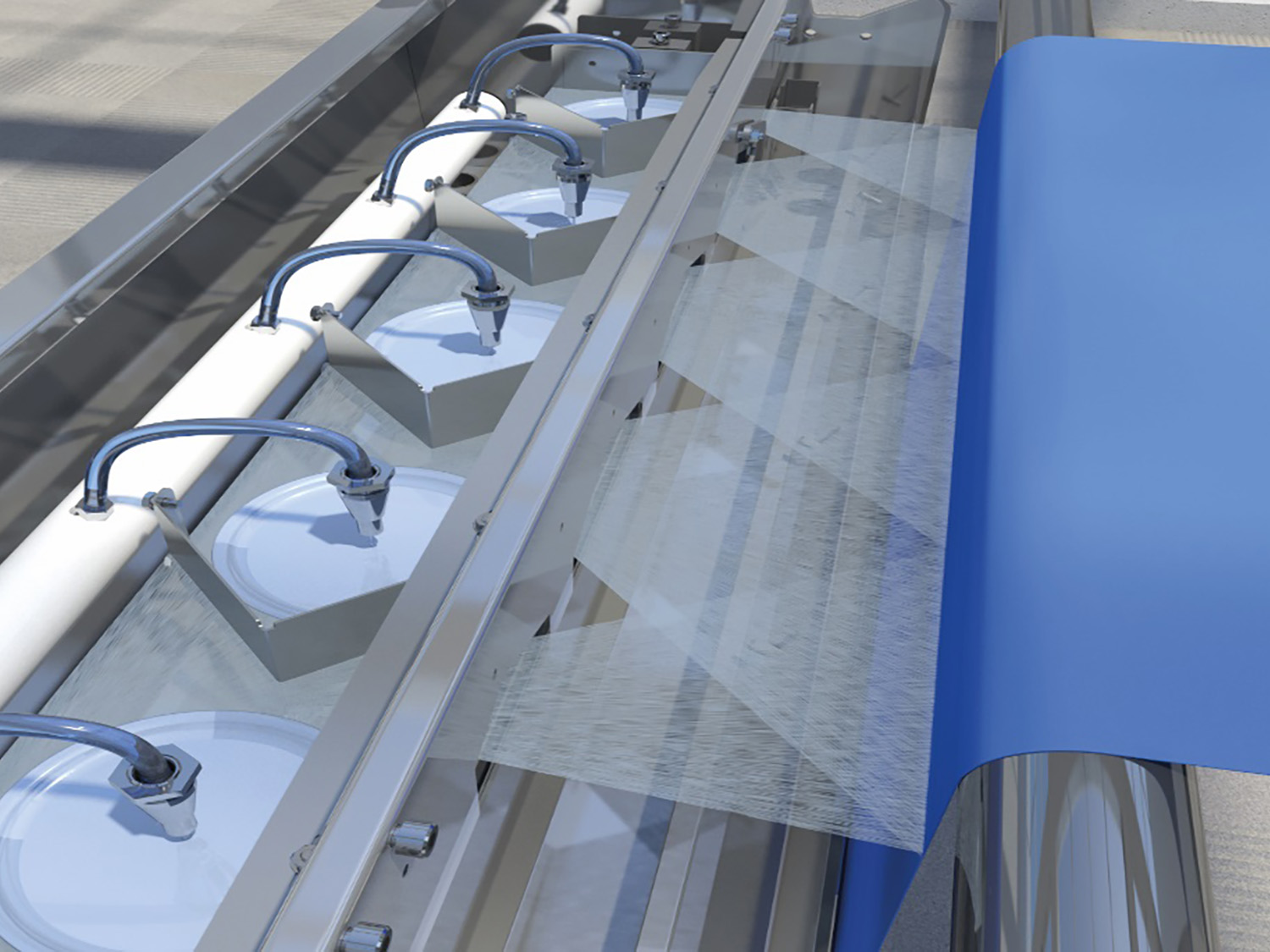
Sponsored by WEKO
As the industry moves away from conventional finishing processes towards more environmentally friendly options, WEKO’s head of technical sales and processes, Jayanta Sanyal, delves into the detail of finishing textiles more sustainably.
