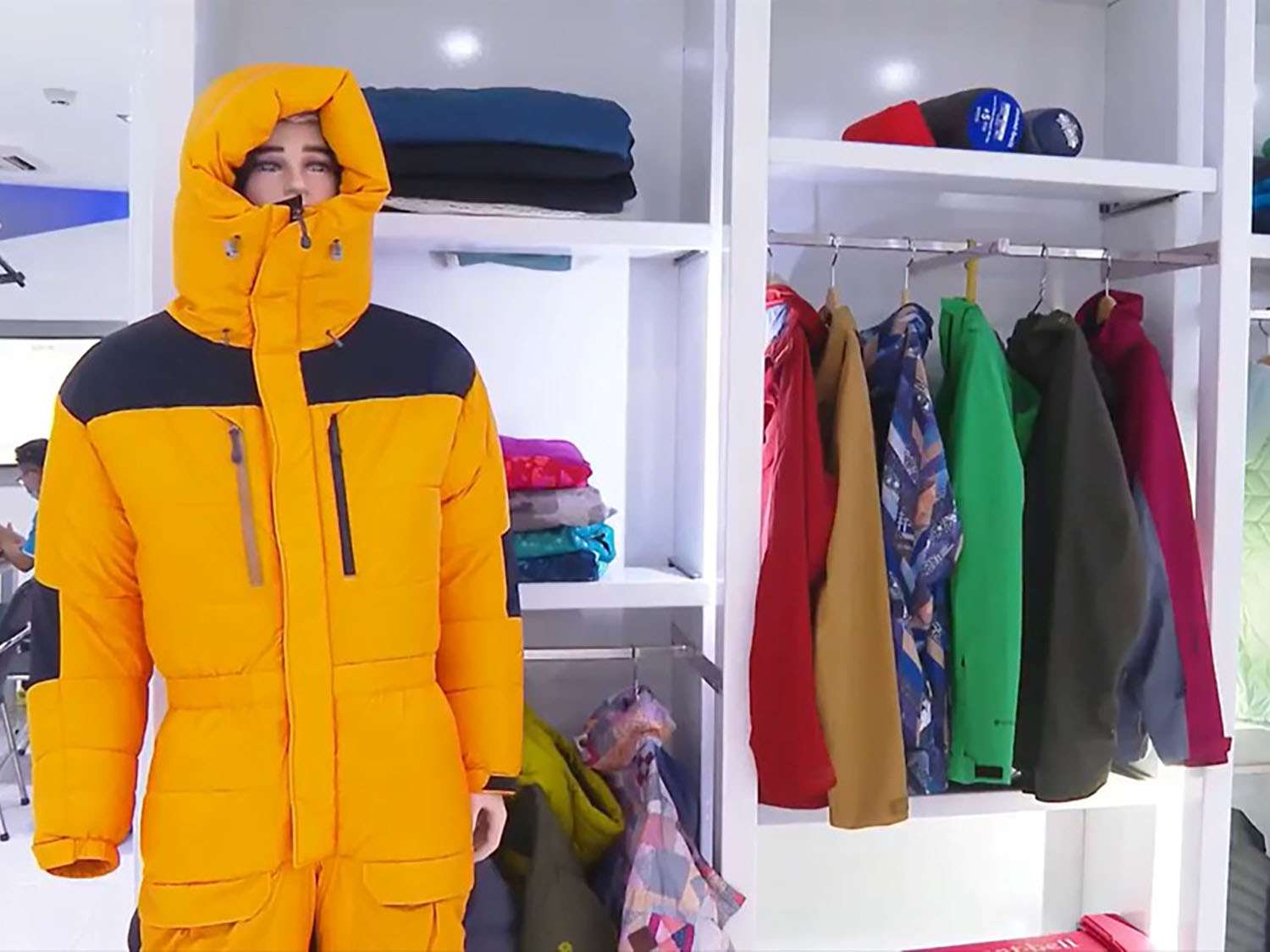
Sponsored by Taiwan Textile Federation (TTF)
Ad. by TITA
Global leading, vertically integrated, outdoor clothing manufacturer Kwong Lung Enterprise speaks to WTiN about its sustainability initiatives and certification achievements.
Taiwan’s textile industry is performing well globally. In recent years Taiwan has demonstrated strength and success in its supply chain, as the country’s textile manufacturers have become strategic partners for many international brands.
A key advantage lies in Taiwan’s vertically integrated supply chain; from raw material to garment manufacturing, Taiwanese companies have developed efficient and flexible processes. Kwong Lung Enterprise (KLE), for example, is a vertically integrated outdoor clothing manufacturer, which was the first down processing company in the world to pass Bluesign Certification, a sustainability standard for the production of textiles.
