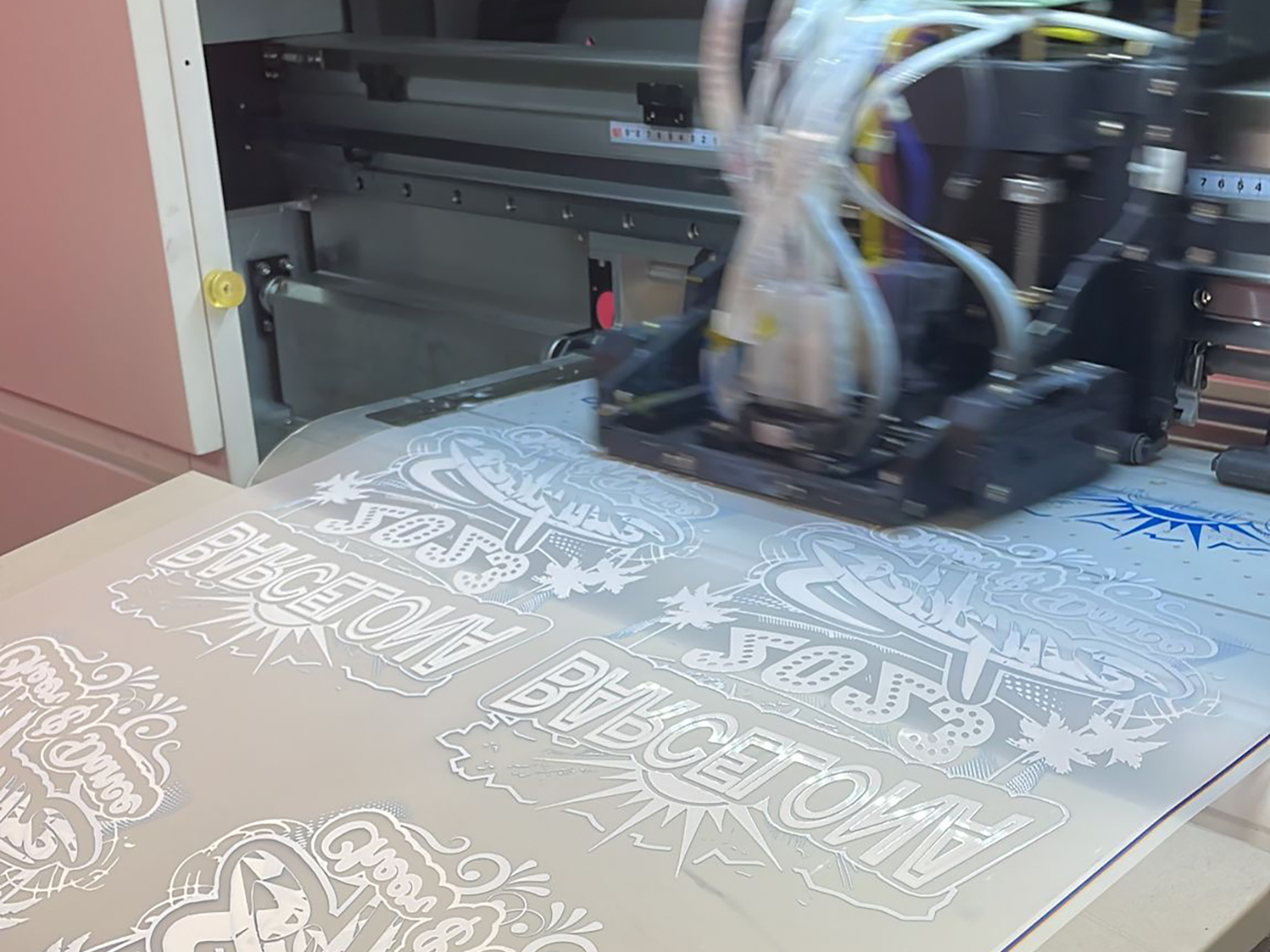
WTiN examines direct-to-film (DTF) printing technology and the reasons why it has gained so much traction in the digital garment decoration sector.
