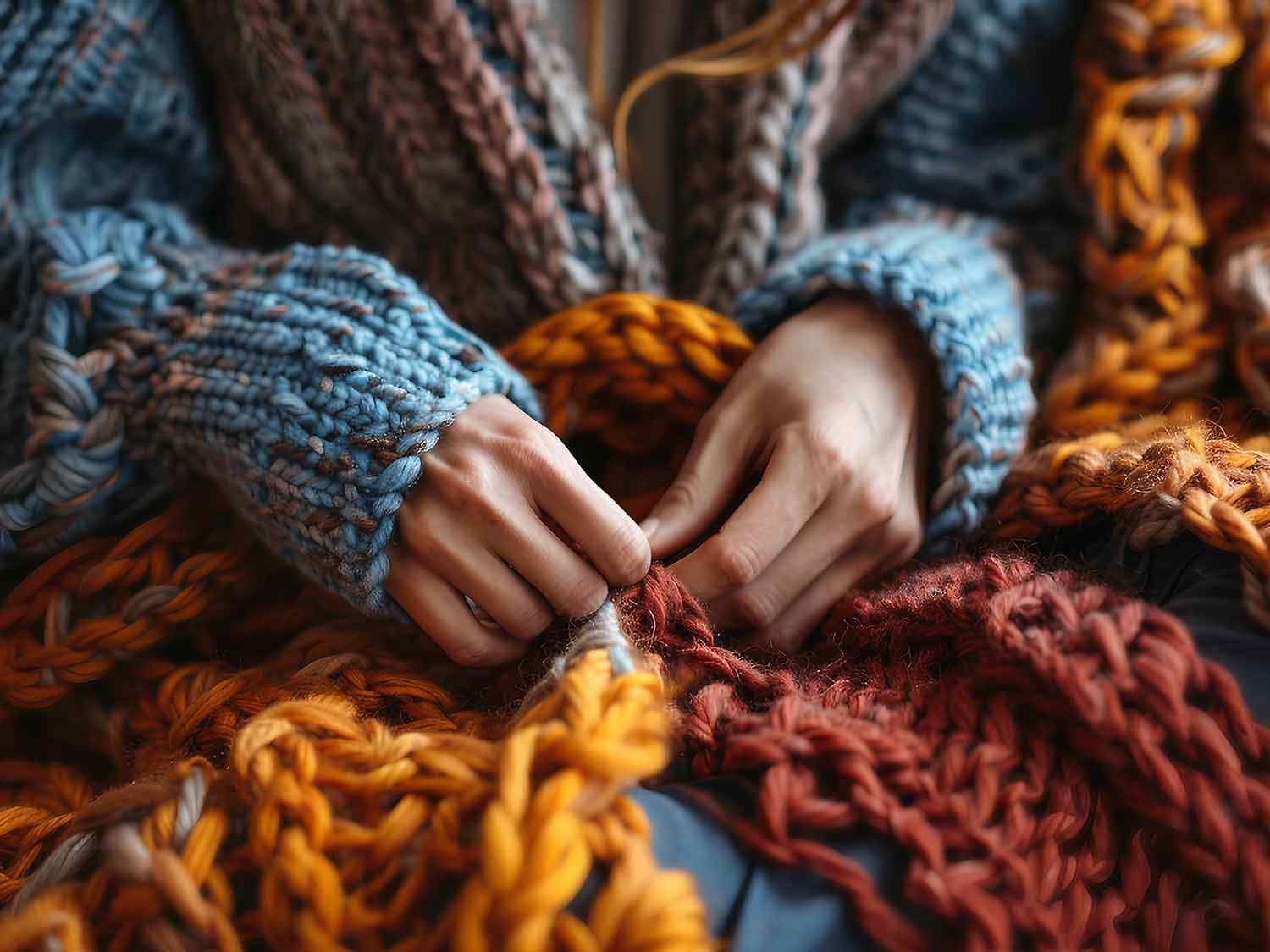
The Textile Innovation Podcast speaks to Thijs Verhaar, owner of Knitwear Lab and Lyske Gais, founder of virtual knitting at Knitwear Lab.
Knitwear Lab develops smart technological applications for knitwear. At its Lab in Almere, the Netherlands, its team of programmers and designers develop prototypes and run small productions. The team of knitwear specialists combine material research with the latest knitwear technologies.
