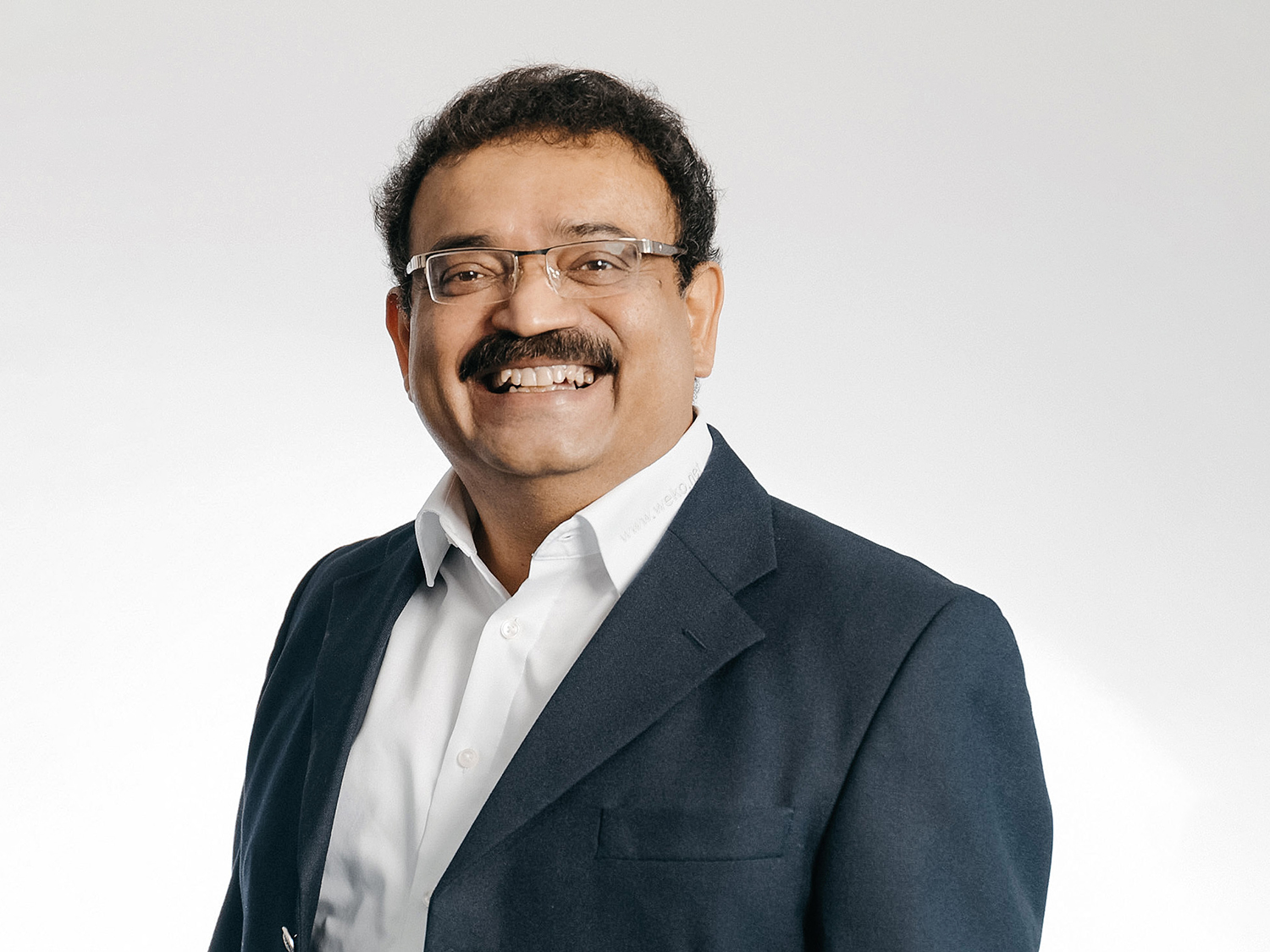
Sponsored by WEKO
WEKO has been manufacturing and supplying powder and fluid application systems for various industries (and the textile Industry stands out as a major vertical), since 1953. The company's success in precise moisture management solutions inspired it to step into chemical applications for textile finishing. WEKO's non-contact minimal rotor spray application system quickly gained popularity, proving to be a precise, high profitable and sustainable finishing solution for textile mills. This success led to numerous requests from mills seeking assistance in the dyeing process. Innovation and development of different dyeing processes have continued. Since acquiring RotaSpray in 2021, both companies within WEKO Holding are consistently working to meet customer needs for textile dyeing.
WEKO’s latest developments revolutionise the entire cotton and cotton/nylon dyeing process in terms of CO2 and chemistry reduction. Due to the non-contact rotor spray application, dyes and auxiliaries are applied homogeneously on one or both sides. The penetration level can be adjusted by exact dosing of the spray quantity and selection of the correct auxiliaries as required.
Abstract
Today’s common Pad-Dry-Pad-Steam process (PDPS) is the most popular continuous dyeing process for cotton fabrics with reactive and vat dyes and is mostly used by all the manufacturers in traditional textile countries for mass production.
Benefits:
The PDPS process covers the entire colour space in all colour depths which is reproducible under certain conditions.