-
Understanding the commercial readiness scale
WTiN’s Commercial Readiness Scale gives an indication of what stage of commercialisation a product is at. It ranges from Emerging: a research stage development; Scaling: the product is being produced on a small but growing scale, and Commercialised: the product is well-established and ready to purchase.
Summary
- While direct-to-film (DTF) printing sounds quite complex, it is an extremely efficient method of providing full-colour graphics to dark or light-coloured garments.
- DTF’s popularity as a garment decoration technique has grown enormously in its short lifetime.
- When working smoothly, the DTF process is an excellent, cost-effective and rapid manufacturing process for garment decoration. However, the technology is not without its challenges.
Introduction
Around three or four years ago, videos started emerging from China about a new garment decoration technique. While some ignored this technology as an industry fad, others explored the process a little further. Once samples started reaching customers and they got to touch and feel the digital transfer technology, word began to spread quickly. The technology was coined ‘Direct to Film’, or DTF for short. Fast forward to today and you will find DTF technology at major trade shows and machines implemented in thousands of print shops worldwide. Its popularity as a garment decoration technique has grown enormously in its short lifetime. This article will explore DTF technology along with the challenges, popularity and the future.
Process
DTF is a digital transfer method for the decoration of (primarily) garments. However, other applications can be used.
While the DTF process sounds quite complex, it is in reality an extremely efficient method of providing full-colour graphics to dark or light-coloured garments.
An inkjet printer is used to print a CMYK image (in reverse), followed by a full cover of white ink onto a filmic substrate. The image then passes through a light heating stage to evaporate the water from the ink, leaving a tacky image. The film is then covered with a hot melt adhesive powder. The powder will stick only to the tacky areas where ink is present. Excess powder on the film is shaken or beaten off. The powder-covered images are then passed through an oven to ‘cure’ the image and fuse the ink and powder together. The film can now be stored or used immediately to press the image onto a garment.
The transfer process for putting the image onto the garment, employs a traditional heat press. A garment is prepressed to remove moisture, then the image is placed on the garment (powder side touching the fabric), pressed and then the film is peeled away, leaving the image transferred to the substrate. A second press is recommended to further bond the ink and hot melt adhesive to the textile.
The technology
Consumables
The DTF process requires three key consumables – ink, film and powder.
- Ink: The ink for DTF is a water-based pigment ink containing binders. Most DTF printers are set up with the configuration of CMYK + white ink. White ink is the most complex of the formulations and is used in significantly larger quantities than the CMYK. Similarly to Direct to Garment ink (DTG), the white contains titanium dioxide (TiO2) as the colourant. TiO2 is a dense compound and has a natural tendency to settle in low viscosity systems. To mitigate for the settling of the white pigment, DTF printers are usually equipped with recirculation systems and stirrers within sub-tanks to keep white ink moving.
- Film: The majority of DTF film has a polyethylene terephthalate (PET) liner with numerous coatings on the substrate. The coatings on the film are required to allow firstly for the aqueous inks to wet the film properly (inkjet receptive), and also for the release process to happen efficiently. Different coatings will dictate whether the film is ‘hot peel’ or ‘cold peel’ – ie whether the image can be peeled away straight after pressing (hot peel) or after a cooling down period (cold peel).
- Powder: The powder employed in the DTF process is a hot melt adhesive. Typically, the powder is based on polyurethane technology (although some powders are blended with polyester adhesives). The most popular powders appear white in powder form and are transparent in melted form. However, other specialised powders are often employed. For example, many users prefer to use a black powder when transferring to a dark polyester garment, as they have found this reduces the re-sublimation of dyes in the polyester garment back into the white ink layer.
Hardware
The hardware for DTF consists of an inkjet printer (at the time of writing nearly all systems employ Epson inkjet heads) and then the powder/oven unit.
The powder unit will release powder from a hopper, which is then shaken over the image areas. Excess powder is removed and reused by placing back into the hopper.
Challenges
When working smoothly, the DTF process is an excellent, cost-effective and rapid manufacturing process for garment decoration. However, the technology is not without its challenges.
