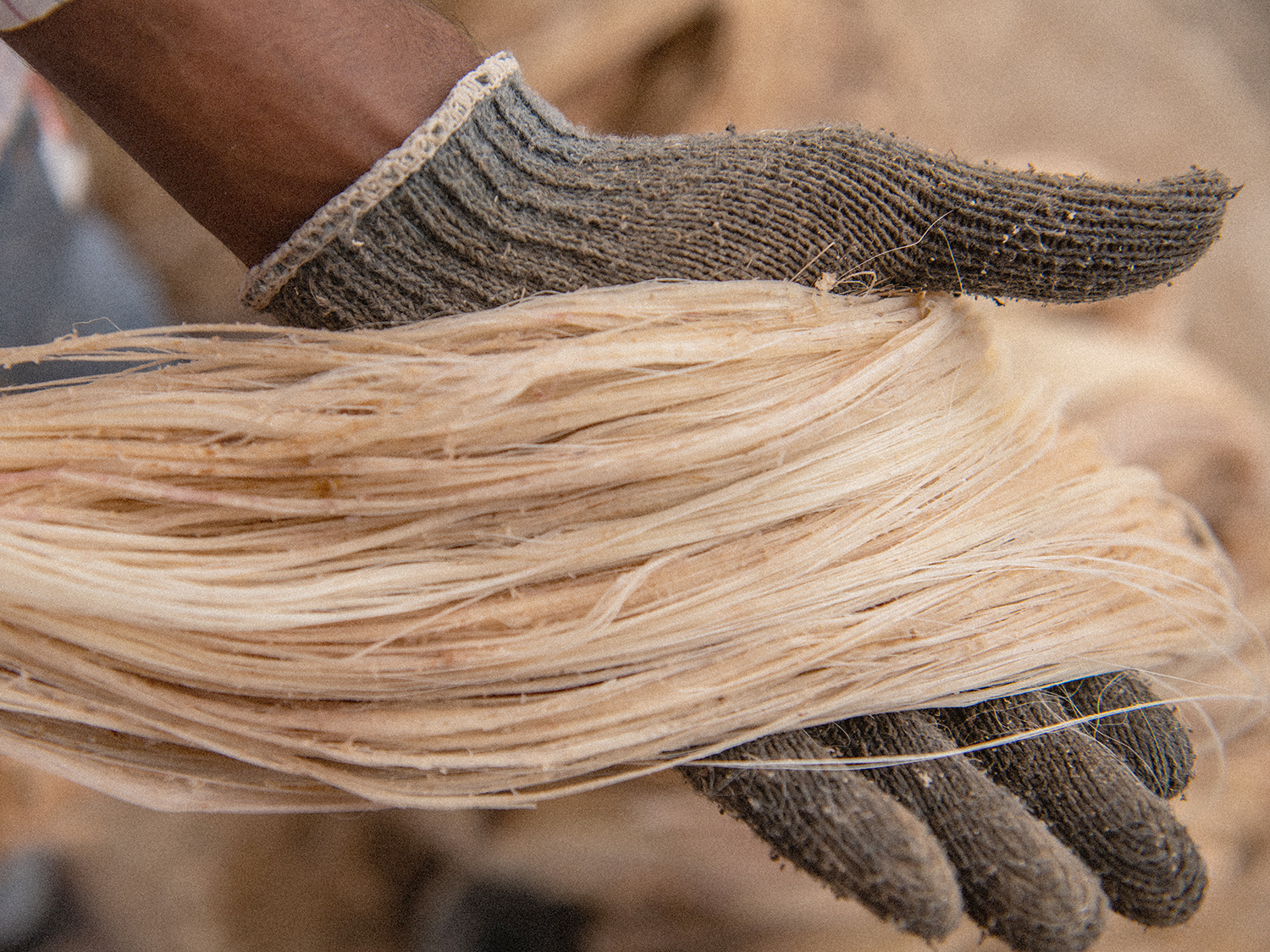
Sponsored by Interloop
Each year, Pakistan produces 155,000 tons of bananas, writes the Pakistan Agricultural Research Council, which results in 10 million tons of annual wastage to be burnt or discarded by farmers [1]. As a large contributor to environmental degradation, plentiful bids to turn banana waste into fibres have made the news – a call to which apparel manufacturer Interloop has answered via its Loomshake TM yarn.
Fahid Hussain, vice president, sales and marketing at the Pakistan-based company, explains banana fibre is a valuable alternative natural cellulosic fibre that can replace cotton by 20% in yarn. As a result, it saves a great amount of land required to grow cotton, an extensive amount of water used for cotton irrigation and that aforementioned chunk of waste.
And since environmental and social ethics are key to the future of the textile & apparel industry, Interloop believes tapping into agricultural waste for textiles – particularly, bananas – is a novel approach to responsible textile production. In using byproducts of the banana fruit crop, industry can forge a more judicious use of the entire plant, avoid use of additional land, and even provide additional income streams for valued farmers – essentially, hitting several of the United Nations’ (UN’s) Sustainable Development Goals (SDGs) with a single arrow.
