running out, and swift action is required to reach our collective carbon reduction targets. To have a genuine environmental impact on a global scale, collective action is necessary by reducing in substantial volumes. With a capacity exceeding 250 kilotons, EcoLactam® Impact is available globally on an industrial scale, poised to deliver a substantial global impact.
EcoLactam® - the impact that counts.
For more information visit: www.fibrant52.com/ecolactamfootprint
Have your say. Tweet and follow us @WTiNcomment