Firstly, from an ink perspective, the main challenge is related to white ink. As mentioned previously, the white pigment (titanium dioxide) is a dense product, which means naturally it will settle in a low-viscosity aqueous system. Most DTF hardware has been adapted to cope with the white ink (stirring and re-circulation). However, from an ink development and manufacturing perspective, the ink needs to be developed so that it has “soft settling properties”. This is where any settling pigment forms a soft sedimentation on the bottom of the vessel, which is easy to redisperse back into the bulk liquid. Poor ink formulations will exhibit ‘hard settle’ where a thick sedimentation forms that cannot be re-dispersed. If hard settling occurs in the printer and eventually reaches the printhead, this can cause serious issues and block the tiny inkjet nozzles with oversized particle agglomerates.
Anyone who has used an inkjet printer in their office will have sometimes come across the dreaded paper jam, which can cause mess and frustration. All inkjet printers can suffer this, no matter how big or small. With DTF, however, the ramifications of a ‘head strike’ can be a bigger headache. The film substrate DTF employs has a coating applied. If the printhead has a serious “head strike”, the coating from the DTF film can transfer to the print head surface and react with the ink in the nozzles, resulting in blocked heads. Inkjet heads are expensive, so this can cause loss of time, production and money. It is important to ensure that the substrate media is running smoothly through the DTF system to avoid this head strike scenario. Many DTF printing systems have a vacuum bed, which prevents the substrate from lifting up and causing a head strike.
External conditions
Room temperature and humidity can have a large influence on the success of DTF printing. Fluctuations in both of these external variables can leave DTF print operatives scratching their heads as to why today’s print is not matching the quality of yesterday’s.
Changes in temperature can affect the viscosity of the ink, which can change the way the ink runs through the printer. It can also affect the evaporation rate of water from the printed film.
Humidity can change the interaction between the film and the powder. DTF film and powder like to be kept in dry conditions, so an increase in humidity can lead to excess powder sticking to non-image areas of the film. Keeping the environment too arid may be good for film and powder, but the print heads like to have some degree of relative humidity to avoid their nozzles drying up.
Overall, the DTF process is a balance. Large fluctuations in external conditions may lead to operators having to change the process slightly to accommodate them. Experienced users will learn the best operating conditions and react accordingly. For best results, it is advised that DTF printers are kept in rooms with some form of climate control, such as heating, air con, or humidity control. However, this is not always practical for many smaller print shops.
Most industrial DTF systems will have heating plates prior to printing to pre-warm the substrate as well as heating plates underneath the print area and after print. These help to standardise the conditions for printing.
Popularity
DTF printing has grown at an enormous rate in recent years. With a relatively modest investment, print shops can invest in the hardware, software and consumables required to create a digital garment decoration line, all within a small footprint (often suiting smaller print shops). DTF technology has been embraced and implemented far more successfully than DTG was in the early days. DTG technology was often seen by traditional screen printers as slow, expensive and unreliable. DTF, however, has already made significant inroads into the garment decoration market. DTF crosses over many different garment decoration techniques and has started eating into market share from screen print, DTG, white toner, print and cut and dye sublimation. While the technology is not a panacea for all garment decoration, it is capable of achieving excellent results at high speed in a digitally controlled format. Hence its popularity.
Cost
As with any print process, the cost is really determined by each specific job. What is obvious to all is that some print runs suit the DTF process perfectly, making it extremely cost-effective for numerous jobs. Compared with other print runs, DTF also appears to balance the cost, speed and performance levels of a larger scope of print runs. Take, for example, a print run of 100 multi-coloured T-shirt chest logos. Before the emergence of DTF, the best available option for this were screen or DTG printing (assuming a cotton shirt was used). This size of job sits somewhat uncomfortably between both these technologies. With DTF, within a matter of a few minutes, the designs can be printed and cured with just the short pressing time remaining. One hundred shirts can be complete in a short space of time and there would likely be a similar time frame to screen for this magnitude of job.
While the DTF process consumes a lot of resources – such as ink, film and powder – the relative cost of the consumables is affordable, and the time saved compared with other garment decoration techniques is a huge consideration for print shops. When also factoring in the relatively low cost of start-up hardware, the process is extremely attractive to print houses, hence the surge in uptake of machinery over a short space of time.
Future
DTF printing has by no means reached its saturation point, with more machine resellers appearing all the time. Distributors continue to report high sales of new machinery.