Textile finishing is a crucial step in the textile production process that involves various mechanical and chemical methods to enhance the value of the end products. It is the final stage, following preparatory and dyeing processes and improving the fabric’s feel, appearance, functionality and aesthetic features. Textile finishing provides functional properties such as softening, flame retardancy, water repellency, wrinkle resistance, etc, ultimately determining the quality and durability of the fabric.
However, the traditional process of functional finishing involves the use of harmful chemicals and additives, leading to environmental pollution, high energy consumption, and increased costs. In recent years, the increasing recognition of environmental concerns has further emphasised the importance of sustainability within the textile finishing process.
The need for sustainable textile finishing
The global textile market in 2023 was valued at US$1,840bn, according to Grand View Research, and it is projected to experience a compound annual growth rate of 7.6% from 2023 to 2030, reaching US$3,047.23bn by 2030 . The textile industry is currently thriving, and its demand is expected to rise alongside the growth of the global population. Nevertheless, the production and consumption of textiles have significant negative impacts on the environment. The textile industry is widely recognised as a leading contributor to environmental threats worldwide.
Fortunately, there are solutions. The consideration of sustainability plays a crucial role in textile finishing. It not only prevents the depletion and misuse of natural resources but also minimises waste production and significantly reduces production costs. It is decisive to recognise that the future of textile finishing lies in the creation of multifunctional fabrics that are both cost-effective and durable, while also being ecologically sustainable. As a result, numerous textile manufacturers are currently seeking sustainable finishing solutions and processes that utilise natural and safe ingredients, through minimal application techniques, thereby enhancing the value of consumers’ lives.
Traditional fabric finishing in stenter frame:
The stenter machine plays an important role in the textile finishing industry by effectively stretching or stentering delicate fabrics. For instance, cotton fabric tends to shrink in width and length after undergoing bleaching and dyeing processes, which can cause distortions. The primary objective of the stenter machine is to modify the fabric's dimensions to predetermined measurements in both length and width. Textile manufacturers utilise this machine for both woven and knitted fabrics to apply chemicals to impart functionalities and, at the same time, to ensure dimensional stability during heat setting. In the traditional dipping-squeezing technique, one or two padders are used to apply chemicals, leaving 70-130% water at the entry of the stenter frame. Subsequently, six, eight or 10 heating chambers are used to dry the fabric, which consume a very high amount of energy.
Use of WEKO instead of a padder in a stenter frame
WEKO’s precision spray systems use rotary atomizer technology and offer non-contact spray capabilities for finishing and remoistening processes. This advanced system ensures controlled and optimal coverage of liquids to achieve specific and consistent fabric characteristics. By applying the exact minimal amount of water and chemistry needed, water consumption can be reduced by up to 50-70%. This leads to a notable increase in productivity and profitability during the finishing process. Whether working with textiles, non-wovens, or technical textiles, the precision spray technology can effectively handle a wide variety of water-based chemicals including softeners, anti-microbials, water repellents, oil repellents, flame retardants, wrinkle-resistant agents, hydrophilic agents, resins and more.
Advantages of using WEKO over padder
- Contact-free, precise, exact and even application – no bath contamination, non-stop production without stopping for cleaning due to colour change or fabric gsm change
- No tailing, CSV, substantivity issues
- Adjustable penetration – optimum flexibility from surface coating until complete penetration
- WEKO-single-passage technology (single side or both sides, different effect)
- Low pick-up therefore low drying energy (15-30% instead of 70–130%)
- Enabling high speed production
- Fast batch/lot change
- Easy to use
- Excellent reproducibility
WEKO’s wide areas of application
Ranging from 584 mm to more than 7,000 mm width of the web, WEKO is successfully supplying its spray applicators with different fluid supply units for various industries for more than 70 years. WEKO is proudly present in almost every sector of the textile industry.