For example, Knitwear Lab has developed virtual kitting, a method of industrial knitwear development, which has the potential to create new opportunities for sustainable, cost-efficient and design-driven sample development and knitwear production. Using Knitwear Lab’s extensive knitwear knowledge combined with the latest 3D software and Stoll Create Plus, a massive waste from sample and pre-production stages can be reduced.
In episode 104 of WTiN’s Textile Innovation Podcast, we speak to founder Thijs Verhaar owner of Knitwear Lab and Lyske Gais, founder of virtual knitting, about the potential for digital solutions in the knitwear sector.
We explore how the sector has developed and the potential for modern technologies moving forward. Knitwear Lab offers a huge range of educational resources and in January 2025 will launch a funding round, to enhance its offering and training opportunities. If you would like to learn more, please visit knitwearlab.nl and knitwearlab.nl/kl-academy.
You can listen to the episode above, or via Spotify and Apple Podcasts. To discuss any of our topics, get in touch by following @wtincomment and @abi_wtin on X, formerly Twitter, or email aturner@wtin.com directly. To explore sponsorship opportunities, please email sales@wtin.com.
Have your say. Tweet and follow us @WTiNcomment
-
Transcript
This transcription has been AI generated and therefore may have some inaccuracies.
Ep. 104: The future of virtual knitting
The Textile Innovation Podcast speaks to Thijs Verhaar, owner of Knitwear Lab and Lyske Gais, founder of virtual knitting at Knitwear Lab.
WTiN: Hi both, thank you for joining me on the WTiN textile innovation podcast, please. Could you tell our listeners a bit about your background and your roles within knitwear lab?
Thijs Verhaar: Yeah, I'm Thijs. I'm the founder of knitwear lab. We founded it 11 years ago with cherish and pal. I'm a very old knitter. In the meantime, I've been knitting for the past 45 years already, and we started knitwear lab out of love for knitwear, and out of the need to have real, I'd say passion and the material enhanced. So knitwear lab started as a material Research Institute for knitwear.
Lyske Gais: Yeah, and I'm Lyske, and I joined knitwear lab about five years ago, the more, yeah, how do you say sustainable matter? I actually have an architecture background. I did spatial design, and I came into network, and I saw that the workflow was quite different from what I was used to. I'm very used to a workflow where we would really model everything before we start building anything. And at knitwear lab, I saw sketches going directly from the desk towards the knitting machine. And there, I thought, there is an opportunity I can do something. So basically, I have love for 3d modeling, and I like software. I like my computer, and I like to see how we can use that, also more within fashion and especially for knitting, that's brilliant.
WTiN: Thank you both. And so knitwear Lab works across a whole range of sectors and offers an array of resources within the knitting industry, as you've just touched upon. Could you explain what the lab does and some of its main points of focus?
Thijs Verhaar: Yeah, I think we have grown the past 11 years from a sample studio into a real knowledge center, and that means we give a lot of trainings to bigger companies like Tommy Hilfiger, and they got long, but also A lot of training to even students design are smaller companies where we bridge the gap between our industrial network knowledge and their design. Need to understand what kind of products they can do in the industry, and for that, we also do a lot of research and development for international brands. And so we develop samples, and we even, we also organize production in Turkey, where we have our own small setup, but also with partners in Europe and in China. But it's all about, I would say the love of well designed and well manufactured and sustainable knitwear amazing.
WTiN: You mentioned that you work with some amazing brands such as Tommy Hilfiger and decathlon. How did you form those partnerships? Did they get in contact with you? Or do you go out to them and be like, we have something amazing that we can show to you.
Thijs Verhaar: Yeah, luckily and unfortunately, most customers come to us. That also means, if they don't come, we have a problem, like at this moment, or the market is quiet, so let's be. Come and but, yeah, most people see us via this type of podcast or via our Instagram, and now we were very present in many situations for many places. So people find us, but we reach out to them. Too.
WTiN: So, the nature of a lab is to test and how do you move from that research stage of development to scalable and commercially viable products which you are offering to these brands and partners?
Thijs Verhaar: Yeah, we I have a I have an industrial background in the sense I had a factory in the past. So I always keep in mind a how to produce things, and we also how to sell things. I think each market has its very specific needs, and it doesn't make sense to make a very complex, beautiful, slash very expensive product for a medium range brand. And so we try to keep this in mind while developing it has to be producible and it has to be sellable. And it doesn't always work like that, because we're design driven. So in everybody, I think most people who love textile is design driven, and sometimes we develop things that are out of price range in our end of chatter, but we I'm the old knitter who tries to not do it too much.