The vast majority of DTF consumables are currently manufactured in China. However, we are starting to see a shift, with ink companies in Europe developing high-quality formulations for local markets. European ink manufacturers have realised the potential of this lucrative technology and have seen the opportunity for the regional manufacture of high-quality consistent quality products that don’t incur the import duties and freight costs associated with products from China.
From a technological point of view, the development focus is likely to be on creating more robustness in the systems – be that in the consumables, the hardware or the process itself.
Other likely developments will be in reducing the environmental impact of the system. While the digital printing technology has obvious environmental benefits, there are some downsides. The primary environmental impact for DTF is undoubtedly the wasted PET film, which is used in the system. Some manufacturers are addressing this by using a significant portion of recycled material in their liners.
Paper-based substrates have also been developed to reduce the environmental impact – however, these are not as widely used. The extent to which paper-based substrates would be an environmental benefit would require further investigation. Depending on the coatings applied and the processes used to manufacture the substrate, this could lead to a product that is harder to recycle than PET-based solutions.
Environmentally speaking, most ink formulations now made in Europe carry the Eco Passport from Oeko-Tex as standard, as well as eliminating harmful glycols from their formulations. Monoethylene glycol and Diethylene glycol are common co-solvents/humectants used in water-based inkjet inks (especially for DTG, but a lot of ink manufacturers are looking to eliminate these from their formulations).
The advent of “powderless DTF” is already in the late development stages, where a liquid binder will be incorporated into the inkjet process to act as a secondary binder to those present in the ink. A digitally applied liquid glue will eliminate the need for the powder process. The technical challenge here will be to achieve the levels of fastness that the powder glue currently provides to the process. To incorporate the binder into a liquid jettable formulation, formulators must abide by the restrictions of inkjet technology (viscosity limitations), therefore it is a larger technical challenge to provide the benefits of a full cure thermoplastic polyurethane (TPU) powder.
Conclusion
The versatility of the DTF process and quality of finished print has been the reason for its huge success over such a short period of time. Many people think DTF will replace DTG printing, print and cut vinyl and other garment decoration techniques but, while it has undoubtedly stolen market share from some of these sectors, it will not completely replace them. Screen print will continue to dominate for large-run, low-cost garment decoration. Industrial DTG will still have its place. It is more likely that DTF will enable access for many new companies to provide digitally printed garments, either by printing themselves, or by buying in pre-printed “gang sheets” of film, which small decorators can use to produce garments with the minor capital outlay of a heat press.
Nevertheless, the speed of DTF’s adoption throughout the garment decoration industry has taken many by surprise.
The technique is here to stay and will become an important revenue stream for print service providers, as well as consumable manufacturers and distributors.
Paradigm shift for inkjet?
The inkjet industry has had a particular way of working over the last few decades. Concepts have been developed in Europe, North America and Israel, among other places and patents on processes and formulations have been fiercely protected. Most developed inkjet systems have been introduced as “closed”, where users are tied into warranty contracts that prevent the use of third-party consumables to protect revenue streams and pay back the (often huge) development costs. Once warranties expire, third-party ink and consumable manufacturers can take some market share of the consumables.
DTF has shifted this status quo somewhat because the technology and consumables have been developed (mainly) in China, with more of an open approach. While re-sellers of hardware in the west do put warranties on machines – these are not as easy to protect as true offerings from original equipment manufacturers. This changes the way in which third-party consumable companies can operate. Are we seeing a paradigm shift in the development of inkjet technology development?
Key takeaways
- The versatility of the DTF process and the quality of finished print has been one of the reasons for its huge success over such a short period of time.
- DTF will continue to steal market share from other digital and analogue garment decoration techniques, however, this is not to say that other techniques will become obsolete.
- From a technological point of view, the development focus for DTF equipment is likely to be on creating more robustness in the systems – be that in the consumables, the hardware or the process itself.
- Room temperature and humidity can influence the success of DTF printing. Fluctuations in external variables can leave DTF printer operatives scratching their heads as to why today’s print is not matching the quality of yesterday’s.
- With a relatively modest investment, print shops can obtain the hardware, software and consumables required to create a digital garment decoration line all within a small footprint (often suiting smaller print shops).