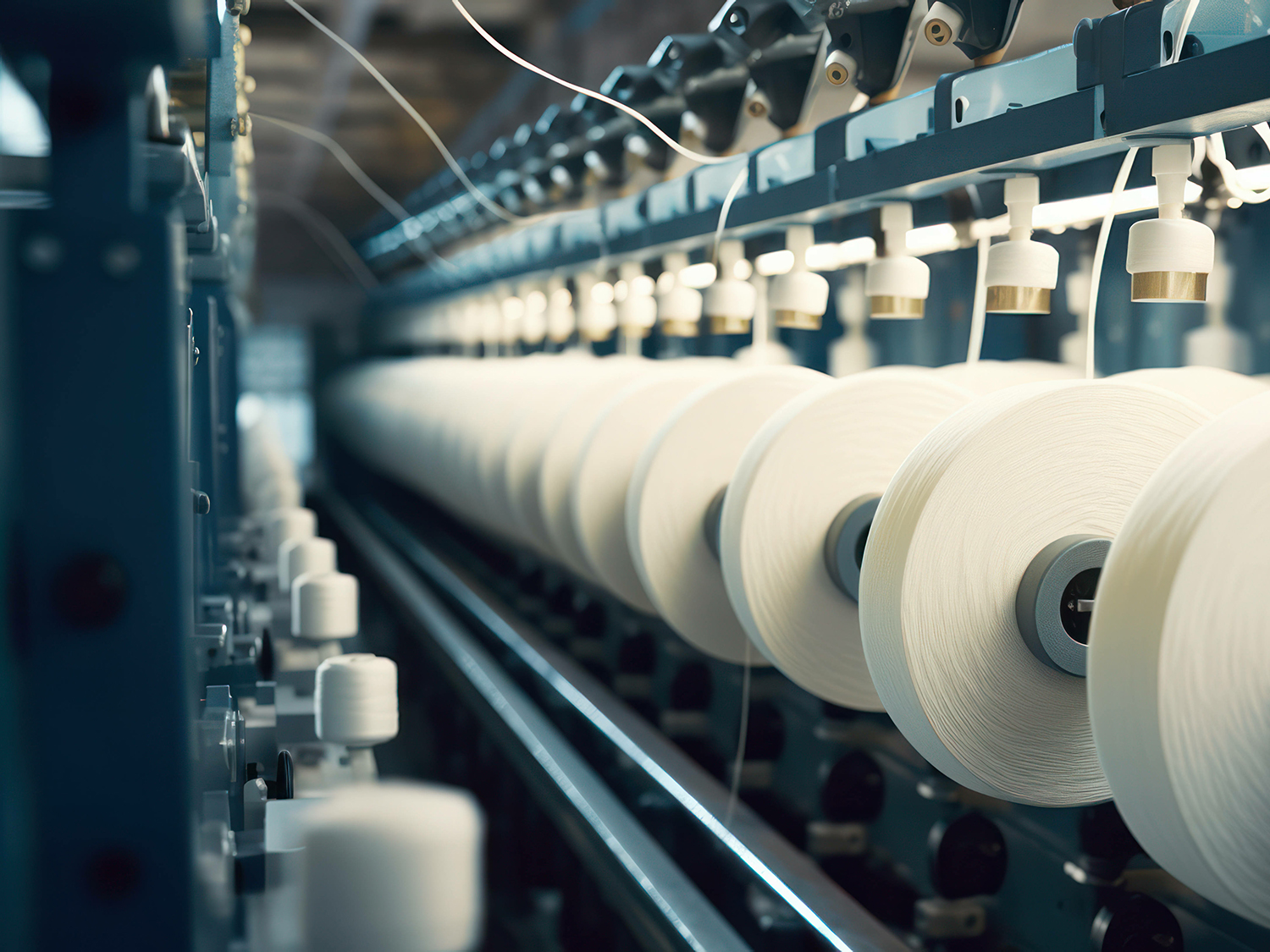
Sponsored by ARISE IIP
Bhavin Vyas, chief environmental, social and governance (ESG) Officer, ARISE IIP, discusses how nearshoring supply chains could be the answer to decarbonisation for cotton supply chains.
Of all decarbonisation strategies, nearshoring manufacturing could offer a promising path to reducing carbon emissions. By shifting production from distant countries in the East to ones closer to raw material production and consumer markets, companies dramatically reduce the need for long-haul transportation (the largest culprit behind supply chain emissions).
What’s more, nearshoring also allows for tighter collaboration and quicker response times, leading to less need for rush shipments and air freight, further minimising emissions. Additionally, it can encourage the use of greener energy sources and more sustainable production practices, as nearby manufacturers face similar environmental pressures and benefit from sharing best practices.
For European markets, the African continent could be the nearshoring opportunity they are looking for.
ARISE IIP has been working on setting up state-of-the-art manufacturing hubs in Africa for the last 10 years. Its most recent project for the textile industry is in the West African country of Benin. Bhavin Vyas, Chief Environmental, Social and Governance (ESG) Officer, ARISE IIP, says that the company’s approach to developing an industrial park in an African country is an “eco-system driven approach”. He explains: “We develop the entire eco-system, which is crucial for the success of industry at the zone.”