WTiN: And kind of going off like what you do do. So this might be one more for Lyske, but knitwear lab has developed a virtual knitting which is sustainable, cost efficient, design driven, method of industrial knitting. Could you tell me more about this and how you've managed to achieve those attributes while keeping it sustainable.
Lyske Gais: Well, it started with, of course, my experience of, why don't we 3d model first in the computer and then start making I think that's the essence of digital product creation, or the virtual knitting workflow, in that sense, and then specifically for knitting, where I came into with knitwear lab, I saw these beautiful knits. But knit is one of the most difficult things to visualize properly in 3d because it's also very How do you say it's very normal that knitting or fashion is very behind compared to other design industries with their digital workflow. This is because what I was used to was very solid objects, a table, a wall. Sometimes we had a curtain that you had to do, but it wasn't moving or anything, and not knitted. And with modeling, solids are very easy to do and also very easy to render out. But if you go into garments, suddenly things need to move and need to stretch. Gravity has influence. These are, are all very difficult things, and thanks to the gaming industry, basically, hardware became better and software became better, Render Engines and our biggest competitor actually the Japanese. Oh yeah, maybe cut this one out. Sorry, that's fine. Yeah. So stoll started developing a new software with came on and stole is the knitting machines that we use, and they have this software that now is and connected to the knitting machine, but can also visualize the knits that we make as a texture that we can use for virtual visualization. And that, of course, opens a whole lot of possibilities to also make this workflow around it, because it's one thing that you can do it within software, but it's quite another thing to also use it within your workflow. And I think that's something where we are very much working on. We are exploring this quite new software. So there are things to improve, things to figure out, things to talk about with, with stole and came on to see how we can make it better. But there's also to think smartly about how can we apply the software and how can we already use it and make the workflow that we have quicker and without with using. Less samples and materials than we do now.
WTiN: Brilliant, and obviously you've explained quite a lot there. But how have you incorporated the technology into virtual knitting? And as more of a wider perspective, where do you think that in this Where do you think industry 4.0 can take the knitting sector in the future?
Lyske Gais: I think definitely with design, there's a big opportunity with virtual knitting. There's with designers, we always have a big problem with communicating, what do you exactly want, because with knit, the programmer, the technician, has to decide quite a lot for the designer, because the programmer decides on what kind of stitch, how stiff it needs to be, what kind of combinations can be done. So there's a lot of technical knowledge that besides how your knitwear will look, and for technician, that's very hard to explain, except for knitting it out and making a swatch. And if we can already make that virtual and communicate in that way between the programmer, the Network Programmer, and the designer, we can get better designs out there, and with better designs, I believe that's also a big part of sustainability, the better our products are, the nicer they are, the longer we love our pullover, the longer we wear it, and the better, the more sustainable it will be. So definitely within design, I think the biggest improvement could be made, and please, kind of start going after that as well.
WTiN: How have you seen the knitwear industry change since you founded knitwear lab, until like now? And now you're incorporating this virtual knitting?
Thijs Verhaar: I think there is, there are short- and long-term trends, but if I look at the long-term trends, you can definitely see the smaller MOQs think there is. There is a need for more variety in a faster variety, besides the very basic pullovers that are sort of always there. And I think what I also but that's that's also long term trends, is that brands have less professionals in house. They become more and more marketing, sales organizations and less product development minded. So I see the retailers with less well qualified designers in house, and they spend less money on it. So they they put that whole product development part towards the manufacturing side, and the manufacturers are, of course, less able to have the creative knowledge of a market. I mean, imagine you are working as a programmer in Bangladesh or Vietnam or turkey. You have to understand the specific needs of fast fashion in the UK, or fast fashion in Brazil, or all this sub all that, what we as designers are trained to answer and still don't understand all so I think there is a, is a big And, but, you can see people recognize the gap in this knowledge. I speak with many designers who have the urge to understand knitwear because they want to make a beautiful product and they want to know what they're talking about. And there's the factories who are frustrated or frustrated, who feel that their communication is not up to par with the design side. So that's that's also why we feel that virtual knitting, or this whole digital product creation is so spot on for this problem and also for, yeah, the growing lack of craft knowledge, I think that's also a big trend, that there are less and less craft people who maybe understand the products industrial craft.
WTiN: That was actually my next question. Lyske, I believe that you recently presented a talk on industrial craft and its future. Could you tell us what you have been speaking about, and what are some of the biggest barriers in the industry and the challenges to overcome in that in that area?