Limitations include:
- The process requires a very high amount of salt in the dyeing recipe – this leads to ecological problems
- It’s not suitable for small batches due to the strong tendency for lengthwise tailing at the beginning of the lot
- The huge intermediate drying is not only a very expensive process, but also emits huge amounts of CO2, thus making the process non sustainable
In 2017, RotaSpray started developing a concept to reduce the salt, tailing, chemistry and energy consumption in the dyeing process, replacing the chemical padder with their non-contact rotor spray application. This process was branded as the PS² (Pad-Spray-Steam) process.
Development and industrial implementation of the PS² process
Pad-spray-steam is the combination of padding and non-contact forced rotor spray application as a two-bath process followed by steaming of the fabric. This revolutionising process change allows for important benefits:
- Eliminating the intermediate drying process
- After padding with reactive dyestuff, a non-contact spray application of alkali and soda completely eliminates the stripping of dyestuff in the second padder (the chemical padder)
- Due to the non-existence of stripped off dye molecules in the chemical padder, re-exhaustion is not necessary which eliminates the use of Glauber salt for light to medium shades and is reduced drastically for medium to dark shades
- Dramatically reduced start-up waste
- Cost efficient and easy repeatable short lot production
- No contact – no hydrolysis of the dye molecules
- No contact – no substantivity issue
- A scope to increase the pH value in the dyeing recipe significantly increases the reactivity of the reactive dyes. This leads to reduced energy consumption in pad steam processes and to drastically reduced throughput times in dwell processes like the pad spray batch process
A 2018 bleeding-edge technology has been converted to trustworthy and futuristic technology in less than five years: PS² process for woven fabrics (salt minimised)
Aiming to move towards carbon neutral dyeing and to make the process eco-friendlier and more efficient, a straightforward lab method was created in collaboration with a high end Pakistani customer and its skilled team. This method simulates the PS² process using existing lab padding technology. The dye solution is applied to the lab padder through a trough method, and then fixing chemicals are applied using a wet-on-wet nip dyeing method. This ensures consistent results when scaling up from the lab to bulk production. Practical experience has demonstrated that the spray technology is easily replicable with the current lab padder equipment, specifically through the trough/nip approach.
The PS² process, implemented in February 2019 at this Pakistani textile mill, differs from traditional PDPS. Since inception, the production ranges from 800,000 to one million metres/month, using reactive and vat dyes. In both colour systems, the dyestuff solution is padded, while the fixing chemicals are sprayed in a wet-on-wet contact-free manner on both sides, with application rate of approximately 18-26%. For single side dyeing, the fixation chemical is padded and colour solution is sprayed on one side.
The PS² process eliminates the second padder and intermediate drying, reducing CO2 emissions by ca. 1,331 tons in the first year. Two new spray systems were commissioned in March 2023, adopting the pad-airing-predry-cooling-chemical spraying-steaming-washing concept for vat dyeing and darker shades of reactive dyeing. A bleeding-edge technology of 2018 has been converted to trustworthy and futuristic technology in less than five years.
The PS² dyeing process boosts productivity and energy efficiency while minimising shade variation and tailing during start-up. Traditional processes often face tailing issues due to hydrolysis and substantivity effects of the reactive dyes, but PS² significantly reduces this problem.
The spray application in PS² involves four front and four back fabric spray contacts, using a specific method for different dyes like soda ash/caustic soda method for reactive/caustic; hydro for vat dyeing. This adaptation, along with a wet-on-wet additional application, cuts tailing length from 15 to 150 metres compared to the PDPS process. This improvement increases the fresh packing during inspection; therefore the profitability also increases.
Furthermore, PS² allows for small batch dyeing or sample lengths without running a full bulk batch, offering flexibility to the product development and sampling team.
To mitigate the dilution effect caused by wet-on-wet padding and spray application, which leads to reduced fixation yield in darker shades, it is advisable to add up to 80 g/l of Glauber's salt to the spray solution. However, when dyeing light to medium shades, the use of salt is not necessary.
The PS² process enhances washout resistance of reactive dyed fabrics and reduces water usage by lowering salt concentration. No intermediate drying minimises the risk of dye migration, ensuring even penetration and high-quality results, though optical colour depth may slightly decrease due to increased diffusion.
The new standard: Pad spray steam for denim yarn (salt free)
The PS² process on warp yarn (sheet/slasher dyeing) has been established in continuous dyeing with reactive dyes for several years. Today it is mainly used in the fashionable area of denim yarns in countries such as Turkey, Pakistan, India and China. Reactive dyes used on denim yarn are mainly utilised when bleeding or during wash-down in the finished wash, otherwise the subsequent household wash is not desired, especially as a differentiation from classic indigo-dyed jeans. The exception is fashionable colour looks, in which a reproducible spotty, poorly dyed yarn is deliberately produced in the spray dyeing process by correcting the spray parameters. After weaving, a wash-down effect is created without the use of bleach or destructive laser effects. The fixing alkali is padded, the reactive dye is sprayed onto the yarn without contact as a forced application and then steamed and washed. Effects of dyestuff substantivity, which caused strong tailing effects on classic dye boxes with 400 – 1200 l liquor contents, are eliminated by use of contact-free spray of fixing chemicals. The residual liquor quantities are reduced to less than 50 l when changing colours or can be completely reused.
In conclusion, the PS² technology of cotton fabric continuous dyeing by WEKO/RotaSpray is a revolutionary advancement that enables manufacturers to make significant progress towards achieving carbon neutral dyeing on a global scale. This innovative technology not only minimises carbon emissions but also enhances the profitability of manufacturers.
WEKO and RotaSpray is committed of taking gradual steps towards a more sustainable textile industry.
Have your say. Tweet and follow us @WTiNcomment