When it comes to the textile & apparel sector, ARISE has so far developed textile parks in the industrial zones of PIA in Togo and GDIZ in Benin GDIZ. These parks are vertically integrated industrial zones, focused on creating thriving value chains for storage, processing, manufacturing and export, the company says.
According to Vyas, each zone has:
- A public private partnership (PPP) model of investment for industrial parks
- Availability of locally produced raw material (cotton) both in Benin & Togo
- Availability of uninterrupted power/water/other utilities at competitive prices
- Ready sheds/land area on long-term lease basis
- Proximity to seaports/international airports
- Availability of cotton made in Africa (CmiA), yarn, fabric (woven/knit), processing houses within the zone
- Availability of packaging, labels, printing, embroidery, effluent treatment plants (ETPs) in the park
- Duty free benefits for exports into US (under the African Growth and Opportunity Act (AGOA) & EU (under the European Banking Authority)
- Availability of skilled manpower ensured through garment training centres in both countries
- A compliant zone upholding international standards of ESG and electronically stored information (ESI)
- A relatively young workforce with competitive wage structure
- A safe and secure environment, politically stable country with a business pro-government
The GDIZ Benin-based facility currently has two operational garment factories. Furthermore, preparations are underway for the commercial operation of three vertically integrated textile mills focused on cotton processing. These mills encompass three spinning plants, two knitting units, one woven fabric unit, three processing houses, and three garmenting factories. The PIA Togo industrial zone, meanwhile, has two garment factories in full operation.
Nearshore adoption
ARISE is encouraging brands and retailers servicing European and US markets to switch to nearshore manufacturing in Benin and Togo. When it comes to emission reduction benefits, Vyas comments: “As the EU and US are geared towards imposing carbon tax on goods-importing companies, the search for carbon-light manufacturing locations has intensified.
“We have done life cycle assessments for the products made entirely in our zone using West African cotton versus Asian countries. There is a huge saving (of 60% and more) of carbon emissions during the life cycle of a product (cradle to grave) made entirely in the zone versus one made from imported cotton in Asian countries.”
And, Vyas says, the benefits aren’t just in carbon reduction. He explains: “For investors, the benefits of changing manufacturing to these locations are the low cost of manufacturing in the long-term with duty benefits for prospective customers.”
He adds: “For brands and retailers, the advantage is the nearshore supply base and a diversification option from Asia.” For example, the Covid-19 pandemic showcased all too well the vulnerability of supply chains that were over-reliant on one geographical market. “The lower cost of goods generally is another benefit in addition to the lighter carbon footprint,” Vyas continues.
A number of global brands and manufacturers have already invested in nearshore manufacturing in these regions, according to Vyas. He says: “Many leading international retailers have either started or are in the process of forming their Africa sourcing strategy. Some of these are Walmart, PVH, TCP, KIABI, SanMar, Tandem, Kontoor Brands, Gemo, Bestseller, Decathlon, OTTO, H&M, Jockey, FOTL, Gerber, Carter’s, Garan and Levi’s.”
And in terms of manufacturers, he notes various Chinese, Indian and Sri Lankan manufacturers have “forayed expansions of their manufacturing footprints into Africa”.
So, where would companies start in readjusting their supply chains in this way? At the moment, the region is prime for the cotton segment of the textile and apparel supply chain. That’s why cotton is always a good place to begin. “West Africa is producing 75% of African cotton,” says Vyas. Hence this provides the biggest potential for vertical integration, which is the key to supply chain sustenance.”
He continues: “With the availability of cotton, yarn, fabric varieties within the textile parks and the emerging eco-system, each new process investor brings in an opportunity for backward linkages and forward integration.” Importantly, he notes, increasing demand for sustainable products has fast-tracked the supply chain realignment process.
ARISE is working with a ‘plug-in’ model. Vyas noted at WTiN’s Innovate Zero Carbon event that everything is ready for manufacturing from raw materials to access to waste systems etc, so the vertical integration process should be (in theory) simple enough.
Transparency
As with all new ventures in today’s textile & apparel supply chain, transparency needs to be addressed. Vyas notes the importance of this to ARISE: “The IFC (a World Bank Group Company) is an investor in our park facilities and the park infrastructure has been made in strict compliance with the standards and ESI practices laid out by such strong stakeholders.”
Additionally, the team are trialling FibreTrace technology on their cotton to ensure the validity and reliability of the fibres used. FibreTrace is a provider of digital and physical traceability solutions that uses traceable pigments to accurately trace cotton and other fibres.
The assurance of responsible raw material sourcing is ensured by using CmiA-certified cotton. This certification guarantees compliance with both national legislation and international standards pertaining to human rights, labour practices and environmental regulations throughout the production process, specifically at the farm and gin levels. It incorporates a comprehensive supply chain traceability system employing its Blockchain tool HIP (Hard Identity Preserved), which necessitates the physical segregation and distinct separation of CmiA cotton at every stage of production.
It’s clear to see why cotton is the strongpoint for ARISE and its integrated industrial zones: the crop is available in the region and is one of the most commonly used fibres in the supply chain today. Still, the team is planning to expand to other key materials in the future.
Despite this, there’s no risk for the existing cotton supply chains. Vyas concludes: “So far we have achieved a very good quality product, achieved all the certifications brand have laid out.” He said he perceived “no risk in moving”.
Have your say. Tweet and follow us @WTiNcomment