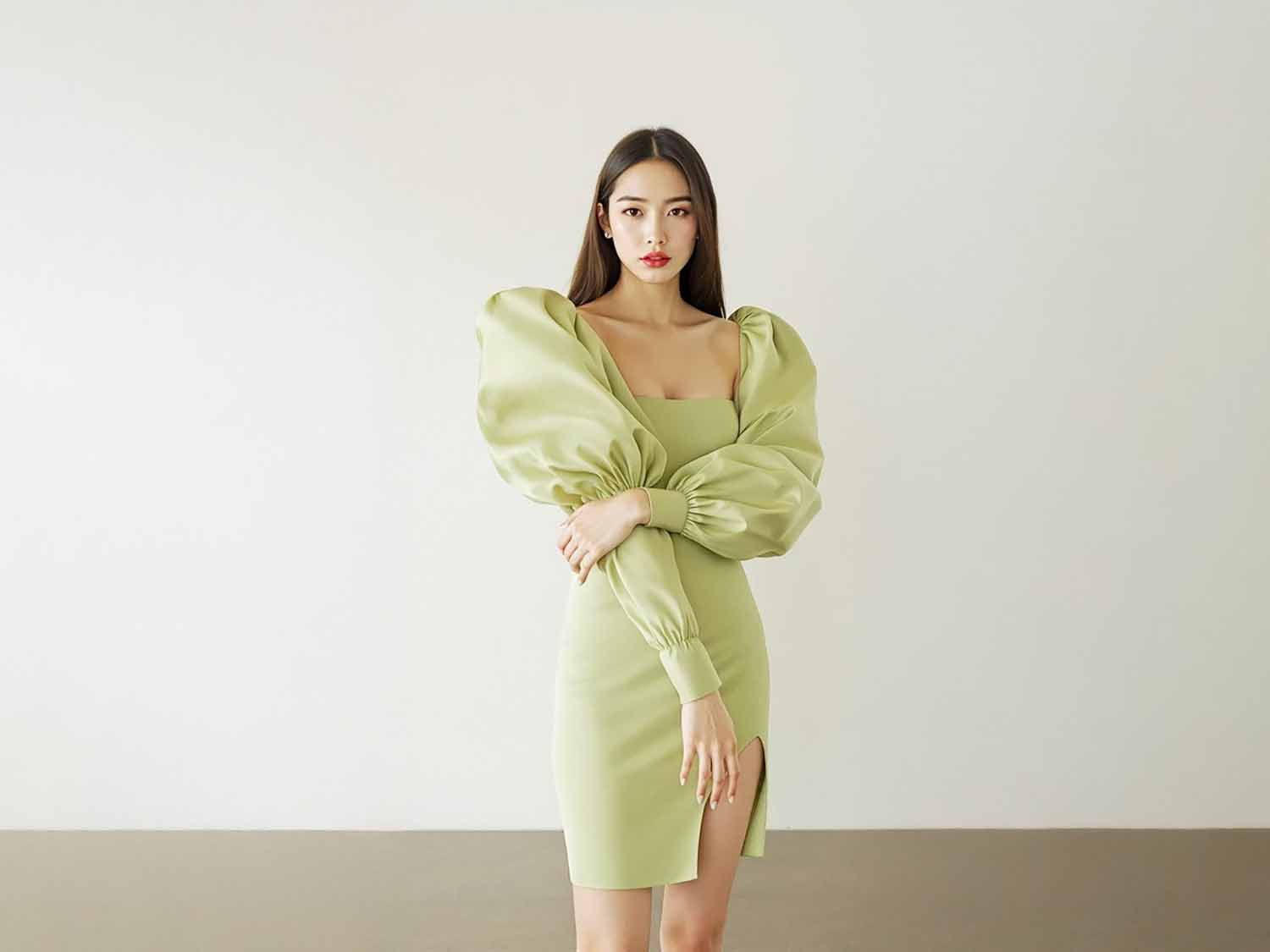
-
Understanding the commercial readiness scale
WTiN’s Commercial Readiness Scale gives an indication of what stage of commercialisation a product is at. It ranges from Emerging: a research stage development; Scaling: the product is being produced on a small but growing scale, and Commercialised: the product is well-established and ready to purchase.
A Swedish startup is launching in February to revolutionise fashion by merging AI-powered design with circular manufacturing.
Launching this February is Gryning, a circular platform designed to integrate artificial intelligence (AI)-driven circular product development with a vertically integrated European network of on-demand suppliers.
The Sweden-headquartered startup works exclusively with recycled cellulose-blended fabrics, avoiding synthetics and blends in materials. Its aim is to achieve 100% recycled content from post-consumer textile waste.
Siri Vikman, CEO at Gryning told WTiN: “We’ve made the technology accessible to creators, who can now design their own garments through a split revenue-share model, exploring the creator economy and democratised design. We have already signed several fantastic creators in the Nordics who have begun product development, and the feedback so far has been amazing.
