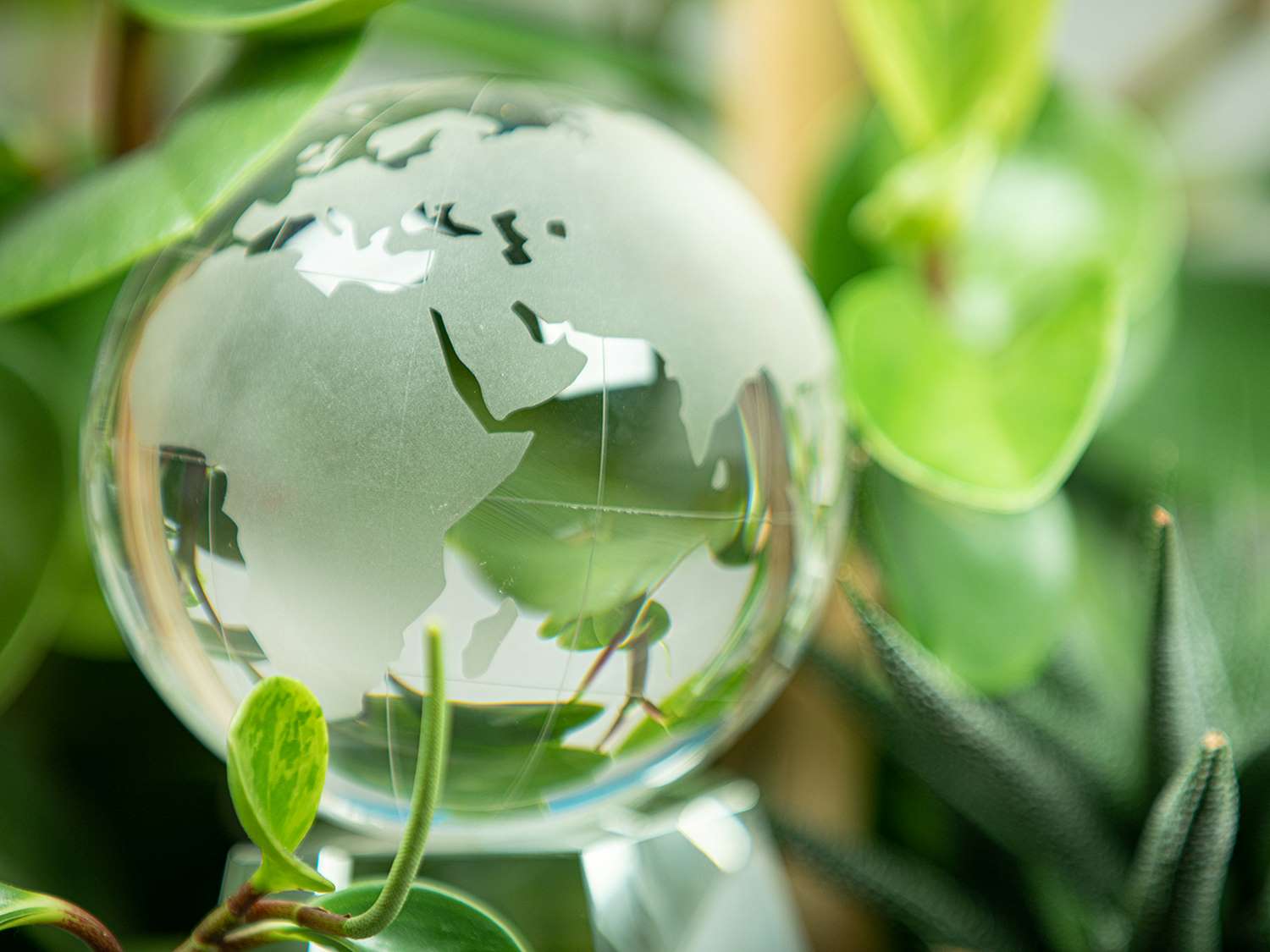
Sponsored by Triveni Turbines
Steam turbines are critical to textile production, but how can they contribute to a greener industry? WTiN speaks to Mr SN Prasd, CEO of India-based manufacturer Triveni Turbines about the advantages of using its products.
The textile industry depends on steam turbines to power machinery across various stages of production. As the industry evolves and environmental regulations gain prominence, many manufacturers are exploring steam turbines as a solution for sustainable energy.