Loomshake yarn
Interloop’s banana fibre-based yarn, titled Loomshake, first began development in 2017. In April that year, the National Textile University Faisalabad, in collaboration with DICE Foundation USA, organised the All Pakistan DICE Textile 2017 Innovation Event, where Interloop expressed interest in funding a student project to create the decortication machine to extract fibres. Following further development stages – to perfect the spin ability of the banana fibres, “making them as smooth as cotton” – Interloop acquired rights to the banana fibre technology and scaled the process from lab to bulk production. Today, the company transforms banana waste into raw material through a process that utilises the result of this research: the Banana Fibre Extraction Machine.
Integral to the Interloop process, the creation of Loomshake yarn begins at banana farms in Sindh, where banana stem waste is peeled off into layers. Interloop purchases this banana waste to repurpose into Loomshake, consequently cutting carbon emissions through reducing the burning of agricultural leftovers. At the company’s extraction facility in Thatta, in interior Sindh, several Banana Fibre Extraction Machines perform the decortication process. By 2025, Interloop hopes to ensure a consistent supply of fibre – up to ten tons of yarn per month.
Hussain explains the creation process: “The first crucial step is decortication, where fibres are extracted from the stem. These raw banana fibres undergo an open-air drying process to prepare them for further use. Upon reaching our Interloop spinning facility, these dried banana fibres are chopped into short staples and processed by a Mechano-Chemical Process to ensure the fibres achieve the desired level of fineness and fibre-to-fibre opening. After this comprehensive journey, the fibres are ready for spinning into yarn after blending with cotton.”
The properties of the resulting yarn prove beneficial for numerous applications, including denim, hosiery and apparel products. Its lightweight nature and breathing properties may prove positive functionalities for underwear or sportswear, and its moisture regain, fibre density and tensile strength properties mirror qualities seen in cotton and hemp. Elsewhere, its elongation properties are slightly lower than cotton and much higher than hemp. Doubly, its dye pick-up capabilities are reportedly positive, and the Loomshake yarn can be dyed “in any colour, as in cotton – there is no limitation”.
This indistinguishability has led to prolific adoption of the yarn. In August 2023, US-based apparel brand Dinner Service NY partnered with the company to run a first test case of its banana stem fabric for hosiery, reported Fashion Network. Later, in October 2023, Interloop and denim consultancy Simply Suzette launched Unpeeled, a multi-category concept collection that utilises Loomshake yarn to deliver a “fresh narrative” on the farm-to-fashion supply chain.
Hussain explains: “For Unpeeled, we kept the focus on the story and process behind each garment, with an emphasis on the harmony between fashion, nature and community. We built the narrative around authenticity by bringing attention to stories from the farms where the banana fibres are sourced, the farmers who are the collection’s unsung heroes, and the design process.”
Uniting Simply Suzette’s “unwavering commitment to responsible fashion” with Interloop’s “innovative expertise and vision for transparency”, Unpeeled also wields Interloop’s Looptrace technology, a proprietary traceability solution that seeks to share and appreciate the field-to-fashion lifecycle of a garment – and the dedication and hard work of farmers.
Hussain adds: “By emphasising the transparency in our production process, we aligned ourselves with the demand for accountability in the fashion industry.”
Looptrace integrability
Interloop says it is a market leader when it comes to responsible manufacturing, backed by its commitment to combating climate change, tracking emissions and reducing its carbon intensity.
As transparency and traceability rise in importance – particularly with burgeoning information requirements as part of the European Union’s (EU) Green Deal initiatives – the need for a fresh narrative on farm-to-fashion arises from the market’s growing appetite for alternative fibres that have a positive effect on the environment and evolving demands of socially and environmentally conscious consumers.
Thus, Interloop’s Looptrace technology offers an end-to-end traceability solution, tracing from cotton farms to finished products. Hussain explains: “Every step of our supply chain is tracked and traced to give our partners access to transparent raw material information.”
This solution has been implemented in several projects, including those related to Loomshake. The traceability of the Unpeeled collection, for example, has been a “major highlight” for the company, notes Hussain. Using Looptrace to communicate the full history of a garment to a consumer, starting with its farm field origins, will place unsung heroes’ stories first: in bringing attention to stories behind fibres, the farmers are highlighted as key to the supply chain, and their crops brought into the spotlight too. Loomshake also holds the ISCC Plus certification, guaranteeing product traceability, chain of custody transparency and sustainability across its supply chain.
Impact at large
Interloop notes that the innovation at the heart of Loomshake – and its integration with Looptrace – aligns with growing demand for sustainable and eco-conscious practices in the industry. It showcases a shift towards using renewable resources and reducing the environmental impact of textile production.
Hussain says: “It represents our commitment to sustainability, transparency, innovation, and consumer education. These are the cornerstones of a progressive future for the industry, ensuring it aligns with the evolving demands and values of stakeholders and consumers.
“The ultimate goal of using banana stem as a fibre source – turning banana waste into textile fibres – is [to meet] circularity and sustainability principles. This is also aligned with United Nations’ (UN’s) Sustainability Development Goals (SDGs) as banana fibre production provides livelihood opportunities to farmers and contributes to the agricultural economy of the country.
“Interloop continues to find new alternate fibres and remains committed to sustainability best practices as part of our enduring mission.”
For more information, visit www.interloop-pk.com.
Have your say. Tweet and follow us @WTiNcomment
-
Notes
[1] This figure was calculated by Interloop, according to a survey conducted with farmers.