Other than the most important application of moisture management for shrinkage control in compactor/sanforizer, the most common finishing applications our customers use are:
Outdoor – Single-side water repellent (Fluorocarbon and non-fluorocarbon) – 25-35% pick up (wet-on-dry)
Sportswear – Anti-microbial, hydrophilic treatment, softening 15-20% pick up wet-on-wet
Workwear – Fire-retardant, soil release, oil repellent, softening etc. 15-30% pick up wet-on-wet or wet-on-dry
Denim – Colour fixation, resin treatment, single-side water repellent, softening, tear strength improver, single-side overdyeing/tinting, glossy finish, wet look, etc. It’s also very popularly used in calendaring as well as in peaching/emerising machine. Applications are single or both sides, wet-on-wet or wet-on-dry with minimal application amount, WEKO SIGMA, WEKO NEO and Rota Spray are commonly used.
Terry towel – Mainly used for softening and anti-microbial finishing in wet-on-wet with 15-18% pick up
Carpets – Mainly single-side application for oil- and soil-release finish.
Home textiles – A wide range of finishing is done with high-working-width WEKO SIGMA rotor carrier. Most popular finishes are wet-on-wet softening, anti-microbial, hydrophilic, hydrophobic, soil release, UV protection, etc.
Technical textiles – Varieties of finishing application in automotive textiles, medical textiles, packaging textiles, etc. Usually applied in wet-on-wet or wet-on-dry depending on the requirements of functionality.
Apparel – Very popular and most successful application for knits and woven. Various applications used to be done, but softening is the most common. Our open-width knitting customer in India proudly claims to have achieved savings of 30-35% in chemicals, 50% downtime and 30-40% heat energy in wet-on-wet knit finishing. Our customer’s monthly production report indicates it is now producing the same monthly quantity in 4-5 fewer working days.
Our tubular knit customers in Brazil are successfully producing good quality fabric by spraying softener into a hydro extractor and are claiming savings in softener of around 40% per month.
Nonwoven – WEKO successfully serves all kind of non-woven manufacturing processes (spunlace, needle punch, dry laid, wet laid, melt blown, etc). Because it can be used for single-side applications, it’s widely used for:
- Anti-bacterial / anti-microbial / hydrophilic finish for medical products
- Oil and water repellence for industrial filters
- Hydrophilic finish for fem care and diapers
- Hydrophilic finish for geotextiles
- Fire retardant for automotive interior
- Perfume and lotionising with softening for other non-woven materials
WEKO’s dedicated team effortlessly serves our nonwoven customers and the original equipment manufacturers (OEMs).
WEKO is continuously working for various process development in cooperation and collaboration of European textile chemical companies to find out the right chemicals to make the process more sustainable.
Together with finishing applications, WEKO has developed various dyeing processes for denim yarn dyeing, denim fabric overdyeing, pad spray steam (PS2) cotton fabric dyeing, polyester pigment and disperse dyeing, etc and they are successfully running in production.
WEKO’s product manager, Carolin Russ, talks to the company’s head of technical sales and processes, Jayanta Sanyal, about its latest denim yarn dyeing innovations
Specific solution for specific requirement
WEKO provides a range of solutions for manufacturers, as indicated in the chart below.
WEKO’s R&D team is working to develop and launch another system according to our customers’ requests and requirement of specific industry segments.
Conclusion
Manufacturers, brands, and retailers are increasingly prioritising sustainable practices in manufacturing, sourcing, vendor selection, and more to ensure the end product reaching consumers is produced in an environmentally friendly manner. Traceability and circularity are crucial aspects of this.
As resources are becoming scarcer, sustainability has emerged as a key focus in the nonwovens and textile industry. Emphasis is placed on finishing processes that are both material and resource-efficient, yet effective. There is a growing demand for specialised and individual finishings, with future products expected to offer specific and unique functions across various industrial sectors.
Increased production flexibility is necessary, while reducing the consumption of chemicals, water, and heat energy is essential for sustainability and profit optimisation. Research suggests that widespread adoption of sustainable finishing processes in the textile industry is necessary to mitigate the environmental impact of conventional methods.
The trend towards eco-friendly and sustainable clothing is on the rise, as consumers increasingly prefer such products. As part of its commitment to a better world, WEKO is actively promoting awareness among industry stakeholders and consumers about the benefits of embracing sustainable practices. Let us work together towards a more sustainable textile industry.
Have your say. Tweet and follow us @WTiNcomment