And this year became the only listed company in Taiwan to achieve B-Corporation certification, showcasing its high standards of social and environmental performance, transparency, and accountability.
Since 2009, KLE has adopted green sustainability initiatives, with strength lying in its knowledge of functional outerwear, strict quality standards, strong research and development (R&D) capability, and production.
With its headquarters in Taiwan and production base in Vietnam and Indonesia, KLE achieved a B Impact score of 80.2, the median score for ordinary businesses who complete the assessment is currently 50.9.
Adoption of new technologies
The business achieved this through a range of forward-thinking, future-proofing initiatives, one being its adoption of 3D pattern-making technology.
A spokesperson for KLE said: “The main advantage of 3D technology is to increase speedy and efficiency. Rather than waiting for physical prototypes, branding clients can directly work with the digital models and respond quicker, which helps reduce sampling lead time.”
3D technology has enabled KLE to make samples without using fabrics and trims, reducing its environmental footprint.
“The popularisation of 3D pattern-making technology is bound to happen, while physical samples are still sometimes required when there is doubt whether 3D technology can precisely present visual output and fitting,” the spokesperson added.
The textile industry is rapidly moving towards greater digitalisation and technological advancements, from design and production to supply chain management. Not only is KLE adopting new technologies, but it is also investing in Artificial Intelligence (AI) driven quality control systems, and integrated enterprise resource planning (ERP) systems that allow for optimisation of production processes.
KLE’s reputation
KLE has built long-term partnerships with some of the most “promising and premium brands globally,” including snow brands, Burton, Volcom, Obermeyer; outdoor functional brands, Marmot, Mountain Hardwear, Vaude, Mont-bell, Fjallraven; tactical outerwear, 5.11.
“We provide one-stop shopping by producing broad types of outwears for our clients, including Gore-tex garments, taping garments, down jackets, padding jackets and sleeping bags,” said the spokesperson.
KLE specialises in garments with “functions”, such as its Gore-tex jacket or down jacket, which feature a huge number of details including noise pockets, 2-way cuff systems, and zipper vents. KLE’s production plants are certified by GORE to produce Gore-tex garments for high-end outdoor functional apparel brands.
A great example of how KLE’s expertise has been used is in its collaboration with Volcom to produce the official uniforms of the US Snowboard Team in the Olympic Winter Games 2022.
The spokesperson said: “With highly functional and sophisticated features, the uniform weaves together cutting edge, patented proprietary technologies, and bio-based sustainable materials into designs that are meant to function for peak performance.”
Elsewhere, KLE has worked with branding clients to develop new and innovative products helping them win ISPO awards. For example, the Marmot WarmCube 8000M Suit, which uses WarmCube technology – small, cube-shaped boxes filled with down, providing comfortable warmth to the highest level, took home one of these awards.
Production systems
Currently, KLE is exploring new opportunities with fast-growing, medium-sized and bigger high-end brands that want to develop functional clothing. To meet its customers’ needs KLE has adopted a production model that has the flexibility to take on smaller orders. The Toyota production system, which has been in place since 2014, works as a U-shaped production line to reach economies of scale even with a small order volume.
The system breakdowns KLE’s work structures and is created from the bottom up, with comprehensive training for each new employee. It extends from Chairman to senior managers, and plant managers, and to line operators. The system assists in streamlining work processes eradicating non-value-added procedures, allowing for defect feedback and operating in the minimum time needed.
“The implementation of Toyota Production System equips us with high production flexibility to take on smaller volume orders while managing multiple items. On average, we could reach economies of scale with a single order size over 1,600 – 1,800 pieces,” said the spokesperson.
The main challenges KLE is facing, currently, are rising production costs and global competition. To combat this KLE said it will utilise automation and advanced manufacturing technologies to improve production efficiency and reduce labour dependency. Due to competing with manufacturers in countries with power production costs, such as Vietnam, Bangladesh, and China, KLE has a constant challenge. The business focuses on high-quality, innovative and sophisticated products, which offer added value that low-cost competitors cannot easily replicate.
Additionally, as global consumers become more environmentally conscious, partnering with Taiwanese companies allows brands to align with sustainability goals and appeal to eco-minded customers. Many companies have adopted environmentally friendly practices, such as using recycled materials, reducing water and energy consumption, and implementing waste reduction strategies, having obtained international certifications such as Bluesign, GRS, Higg Index and Oeko-Tex. Sustainability not only benefits the environment but also enhances the industry’s global reputation.
Sustainable and ethical production continues to be crucial to the textile industry. In its Vietnamese factories, KLE is implementing energy-efficient processes, reducing water usage, and ensuring its production methods meet high environmental and ethical standards.
“We are committed to staying at the forefront of these changes, ensuring that we remain competitive and responsible as the industry evolves,” the spokesperson said.
Have your say. Tweet and follow us @WTiNcomment