Lyske Gais: Yeah, it was a talk actually, at the university in America at Cornell, and we had the opportunity to talk to a lot of starting designers and fashion professionals in their sense. And we see, we see a lot of students and starting fashion people. And we see sort of two ways that lots of them go. Either they go the very, very craft Wade, or fashion craft. Let's knit by hand and hand machines and or they move more away from the product. They're more the meta vision, the they don't touch the actual thing. What we need is more the people who can also make products on an industrial scale. So and in this day and age, to do that, you need to love your computer a little bit more than you had to in the past, I think, yeah, but also you need to have a bit of a different view on how to touch the product, you're still touching product, and it's still about tactility, and it's still about making, but it's about making on a different scale and with slightly different mindset. And I think there a lot of students forget that that's an option for their professional life afterwards, that this is where the actual products are being made, and that you are still in touch with the product, but that you have to think smarter and faster and still make beautiful products.
Thijs Verhaar: So that is, I think, yeah, that's one thing. And for me, there is a more sad trend, but that's already going on for hundreds of years. Let's say where, yeah, let's say in the in the 17th century, if you were a craftsman, you would learn for 10 years to become a carpenter, you would make your masterpiece, and after you make a masterpiece, you would be a master carpenter. And not only do you have a craft, but you had status in society, yeah. And nowadays, if you are, let's say your master knit. I know some very talented, very great knitters, but they work in a factory and they have no status. Of course, they have a reasonable income, whether they are whatever country they are, but the people earning the money are are not the cross people anymore. Now, the people who have respect in society are not the people who make things. And I always and there, I'm a bit of a maybe socialist, less Marxist about if I drive through Amsterdam and I see the real big buildings, it's banks, insurance, multinational officers and lawyers, and then I think, Who does actually make something in all these high paid jobs, and I don't I'm not against it, but it's that reality that people who make things that's also why it's sort of outsourced to the cheapest possible countries, because we don't value the making. We need to revaluate making, but making on on a smarter scale, only as a home craft, but no and that sense making makers an honorable profession against young people. Okay, I want to, I'm going to learn 10 years to be a great knitter. I'm a valuable, well paid member of society.
WTiN: What is Knitwear lab doing to bring education to the younger generation and those already in the industry, to pave that future that you or pave that vision that you've just so eloquently described?
Thijs Verhaar: The let's say the knowledge or we're very open. We are. We get a lot of interns from all over the world. We do give our courses. We give our master classes. But of course, we can't change the fact that that we are all slightly underpaid network, and we can't change the fact that people who go into this industry are Yeah, except if they become management in a big multinational more focused on market. The management than on the product. You want to really reach an high financial level. And I think there are a lot of people who can live with it. I mean, I'm, I'm fine with it, but I feel a bit sad. But yeah, I think now the knowledge side we can offer.
Lyske Gais: Yeah, I think that there definitely we are our a lot of our program programmers are, how do we call it home grown? They come in right after school or finishing their studies and to really learn the knitting and the knitwear. That's basically they learn that here in house. And in a way, it's very sad, and in a way, it's, how do you say it's an honor that basically our best programmers get lured away by bigger names and bigger brands. So in that sense, we are growing good knitwear professionals. And they they, of course, also move on. Maybe another or in regards this topic, we are working on a Knowledge Platform, once to create a platform where we have our courses, but also our future Digital Library, and where our knowledge will be available digitally or on a platform, and more accessible to a broader audience, in that sense and more also for designers, easier to gain network knowledge.
WTiN: In terms of digital product developments, which you've already spoken about, how do you see them moving the knitwear industry forward, as you've just been speaking about, in terms of knowledge sharing, and also towards that more sustainable future that we touched upon at the beginning?
Lyske Gais: Now the digital product creation. It offers more than only a smarter, quicker workflow with the use of less materials. It also offers a in that sense, data driven, one of those buzzwords approach where, if we have a digital twin of product, we can, before we start producing it, calculate the impact. We can see what kind of digital product passport that's the other thing that's coming up and becoming very important, next to the digital product creation. But the we can calculate the passport upfront and see what kind of impact our garment will have and what kind of score it will be, and make a good choice before we start producing and also what I hope that is already mentioned, that the industry is going towards lower mlqs, and I think that's very good to it's it's avoiding overproduction, and let's produce what we need. And to know what we need, it's good to see already a bit what we're going to produce and test it out. And there, I think it's the digital product creation can offer more than only a workflow. It offers knowledge upfront before we start producing and I think that's also very important to get the industry forward.