Triveni Turbines, an industrial steam turbine manufacturer based in India, emphasises that its products are designed to support the use of cleaner fuels and enhance energy efficiency.
"While the initial capital investment for steam turbines may be substantial, they offer significant long-term savings through optimised energy usage, reduced fuel consumption, and lower maintenance requirements compared to other power generation systems," Triveni Turbines CEO Mr SN Prasd explained.
The company also highlights the advantages of cogeneration, or combined heat and power (CHP), in improving energy efficiency.
"CHP is an incredibly efficient way to produce both electricity and heat simultaneously," said Prasd. "In textile plants, steam turbines are often integrated into cogeneration systems to maximise energy usage and minimise overall energy costs. The excess heat generated during electricity production can be used for steam generation, heating, or other industrial processes, thus increasing overall energy efficiency."
One of India’s fastest-growing global conglomerates, with textile units in Maharashtra (Palghar) and Gujarat (Vapi and Anjar), has been a long-standing customer of Triveni Turbines.
In 2015, the Vapi-based textile plant approached Triveni Turbines with a need for steam and power, as its existing gas turbine-based power plant was no longer viable. The plant required steam at two pressure levels – 36 bar and 8.4 bar – and a power output of approximately 14 MW.
Triveni provided support from the conceptual phase right through to the installation of a coal-based 15 MW steam turbine generator designed for cogeneration applications.
After detailed consultations with Triveni and external consultants, the customer opted for inlet steam pressures and temperatures of 110 bar and 535°C. The customer then issued a tender for a 15 MW cogeneration plant, engaging leading consultants from Bengaluru for both the textile machinery and power plants.
The project faced challenges, including limited space and a tight 10-month deadline. Triveni Turbines secured the contract following a rigorous technical evaluation, which considered turbine efficiency, heat rate, and the overall scope of supply.
Despite the spatial constraints, Triveni successfully installed the steam turbine, even accommodating large equipment such as mobile cranes and Hydra machines.
In 2021, the customer once again turned to Triveni to adapt the steam turbine to new process demands, which altered the plant’s power and steam requirements. The project resulted in a new output of 13.5 MW. Triveni modified the steam path, decommissioned the old system, and conducted a successful performance guarantee (PG) test for the updated turbine.
Triveni Turbines also worked with a leading Indonesian manufacturer of viscose fibres, providing steam turbines to meet both its process needs, such as drying threads and mixing raw materials, and its captive power generation requirements.
"Steam turbines provide the essential energy for heating and drying within these processes," said Prasd. "In particular, steam is used for warming water during fibre washing, drying yarn or fabric after dyeing, and fixing dyes or finishes during the finishing process."
Triveni supplied a 5.5 MW back-pressure steam turbine generator with an inlet pressure of 44 bar and an inlet temperature of 450°C to meet the customer's heating needs, which enabled the manufacturer to expand its capacity in two phases. The expansion included a 12 MW extraction condensing turbine and a 22.5 MW bleed cum extraction condensing turbine, each optimised for efficient energy use.
Advantages of steam turbine technology
Triveni Turbines’ steam turbine technology offers numerous benefits, particularly within CHP systems. These turbines provide reliable, continuous operation with minimal maintenance, making them ideal for industries requiring constant power and heat. Additionally, CHP systems are scalable, allowing them to meet specific power and heating demands in various applications, such as drying threads and mixing raw materials.
One key advantage of steam turbine-based CHP systems is their ability to recover and use waste heat from the turbine exhaust for heating purposes. This significantly improves overall efficiency and reduces greenhouse gas (GHG) emissions, making them a more environmentally friendly option than separate heat and power generation systems.
Steam turbine-based CHP systems can also offer valuable grid support, improving the stability and reliability of the electrical grid.
There are incentives and policies in place that encourage the adoption of CHP systems, including those powered by steam turbines. These incentives, which may include financial aid, tax credits, and regulatory support, enhance the economic attractiveness of steam turbine CHP systems for businesses and industries.
In the UK, the Renewable Heat Incentive (RHI) is a government scheme that provides financial incentives to businesses, public sector organisations, and homeowners to install renewable heat technologies, including CHP systems that use renewable fuels like biomass or biogas. Under this scheme, participants receive payments based on the amount of renewable heat generated, making it more economically viable to invest in CHP systems. The RHI aims to reduce GHG emissions by promoting more efficient and low-carbon energy solutions like CHP.
For more information, click here.
Have your say. Tweet and follow us @WTiNcomment