“Beyond production, we envision a parallel platform focused on Circular Services, such as resale, remake, repair, rent, re-dye/print, and recycling, offering brands and consumers a comprehensive solution for circular operating models.”
In January Gryning achieved its first major milestone - its debut fabric made with recycled content. The fabric is composed of 49% Ecovera, 41% certified Viscose and 10% Circulose, all of which are circular materials, and have been woven in Turkey.
Vikman said: “Once we found the right material, we collaborated closely with spinners and weavers to develop a fabric that met our requirements for circularity and quality. Starting with light woven fabrics, one of the most technically difficult categories, made the process even more complex.”
It took Gryning three months to develop the fabric and early on the company found limitations in the recycling infrastructure and so had to source recycled content from post-industrial waste. Additionally, the team discovered most recycled fabrics cannot be recycled a second time and so needed to collaborate with a scientist who is currently trialling new recycling technology for cellulosic materials.
“It required constant innovation and problem-solving across the supply chain. This milestone wouldn’t have been possible without strong partnerships and a shared vision with our collaborators to push the boundaries of what recycled textiles can achieve,” added Vikman.
The challenge then comes for achieving the same durability and performance as virgin materials. Chemical recycling of cotton often results in weaker viscose when compared to virgin cotton fibres. While mechanical recycling can produce short, damaged fibres that lead to issues such as reduced durability and increased pilling.
But by collaborating with spinners and weavers Gryning hopes to ensure greater control when overcoming the aforementioned challenges. And moving forward they hope to expand Gryning’s mono-material catalogue, including protein-based fibres such as wool, silks and protein-based biomaterials, which the team plans to incorporate later this year with the launch of its knitwear category.
“Achieving 100% recycled content from post-consumer textile waste is a long-term goal, and we’re addressing it step by step by designing with recyclability in mind and collaborating closely with recyclers, spinners, weavers, and scientists to test innovative technologies,” said Vikman.
The company was founded by a diverse team of four, bringing together expertise in fashion, innovation, AI, technology and law. They have built startups, launched fashion brands, and worked with likes of H&M Group, Tesla, Klarna, and IKEA.
“We’re proudly self-funded, which allows us to maintain our vision and move rapidly to transform the fashion industry through AI-driven circular product generation and circular production methods,” added Vikman.
Another aim of Gryning is to enable designers to create their own garments using Gryning’s AI tool Saga. Saga works by analysing a creator’s style and translating their vision into garments designed for circularity. Saga has been built to ensure all designs use circular materials stocked with Gryning’s suppliers and has been optimised for circular production.
Vikman said: “Saga is highly scalable and has already been embraced by creators who’ve produced thousands of designs. While it’s not public yet, the response so far has been overwhelmingly positive.”
Throughout the textile supply chain, we are observing higher demand for on-demand production and reducing waste. This is being driven by consumer demand and incoming legislation, such as Digital Product Passports (DPP). Digitalisation for optimised production models are becoming more widespread, to create greater efficiency and less waste in manufacturing, as is material innovation, such as biorecycling.
Yet, alongside these opportunities the industry faces systemic challenges, from overproduction, the challenges to recycle true post-consumer textile waste, to water pollution, CO2 emissions, and over consumption.
Vikman outlined nine key challenges in the industry, across the supply chain. She said the global material basket is still heavily reliant on oil-based, fossil fuel-derived materials such as polyester. Polyester, derived from fossil fuels, drives greenhouse gas emissions during extraction and production, sheds microplastics into waterways with every wash, and is nearly impossible to recycled effectively – especially when blended with other fibres.
“Its non-biodegradable nature means it lingers in the environment for hundreds of years, contributing to long-term pollution,” she explained.
Vikman also said unrealistically low prices driven by offshore production have led to labour exploitation, environmental degradation and a disconnect between consumers and the true cost of garments. At the same time, declining durability and quality have shortened product lifespans, fuelling overproduction, overconsumption and increasing waste.
She added: “The textile supply chain remains highly fragmented, making it difficult to track the journey of raw materials and products. A lack of transparency and digitalization hinders accountability and progress toward sustainability and circularity goals. If you don’t know, you cannot act.”
To start combatting these challenges Gryning is uilidng its own version of a DPP, which it will expand and refine over time. The goal is to reach a granual level of traceability in everything the company does, ensuring full transparency across the supply chain.
“This approach allows us to track materials and processes in detail, ensuring accountability and enabling informed decisions that align with our circularity goals,” said Vikman.
In the near future Gryning is preparing for its February launch and is “happily bootstrapping”. Looking further ahead the company may explore external funding to expand outside of Europe to scale up its vision.
Have your say. Tweet and follow us @WTiNcomment