WTiN: Are there any challenges that you're seeing within the industry in implementing these digital technologies that need to be overcome?
Thijs Verhaar: We have, I think the biggest one, we have a Dutch Comic who, which we use a lot, where you see two monks writing behind the desk, and then the one say monk saying to the other, they're writing books. Saying, nah, that book press printing that's never going to catch up. People will always want to read home written or or self hand written books. And I think the fashion industry is a little bit um. Like one of those monks, like we will. We need to feel everything, and we have to have everything physically before we can decide what's going on. So I think actually the conservative passion, but yeah, that's one of the things the other side is the financial pressure where many manufacturers, but also many brand brands are suffering from. I think the the the pressure on a production company is quite enormous, and their margins are low. Of course, we the concept or what we offer with our digital product creation will save costs, but to to do that, you They first have to invest in new knowledge systems. So I totally understand that they're a bit conservative, and that's if you're under pressure. Yeah, then change always will cost at first, a little bit more before it will get better.
WTiN: Okay, yeah, is there any advice these that you give to companies that are considering implementing these technologies?
Lyske Gais: I think what's important, and what many people underestimate, is that it's easy to buy a system, or it's easy to buy software, it's easy to buy a machine, it's easy to buy a water cold computer, but it's, it's, you have to invest in people operating it, and have to give them time to learn and to implement it. And I think there a lot of people also, if you talk about software, but you always hope that you push on the do this button and it actually does it. But the reality is that you have to press 100 buttons in certain sequence before it actually does what you want it to do. And this takes time, and you have to invest in people, to teach them, so don't expect it to happen overnight, and that suddenly all your employees understand everything.
Thijs Verhaar: I think it's also a bit of a thing. Let's share knowledge and no, but I think the more we've been talking about this whole digitization already for 10 years with infection, I think it's good. And the bus is getting bigger, and more people are talking about it, and there are more online things, like this podcast, there are webinars, etc, of people also sharing how they are implementing it and how they are using it. And I think only by starting to use it, we will learn how we can use it in the best way. That's the only way. By start doing it, and more people start doing it, the better it will become, and the smoother it will become. And if we keep sharing that and having people trying it out and failing and trying again and failing again to be talk with Benjamin. I think it was. But then we will get there if we keep being reluctant and saying, Well, I'm first going to see whether this will catch on and whether it will work, then we won't figure it out so and of course, with the current financial climate, that's a very hard thing to do. So in that sense, even if you start small, if you implement a very tiny bit of it, but at least then you sniff and you you get the ball rolling within your company. So start small and let it snowball into something bigger. So that leads us on.
WTiN: And Lyske, this is something that I know you wanted to clarify, but please, could you explain what the difference is between a digital product creation and a digital twin?
Lyske Gais: Yeah, I think the word digital twin is, for me, it always, it's, it's, it's one of those words everybody uses and but it's been hyped a little bit for the fashion industry, and that has worked against it, because a digital twin implies that it's really a copy of Your real garment. And that is for fashion, and definitely for knitting, really, really hard. And people, then, if they don't see an exact twin of the physical garment, they throw it away. They just, they say, No, I can't take this seriously. I can't because it's not an exact twin. And that I find. Such a pity, because there I'm definitely an advocate for how I call it, pardon my English, the shitty renders. That's always my because even with a less than perfect visualization of your of your physical garment, you can already gain a lot of knowledge, and you it can already help you tremendously in communicating between your client and your programmer, and therefore I call it sort of digital cousins or digital family members to also say, let's give ourselves a break, because the software is hard, the hardware isn't always up to par, but let's start using it, even if it's not yet a full twin. Let's not fool ourselves that we can only use it once it's a twin. We can use it before that, and hopefully, of course, we do get to a twin. I'm definitely going for that. But, yeah, I find it always a bit of a pity that the word polluted expectations a little bit.
WTiN: And finally, what is the vision for knitwear lab moving forward? And is there anything that you're currently working on that you'll be able to share with us today?
Yeah, I think we're working on our coming year's plan for the digital product passport. We're working on our platform, and we're working on digital but also a digital fabric library, which we will also that will come out in public, also through browser with fee Stitcher. So we are digitizing our knits and making quite some basic structures.
Thijs Verhaar: We will go for a seed funding round in three months. So we're very interested in people who can support us and back us up with their advice and their money to make this happen. We have a first funding round, but we there's a lot to do and a lot to invest to make our dreams come true for the textile industry.
WTiN: Amazing. Thank you both so much for coming on the podcast today.